
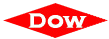




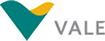

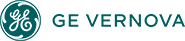




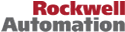

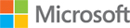
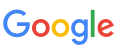

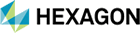


A typical distributed control system (DCS) consists of functionally and/or spatially distributed digital controllers capable of executing from 1 to 256 or more regulatory control loops in one controller “box.” The sensor I/O can be integral with the controller or located remotely via a field network. Controllers currently available have extensive computational capabilities and, in addition to continuous control (e.g., PID), generally can also perform logic and sequence control.
A DCS may employ one or several workstations and can be configured at the workstation or by a networked personal computer. A control network with transmission over twisted pair, coaxial, or fiber optic cables handles local communication. A server and/or applications processor may be included in the system to provide system services as well as additional computational, data storage, and reporting capability.
A DCS begins at the sensor I/O and extends through controllers, application processors, workstations, PCs, and the networking equipment falling within the process control network domain. PLCs and PLC-type controllers sold as part of an integrated system offering may be included. DCS controllers that perform PLC functions only and replace PLCs in an integrated system are included.
Field instruments, control valves, analytical devices, specialty measurement equipment, and any other devices that exist outside the I/O level of the system are excluded. Also excluded are dedicated supervisory workstations that execute applications such as advanced control, production management, real-time optimization, simulation, or plant asset management.
Hardware specifically includes all controllers, application processors, I/O modules, workstations, and communications networks. PCs used for system configuration and real-time control are included, as are computers used for supervisory control, if sold as part of the system. PLCs sold by DCS suppliers that are integrated with the DCS are also included.
DCS software includes control, Human Machine Interface (HMI), systems management software, engineering and configuration software, and plant information management (PIM) software such as bundled data historians. Software excludes optional supervisory software that performs production management (MES) and advanced control functions.
Quality control systems (QCSs) for paper, plastic sheet, and similar web product manufacturing applications may also be included.
Project services include all services provided by DCS suppliers for installing, configuring, and commissioning. Services provided by direct employees of DCS suppliers are included.