
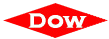




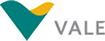

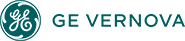




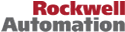

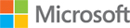
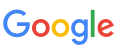

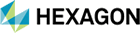


Technology is changing, and fast. Labor availability and skillset requirements are changing as well. In the process industries, the process control end user makeup and skillsets have evolved over decades of iterations. At the 2017 ARC Industry Forum in Orlando, ARC Advisory Group hosted a session in which three end users discussed their respective companies’ process control roles, challenges, and possible responses to those challenges.
Janet Brightwell from Dow Chemical spoke first, followed by Dex Dutson of Lamb-Weston. Andy Young of Pioneer Energy completed the session. Ms. Brightwell and Mr. Dutson provided insights from the perspectives of established businesses, whereas Mr. Young discussed what it was like starting from scratch, leveraging current technologies.
Ms. Brightwell provided attendees an overview of process control at Dow. The company’s diverse nature requires that process control handle all manner of control: batch, continuous, and discrete. Process control also requires knowledge of field devices, field networks, operator interfaces, application layer interfaces, as well as maintain process knowledge.
Dow is unique in that, until the mid-1990s, it developed and maintained its own process control system: the MOD5. It has since adopted commercially available systems, but its installed base is enormous and process control personnel must still support the legacy installations until they are migrated.
Traditionally, Dow recruited chemical engineers as process control staff and taught them to code. The role has expanded to include information technology (IT) and it is getting difficult to achieve the right balance. Through its state-based control approach, Dow has institutionalized its operating discipline into the control systems. However, the company has begun relying on external resources and is developing methods to protect its intellectual property. Dow remains committed to maintaining in-house proficiency, but struggles to find the right balance between in-house and outsourced expertise. The company is also assessing individual expertise versus organizational expertise and how to leverage organizational expertise across the enterprise.
Moving forward, Dow looks to embrace new technologies in the context of supporting its core competency of producing chemicals safely. In doing so, it expects to maintain an appropriate ratio of direct versus contingent staff, as well as between control system expertise versus plant operating knowledge. Technology will be evaluated as either adding value, or not. The company looks to shift to a mindset that integrates running the plant and running the business. In making this transition, it expects to put forth a greater effort to manage the variability and complexity involved.
Dex Dutson introduced the current challenge as an inflection point in the same vein as the Industrial Revolution. He believes that success will be determined by the individual business’ reaction. Plants rely heavily on automation and everything that goes with it. This automation continues to increase in complexity. Knowledgeable professionals are retiring, and new workers want to work differently. This has put too much responsibility into the hands of too few people.
Thus, operations must adapt because the status quo won’t work. Technology is quickly outpacing the on-site knowledge base. IT and OT (operational technology) groups continue to function as siloes and must be bridged. The demographic dynamics are quickly changing. Although more automation means fewer manual tasks and higher efficiencies, it also requires more technically competent operators and better trained technicians.
Lamb-Weston is looking to leverage system integrators (SIs) more. SIs provide a second set of eyes and provide a larger experience base to draw from. As such, it is important to identify what skillsets should be outsourced versus kept in-house. In fact, Mr. Dutson stated that his organization would take on some of the responsibility for ensuring SI personnel were properly trained. It is also looking to promote a security culture, just as it does for safety. More focus is required to ensure the availability of good data to improve reporting throughout the organization. This requires a better understand of information technologies at the automation level and a blurring of the division between IT and OT organizations.
Mr. Dutson closed with an interesting comment, “Challenge a Millennial. Tell them they can’t do something and see what happens.” He believes that Millennials tend to get a bad rap, but they’re pretty resourceful. Look for adaptability as a key characteristic in new hires.
Pioneer Energy is a young company based in Colorado. It is a service provider and original equipment manufacturer that solves gas processing challenges on the oilfield by developing and deploying new technology. Its business revolves around mobile gas processing trailers that the company operates remotely. Andy Young, Director of Remote Operations, presented.
Due to its youth, the company built an organization without the baggage of organizational history and could leverage current (rather than legacy) technology. When considering organizational makeup, Pioneer integrated seemingly disparate departments: Design, Fabrication, Process Control and Operations. This created more collaborative working relationships. Due to the organization’s size, it has greater need for high-quality people. Pioneer doesn’t have an IT department, existing employees must fill this role, which means the employees must possess a wider range of skills. The company also leverages outsourced resources for specialized expertise.
On the technology side, Mr. Young spoke about selecting the best tool for the job, rather than the best platform. He used the term “atomicity” to describe this. Due to the geographic dispersion of equipment, the company placed a high priority on network connectivity. All technologies must support remote operations. Networking, however, only matters if the “glue” is in place in the form of familiar and flexible protocol(s) for communications. This provides personnel with a single view of the assets and reduces complexity.
Three different end users with different backgrounds and from different industries presented on the challenges of the process control role within their organizations. We can attribute the similarities and contrasts in the presentations to company history and culture.
ARC recommends the following actions for owner-operators and other technology users:
For more information, look for the video of these presentations on the ARC Advisory Group’s YouTube Channel.
If you would like to buy this report or obtain information about how to become a client, please Contact Us
Keywords: Process Control, Staffing, Human Resources, Skillsets, OT, IT, ARC Advisory Group.