
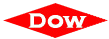




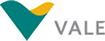

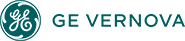




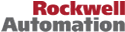

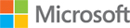
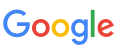

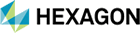


The influence of information technology (IT) on operational technology (OT) affects every area of industrial automation, from connected smart sensors to virtual software deployment. The Industrial Edge has become the place where OT meets IT, serving as the bridge between two disparate technology cultures that connects new and legacy industrial systems to the IT world.
Today’s logic, process, and motion control solutions consist of a myriad of software applications installed across various systems and smart devices. While these systems and devices are easily connected, using contemporary IT technologies, they often have special requirements and priorities that cannot be addressed with standard IT tools and practices. Bringing together the worlds of IT and OT requires an environment with tools that considers these requirements – a sort of last mile for industrial machinery. This is the emerging role of the Industrial Edge.
This ARC Strategy Report takes a close look at recent developments around industrial edge devices that use software-defined machinery automation (e.g., soft PLC), and:
The Industrial IoT Edge is a platform that can add value to existing automation systems. This value is derived from the ability to centrally roll out apps and manage applications and devices deployed on plant floors. This is important because the amount of software on the plant floor will grow significantly as automation architectures become more IT-like, automation applications become more software-defined, and users deploy more home-grown apps.
Edge and cloud-native computing enables the creation of new digital services that allow automation suppliers to service their systems in the field, or machine builders to monitor the performance of their equipment in faraway plants. In either case, digital services can help reduce equipment lifecycles costs for end users, while machine builders gain new aftersales revenues streams.
Ever since the Industrial IoT Edge emerged as “the place” where IT meets OT, many new edge devices have appeared on the market, to address machinery automation applications (PLC, motion, CNC, robots) and, in parallel, IoT applications such as condition monitoring. These devices often use “Edge” or “IoT” in the product name as well as “Edge Computer/Edge Computing” or “Edge Controller.” Contrary to traditional automation devices like PLCs, edge devices offer features known from the IT-tools landscape. The following section outlines key edge concepts.
Investments in edge computing are mostly driven by the need to increase the overall equipment effectiveness (OEE) of manufacturing assets and processes. Most edge devices are IPC or embedded controls, based on x86 technology. Once these are installed close to the production machinery, this question arises: Why not replace the traditional PLC with a soft PLC and save the costs of the PLC CPU? A soft PLC leaves the remote IO, sensors, drives, motors and other actuators in the machine, but executes the PLC (or motion control, CNC, robot) as a software application running on an edge device. Other concepts are to execute the PLC application from a company’s on-premise server. The challenges of such concepts are numerous, and this Strategy Report takes a closer look at them. But first let’s look at the edge segmentation.
To better understand what kind of edge devices have been introduced to the market, ARC has screened many supplier portfolios and established an edge segmentation:
Whenever there is a soft PLC, soft motion control, soft CNC or soft robot control included in an edge device, ARC uses the term “software-defined machinery automation” (SMA).
Suppliers of edge devices use various terms such as controller, computer, or platform. There is no standard or common understanding when to use which term for an edge device. The ARC edge segmentation offers a clear differentiation for naming edge devices.
These platforms host pure software products that are applied throughout all edge segments. ARC publishes a Market Analysis Report on Industrial IoT Edge Software Platforms. Please contact your client manager if you are interested in this report.
Hyperscalers like Microsoft (Azure IoT Edge) or Amazon (AWS IoT Greengrass) have dominated this segment, but now automation suppliers like Siemens (Edge Management), Rockwell (Factory Talk Edge), Bosch Rexroth (ctrlX OS), and TTTech Industrial (Nerve) are gaining momentum.
This segment includes devices that by default have an SMA (e.g., soft PLC) for machinery automation on board. Further to the machinery automation capabilities, IIoT Edge Automation Controllers are equipped with the means to feed digital data to upstream edge devices, or to local or remote clouds. Processing of IoT related applications, like data analysis, may be possible, but is limited to not interfere with the real time machinery automation execution. To avoid risking performance dips in the machinery automation, IIoT applications executed on the same CPU are limited. The main purpose of such Industrial IoT Edge Automation Controllers is still machinery automation.
ARC Advisory Group clients can view the complete report at ARC Client Portal
If you would like to buy this report or obtain information about how to become a client, please Contact Us