
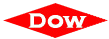




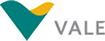

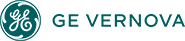




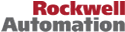

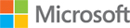
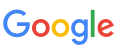

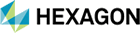


What do plant safety and asset performance management (APM) have in common? As attendees learned in the well-attended “Minimizing Safety Risks with Asset Performance Management” session at ARC Advisory Group’s recent Industry Forum in Orlando, Florida, the two fit together “like a hand in a glove.” Asset performance management minimizes risks on safety. Attendees learned how the proactive view of risks provided by many APM solutions enable industrial organizations to implement an effective, enterprise-wide risk assessment and process hazards analysis program. Ensuring the reliability of the communication network provides the foundation for improving asset performance and ensuring safety in remote locations such as offshore platforms.
Based on the session presentations, ARC recommends the following actions for owner-operators and other technology users:
The significant benefits enabled by the Industrial Internet of Things (IIoT) can only be realized if communication is reliable. When considering managing assets, one’s attention is drawn directly to the asset without considering the reliability of the asset’s communication network. In his presentation, Mr. Maamor, Principal Instrumentation and Control Engineer at Petronas, reminded session attendees that while asset reliability is the ultimate goal, it can never be assured if network communication is unreliable.
A fully integrated oil and gas multinational based in Malaysia, Petronas employs over 15,000 people to operate its more than 80 development projects around the world. The company’s operations include 130 onshore and offshore rigs, 23 FPSO/FSO units, six LNG projects, and four unconventional assets. Improving the safety and reliability of asset management was the project goal for Petronas. The project’s objectives were to assess the performance of a long-distance ISA100.11a wireless communication system in an offshore environment and test the performance and interoperability of the system for wireless gas detection.
Located in the South China Sea 130 kilometers offshore, the Zuhal unmanned platform was selected to demonstrate the reliability, interoperability, and delivery of full wireless functionality over a long distance due to its remote location and harsh operating environment. Other project considerations included signal transmission distance of five kilometers and the potential for signal interference caused by steel structures on the rig. System hardware included a gateway, two access points, multiple pressure transmitters and gas detectors, four repeaters, and four high-gain antennae. Petronas employed Yokogawa’s web-based FAST/TOOLS system architecture for system management, control, and visualization.
Received Signal Strength Indicator (RSSI) and the Packet Error Rate (PER) were designated as test metrics. During the six-month test period, the system maintained an approximate signal strength of 60 dbm and 0 percent PER. This demonstrated the robustness of the ISA100 Wireless Standard for long distances in a harsh environment. Perhaps more importantly, the test demonstrated that plug-and-play interoperability of different vendor products in the network is achievable.
The Petronas team believes that its research has proven the concrete benefits of ISA100 Wireless in safety applications. These include delivering cost reductions and operational flexibility. The research also demonstrated that ISA100 Wireless can deliver full wireless functionality in mesh, star, or mixed topologies.
At the close of the session, Mr. Andre Ristaino, Managing Director, ISA100 Wireless Compliance Institute presented the Institute’s 2015 Excellence in Automation Award to Mr. Maamor and Petronas for this research project, citing that it quantified the performance of an ISA100 Wireless based safety system at an offshore operational site.
According to ARC safety experts, while safety system practitioners are concerned about adherence, they are not leveraging their efforts to deliver benefits over the lifecycle of the system. For example, proof test results, audit findings, and logbook notes are generally not stored in an integrated, sharable, and searchable manner; rendering this a non-reproducible, one-off activity. The danger lies when complacency sets in, since even when nothing obvious appears wrong, conditions can imperceptibly change. Assets get older, the risk profile may become elevated, or the control strategy may change; making the as-commissioned and as-tested state of the safety system invalid.
Comprehensive safety lifecycle management can improve the repeatability of the process, reinforce the desired behavior, and help reduce overall safety risk. However, timeliness is crucial. The pertinent data must first be collected, documented, and acted upon. Most importantly, the results must be recorded and integrated with tangential systems. Related testing must be performed in a reliable and repeatable manner. Changes in control strategy may require a change to the layers of protection analysis (LOPA) to determine if the existing safeguards are adequate. By having a more realistic view of the safety profile, owner-operators may uncover the opportunity to extend asset life.
Enterprises in all industries profess that safety is their top priority and state that it is the responsibility of all employees. However, reliability is gaining ground as evidenced in Tuesday’s General Session Executive Panel discussion where each member of the panel cited reliability as the most important thing to them. An important distinction between the two is that process and employee safety are heavily regulated; reliability is not.
The goal of a safety culture is to avoid incidents and accidents. In a reliability culture, the emphasis is on preventing failures. Although the goals are different, the synergies between them are obvious. For example, to be successful, both require a commitment from the highest levels on the organization. Behaviors that ensure safety and reliability are so embedded in daily activities that they become second nature. Roles and responsibilities are clearly defined, communicated, and understood. Periodic audits and adjustments are made accordingly based on measureable metrics. Root cause analysis (RCA) is applied to eliminate asset failures and plant incidents and training is ongoing.
Industry statistics indicate that 44 percent of errors related to safety instrumented systems (SIS) and safety instrumented functions (SIF) occur during the hazards assessment and specification in the design phase of the lifecycle. Many of these errors occur because SIF/SIS designers incorrectly consider interactions of one SIF to the rest of process. An APM solution can help ensure effective safety system design and management by assessing integrity level requirements, performing integrity level verification, conducting proof tests, and providing continuous monitoring to ensure actual failure rates comply with specified failure rates as designed.
Based on ARC research and analysis, we recommend the following actions for owner-operators and other technology users:
KIf you would like to buy this report or obtain information about how to become a client, please Contact Us
Keywords: Asset Performance Management (APM), Industrial Internet of Things (IIoT), Reliability, Safety Instrumented Systems (SIS), ARC Advisory Group.