
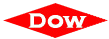




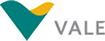

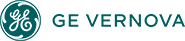




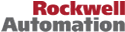

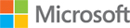
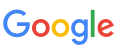

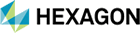


The New Space Race, or simply New Space as it is commonly referred to, is a rapidly expanding industry covering several industrial manufacturing fields focused at utilizing the recently rediscovered arena of space to advance business interests. New Space is seeing interest from companies seeking to put communications, observation, lab packages, test beds and potentially mining into space, and is showing no signs of slowing down. Driving this billion-dollar industry are a wide array of businesses and visionaries looking to reach out and grow this burgeoning industry with the potential to change the course of humanity.
Traditional aerospace frames have seen a revolution in the last thirty years. Designs have been pushed to maximize flight and weight characteristics using new designs and materials. This can mean anything from increased efficiency for turbofan assemblies inside of jet engines to new bracing structures running along aircraft wings to reduce weight and increase fuel efficiency. One of the notable changes in aerospace design has been an acceptance of additive manufacturing into both the manufacturing and design process. Modern engines have complex geometries that are perfect for additive manufacturing, as these engines are developed and revised to increase power, performance, or efficiency for a more sustainable future. 3D printed parts incorporating technologies like Design for Additive Manufacturing (DfAM) and Generative Design allow engineers to push for more out of their production parts. Designers see increased adoption of additively manufactured parts for both internal and external components. These parts are not just limited to standard civilian airliners either, they also see adoption in drones, military aircraft, helicopters, sea-based planes and spacecraft and satellites for extraterrestrial activity. Repeatedly, additively manufactured parts prove to be an efficient, reliable, and in some cases, better part than can be created through traditional manufacturing options. Additively manufactured parts still must undergo a strict process to be certified for use, and any changes in the design of parts for airframes or their composition must meet a strict requirement for certification. However, the ability to further lighten aerospace parts while maintaining or improving on the stiffness of the part has led to many manufacturers looking to adopt these designs into their airframes if they haven’t already.
This comes down to three main advantages in additive. First, material choice allows for end users to print a variety of parts, either polymer or metals, in several different ways. Aerospace for external parts usually relies on metal blends, but these blends can be tweaked to achieve better results based on the characteristics of the part. Second, the design process of additive manufacturing, including the printing of the part, can be tweaked to allow new structures and supports the internal design that would be either impossible or expensive to mill. Finally, the additively manufactured parts can be more efficient in their design and construction, allowing multiple components to be integrated into one part.
ARC Advisory Group clients can view the complete report at ARC Client Portal
If you would like to buy this report or obtain information about how to become a client, please Contact Us
Keywords: Additive Manufacturing, New Space, Low Earth Orbit, Rockets, Launch Package, Satellites, Combustion Chambers, ARC Advisory Group.