
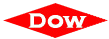




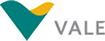

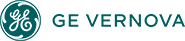




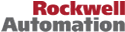

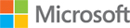
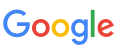

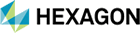


Keywords: Capability Matching, Siemens, Teamcenter, BOPEX, Distributed Manufacturing, ARC Advisory Group.
Manufacturers today are faced with a host of new challenges, ranging from global supply chain issues to a lack of available skilled personnel. Many are looking for ways to do more with fewer resources. “More automation” used to be the answer, but a more effective solution is to make the factory more flexible.
One way is to employ adaptive, modular production concepts in which machines and equipment can be reconfigured to adapt to changing production needs and market demand. While many production lines today are “smart” enough to handle rapid reconfiguration, they often remain rigid, connected to other machines via the handling equipment installed between them.
This ARC View looks at a solution that addresses these needs by letting the manufacturer assess the availability and capabilities of equipment and plants, and then choosing the optimal production path.
A bill of process (BOP) describes how to make a product, detailing the line configurations, tools, machines, and equipment needed. If the BOP is the recipe, then the bill of materials (BOM) is the list of ingredients. The management of BOPs and BOMs used to be a set of error-prone manual steps, but is now a fully integrated part of product lifecycle management (PLM) software such as Siemens Teamcenter. A bill of process execution (BOPEX) takes this process to the next level.
A BOPEX engine guides individual batches of products along the production process, selecting the optimum path by matching the capabilities of available equipment to the requirements outlined in the BOP.
Using “advanced capability matching,” the BOPEX identifies, allocates, sets up, and triggers the equipment. It also breaks up the classic, rigid production line by replacing hardcoded production logistics (pipes, conveyors, fixed automation) with smart AGVs and real-time software-based production coordination, similar to the batch engine defined in ISA-88 batch process control. BOPEX also supports modular type package (MTP) units, which are flexible by definition and therefore fit in nicely with the BOPEX concept.
The BOPEX configuration consists of a capability model, routing constraints, inventory levels and an imported BOP for each product. Equipment allocation is performed by a capability matching algorithm that uses hard and soft constraints to identify the best equipment available.
When a production process step is complete, the smart carrier containing the WIP reaches out to BOPEX and asks for help. BOPEX looks up the capability in the next step of the BOP (e.g., MIXING), then makes a request to the production modules, asking for a response from any equipment that can provide the MIXING capability. The dialog looks a lot like a WhatsApp chat (see screenshot below from the BOPEX Production Monitor).
The list of tentative capability providers is filtered by status, for example:
Availability: Is it reachable by smart carrier from current location?
Hard constraints: Can it mix at requested speed and time? Does it have the correct amount of the required material?
From this, a short list is optimized (closest, least CO2, etc.). BOPEX allocates the chosen capability, then calls the logistics system (AGV, robot, smart conveyor, pumps and pipes) to move the smart carrier to the target equipment. On arrival, BOPEX downloads the setpoints (mixing) or a part program (machine tool), then triggers the capability.
If the constraints are met, BOPEX doesn’t care if the mixing is done by a mixer, a robot with an agitation end-effector, or an operator with an electronic work instruction. Should the equipment break, BOPEX reroutes automatically to keep production moving.
A bill of process execution can manufacture multiple products simultaneously in the same flexible cell. In the screenshot below, small lots of shampoo, conditioner, hand cream, face cream, and body lotion are being concurrently manufactured on-demand:
The example mentions typical process industry tasks like mixing, but BOPEX is used across a wide range of other industries such as CPG, battery manufacturing, aerospace & defense, automotive, and medical devices.
Because BOPEX runs at the heart of production, it can easily track material as well as environmental parameters like CO2 footprint and energy usage. The BOPEX engine is available commercially via a SaaS model and can be deployed at the edge in a docker container.
The old rivalry between product design and manufacturing departments was laid to rest when PLM software enabled error-proof electronic BOPs and BOMs that enable continuous coordination between designers and makers. Now, a platform-based solution like BOPEX takes the process one step further by allowing manufacturers to assess their production and automation resources, and then select the optimum path through the plant based on asset availability and equipment capabilities. This also has implications for decentralized and distributed manufacturing models, which we will explore in a future ARC View.
ARC Advisory Group clients can view the complete report at the ARC Client Portal.
Please Contact Us if you would like to speak with the author.
Obtain more ARC In-depth Research at Market Analysis.