
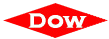




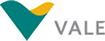

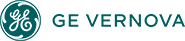




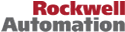

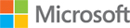
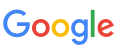

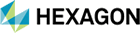


As new open process automation systems are developed and commercialized, manufacturing companies, automation suppliers, and engineering contractors face both the opportunity and challenge of developing automation projects with new approaches. Advances in automation technologies create new opportunities for all stakeholders to lower both the replacement and ongoing lifecycle costs for their control systems and derive more value from automation investments.
To date, however, only a small minority of these benefits have been realized due to a hesitancy to try something new, invest in new technology, or change existing business practices. Too many automation stakeholders are trapped in the mode of doing things the same way they have always done them. This reluctance to change minimizes the value of automation investments and prevents manufacturers from realizing opportunities to drive inefficiencies out of their plants/processes and taking their operations to the next level of performance.
At the recent ARC Industry Forum in Orlando, Florida, this theme was evident in the New Approaches to Automation Projects session. The session examined how emerging automation technologies and new approaches to project management now make it possible to significantly reduce overall project cost for everyone involved. The presentations centered around how smart, configurable I/O, virtualization, modular approaches, and main automation contractor (MAC) approaches offer the potential to reduce project costs by as much as 30 percent if everyone involved approaches the project with an open mind and appropriate new technologies/business processes are implemented correctly.
Thomas Holm, committee member for NAMUR, began his presentation by stressing that modular production and decentralization are key elements of both Industrie 4.0 and IIoT architectures.
Mr. Holm’s idea of modular production included the development of modules that offer a specific functionality or function (i.e., mixing, feeding etc.). Each of these modules must include its own intelligence. Once the modules are developed, the production process is created by combining pre-assembled modules in a row to form a process. The row of modules is then coupled on a backbone, which includes a Process Control Layer (PCL). One of the key challenges to this approach is designing in the ability to quickly reassemble and model an automation system in the PCL without the traditional need for expensive and time-consuming customized programming.
Mr. Holm’s proposed that the solution to this challenge lies in developing Modular Type Package (MTP) files that include:
He went on to explain the optimal situation, which would involve having the MTP files generated automatically by parsing the program code included in each module and looking for patterns in the code.
Seven working groups have already developed around this activity, with 25 companies involved in NAMUR recommendations development for modular automation. Current working groups include: Alarm Management, Archive, State based process control, Technology, Standardization, Human Machine Interface, (HMI), and Diagnosis/Maintenance. Companies involved come from a diverse background, including DCS suppliers, sensor/actuator companies, end users, remote I/O suppliers, module and plant manufacturers, and universities/associations.
The modularization concept was first developed in 2014. Requirements and case studies were developed throughout 2015 and the first half of 2016, including comparing and defining the technologies involved. Demonstrations of this approach began in the second half of 2016, with true process control schedule to follow later in 2017.
Hyonsook Kang, retired project manager and engineering manager for Shell, focused her presentation on the key considerations for scoping modernization projects. A common theme that resonated throughout Ms. Kang’s presentation was the importance of maintaining a vision of what constitutes success throughout the project. In her presentation, she encouraged everyone involved in the project to continue asking themselves what success would look like at the end of this project and what needs to be done to accomplish this vision?
Ms. Kang began her presentation by offering a checklist of the key questions users should ask themselves when considering whether to modernize or maintain an existing control system. Key questions included:
While answering these questions, Ms. Kang stressed the importance of carefully considering how a possible accident could affect the company in terms of workforce safety, equipment damage, and loss of reputation. She reminded the audience that, as the market becomes increasingly globalized, an incident that occurs in Nigeria could have implications on the company’s activities in Alaska. Ms. Kang also stressed the importance of using modular procedural automation to automate the knowledge transfer to help mitigate the risk posed by the aging workforce.
David Hoeppner, Control Systems/Electrical Department Manager for Fluor, discussed the opportunities available for those willing to embrace new technologies and develop new work processes to reduce the cost and complexity of automation projects. Mr. Hoeppner maintained that the traditional engineering method is too cumbersome and includes too many time-consuming interdependencies. To reduce cost and unnecessary dependencies, Fluor teamed with key automation suppliers to create a new approach. This starts from the bottom up and uses new technologies to develop new work processes designed to optimize the engineering and design phase of automation projects. A key element to Fluor’s approach is using new technologies available to dictate how the project is executed, rather than choosing automation products based on traditional work processes.
Mr. Hoeppner stressed that all too often, the basis for project design is what has traditionally been done, including using outdated technologies and excessive specifications that can add layers of unnecessary cost. He encouraged everyone in attendance to incorporate a fit-for-purpose project design approach and apply industry standards and standardization in design. According to Mr. Hoeppner, this approach works best when everyone involved starts with a blank sheet of paper and develops the processes based on the new technology.
Mr. Hoeppner asserted that the biggest hurdle to reducing cost and complexity of automation projects is the pure reluctance to change with the technology. He mentioned the oft-repeated quote attributed to Einstein: “Insanity is doing the same thing over and over again and expecting different results...We cannot solve our problems with the same thinking we used when we created them.” To break free of this paradigm, he encouraged the audience to never be afraid of trying something new and strive to take advantage of the benefits offered from new technology advancements that allow end users to get control systems off the critical path on projects and reduce costs. To be effective, however, Mr. Hoeppner suggested these changes be driven by management from the top down.
A rallying cry for change was a common theme expressed by all presenters in this session. New automation technologies and work processes can bring significant economic benefits, but a lot of the future success for end users will depend on their ability to embrace not only new technologies but the new work processes that are essential to their success.
As long as the industry continues to implement traditional technologies and work processes, we will continue to be burdened by the unnecessary costs, complexities, and inefficiencies of the past. New approaches and implementation of new technologies, are required to take the industry to the next level of performance. Standards organizations with strong input from the end user community, like NAMUR, are a great example of how end users themselves can drive change in the technologies offered by automation suppliers.
ARC also expects that supplier companies, engineering firms, systems integrators, and technology licensors will be forging closer relationships as they continue to try to drive out cost and complexity not just from automation solutions, but from the holistic view of the plant and the process. The big innovations in industry and technology happen when knowledge from one discipline is applied to another discipline.
If you would like to buy this report or obtain information about how to become a client, please Contact Us
Keywords: ARC Industry Forum, Open Process Automation, Main Automation Contractor (MAC), NAMUR, Human Machine Interface (HMI), ARC Advisory Group.