
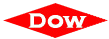




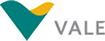

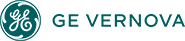




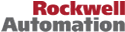

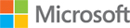
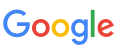

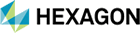


The electrification of mobility and transportation will continue to accelerate because industry, business, and society at large are accepting the clear reality that the industrialized world must eventually move away from burning fossil fuels. But nowhere will the impact of electric vehicles (EVs) be felt more immediately and expansively than in the global automotive industry.
Options for both individual transportation and more flexible human mobility are being electrified at a rapid pace, with an increasing number of all types of traditionally fossil-fueled vehicles making the transition to electrification. ARC Advisory Group research indicates that this trend will continue to accelerate well into this decade and beyond.
With more all-electric vehicles now hitting the personal vehicle market, the growth is also surging in trucks, buses, and industrial/agricultural vehicles. While it will be difficult to accurately predict future sales of EVs, a combination of increasing demand for more environmentally friendly vehicles and government mandated restrictions in emissions is compelling automotive OEMs to significantly increase production rates. The shift from internal combustion engine (ICE) vehicles to EVs will have a profound and transformational effect on automotive manufacturing operations and their suppliers. Moreover, this shift will significantly impact global automotive industry employment patterns.
The flood of EVs rolling out over this decade will have much fewer parts and assemblies than today’s gas-powered cars and trucks. Moreover, there will be a complete shift from the powertrain manufacture of ICE vehicles to EVs, not to mention battery assemblies and other electrical systems and components; and that will radically change the automotive production processes, manufacturing technologies, the overall automotive supply chain, and the car-making workforce. This transformational shift will most certainly cause some disruptions to the industry, but it will also afford opportunities to reinvest in U.S. manufacturing as companies move to a green economy.
Designing and building s to replace ICE vehicles presents a formidable set of design and manufacturing technology challenges. It not only requires a new set of technologies to address the electrification of the vehicle, but also converting existing ICE factories as well as building new factories to manufacture s exclusively. Additionally, car makers must completely rethink vehicle engineering and the vehicle experience for the driver, while maintaining the existing “DNA” of their car brands as they convert iconic brands to electric drives.
Building an electric car is different in a multitude of ways. Fully electric cars don’t have multi-speed transmissions, radiators, fuel injectors, gas tanks, gears, crankshafts, or exhaust systems to name just a few differences. When compared to an ICE vehicle, drivetrains have much less parts and components. While conventional ICE drivetrains can have as many as 2,000 parts, electric drivetrains can have as few as 20.
Clearly, the difference in parts and system composition will define production requirements for manufacturing and the eventual factory layout and processes. A traditional ICE manufacturing system would consist of powertrain production (transferee lines to produce engine parts and components), sheet metal stamping, body-in-white assembly, chassis and powertrain fitting, and general assembly. Many production processes for body, chassis systems, and interiors would be comparable between ICE vehicles and s.
In manufacturing the primary components replacing ICE powertrains would be battery packs and electric motors. The battery pack consists of modules that contain battery cells, a battery management system that monitors performance, thermal management to control battery temperature, interconnects, and housing units. The multi-speed gearboxes used in ICE vehicles are replaced by single speed transmissions because in s the power output of electric motors is more efficient and consistent across a much broader range of RPMs than conventional ICEs. In other words, hit the pedal in a and you get almost instant torque. In addition to the powertrain, the other significant category is power electronics. This covers all the equipment essential for running s like DC to DC, DC to AC converters, and power electronics controllers. All of this represents completely different production processes, equipment, and systems to make the vehicle.
While switching from manufacturing an ICE powertrain frees automakers from the complex and labor-intensive fabrication and assembly process of engines and transmissions, the car companies will need to master an entirely new set of manufacturing processes for s. An electric car requires a completely redesigned electrical system that includes different wire harnesses, coiling, sealing of wiring, and quality assurance for the more complex electrical systems. This represents a significant change for an industry that has spent over 100 years developing and optimizing engine manufacturing and vehicle assembly to very high levels of efficiency.
An entirely new aspect of manufacturing is the integration of battery packs. Automotive OEMS routinely assemble battery packs in-house by piecing together battery modules. However, the cells that make up the battery modules are typically produced by specialized suppliers, often from the consumer electronics industry and headquartered in APAC. Delivery of those cells to OEMs requires a well-functioning supply chain, since the car makers cannot store large inventories of battery modules, because of potential fire hazard and the degradation of batteries over time. As a result, the OEMs must create a well-functioning just-in-time production process for battery pack integration.
New materials are becoming a factor in the manufacturing transformation to s. While reducing vehicle weight to help meet tightening fuel economy requirements is an ongoing process in the auto industry, manufacturers will be focused on this issue even more because the battery pack platforms are extremely heavy, and deterrent to range capacity between charges. For example, the battery pack of a Tesla Model S weighs over 1000 pounds. To deal with the extra battery weight much of Model S body is made of aluminum. However, aluminum is trickier to work with in a production environment making stamping, forming, and welding more difficult.
Expect the car makers to use more and varied materials going forward to solve the weight problem. Advanced composites are already being used by OEMs for body parts. Auto makers like BMW are producing bodies made of carbon fiber composite for their i3 and iX electric models and are making prototypes of monocoupe 3D printed bodies. The smaller lightweight s will be the norm for urban environments while larger models with longer range will serve longer distances between charges. The common manufacturing factor will be newer lightweight materials.
As automotive OEMs make the transformation from ICEVs to EVs, deployment of the workforce will be a critical factor in this transition. The growth of EV manufacturing in the U.S. could drive a renaissance for auto workers, creating new skillsets, training opportunities, and higher wages. The downside could be a smaller workforce and layoffs for workers unable to make the transition to a completely new form of manufacturing processes. At this juncture, the latter is highly unlikely as the global automotive industry makes the historic manufacturing transformation to electric transportation and mobility. They will require a fully engaged and retrained workforce to make this transformation.
As car companies re-tool and convert ICE production lines and build completely new greenfield factories dedicated to EVs, it will provide the opportunity to build these new production facilities with the latest smart manufacturing technologies and processes. |
As labor needs change, automotive companies will need to conduct extensive workforce planning to evaluate the impact of the shift to EVs on their workforce, and assess which employees can be retrained for the totally different skillset required for building a EV. Many car companies have already accomplished many aspects of this workforce transition, or are heavily involved in the process. EU car makers and Chinese companies are significantly ahead of the U.S. auto makers at this point, but U.S. car makers are very actively engaged in this workforce transition, with most making a commitment to electrify most or all of their models. U.S. car company, Tesla, has been building EVs for almost a decade and has established a workforce from the ground up. New EV startups have already tapped into the automotive workforce and have initiated retraining programs concurrent with converting brownfield automotive production lines to BEV manufacturing plants.
Accompanying the transition to EV manufacturing will be a wave of new technologies that will enable smart factories. As car companies re-tool and convert ICE production lines and build completely new greenfield factories dedicated to EVs, it will provide the opportunity to build these new production facilities with the latest smart manufacturing technologies and processes. This will also enable the new EV workforce to be incorporated and trained directly into the smart manufacturing environment and become an internal component of this transformational change.
The electrification of mobility will be broad and involve many modes of transportation beyond just light vehicles. While the established global automotive industry is making the ICE to EV manufacturing transition, many startup companies are emerging that are manufacturing all modes of electric transportation from long-haul trucking to commuter aircraft.
In addition to EV OEMs, the automotive manufacturing supply chain will undergo significant change and to some extent disruption as the demand for electric vehicle components rapidly increases along with the overall market demand for BEVs from the automotive consumer.
Manufacturers across all areas of transportation should be aware that the long-term outlook is for the electrification of all modes of mobility. ICE powered vehicles that depend on fossil fuels will eventually be phased out, although that will take at least two decades. Meanwhile, the technology of electrification will continue to progress, enabling a host of opportunities for new business and manufacturing advancement.