
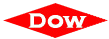




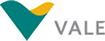

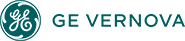




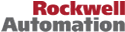

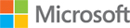
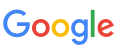

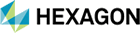


The recent ARC India Forum in Bangalore included a number of interesting and insightful sessions about the latest trends in manufacturing, all showing India manufacturing seeing innovations. This Insight covers three such presentations. Lokesh Payik Head of Smart Manufacturing (General Manager), Bosch, discussed that manufacturing company’s journey to Industrie 4.0; Chandrashekar Bharathi, Managing Director, Ace Micromatic, spoke about his company’s advanced manufacturing decision support system; and Jeetendra Bhavrani, Additional Deputy Manager (MQA) and R.S. Kulkarni Deputy General Manager (MF, GS & MPC), Nuclear Fuel Complex (NFC) provided insights into the company and some of the advanced manufacturing processes it has implemented to ensure quality.
The presentations all stressed the importance of Industrial Internet of Things (IIoT) and Industrie 4.0 and included relevant case studies.
Lokesh Payik said that despite the current challenging scenario, the future of manufacturing looks very bright and optimistic.
In 2012, Bosch began its Industrie 4.0 journey. The company did a survey among 160 operations leaders to gain a better understanding of their perspective on Industrie 4.0. The survey revealed that transparency in the production process, real-time updates about the plant, and converting manufacturing into a profit sector were some of the expectations. Also in 2012, thought leaders from Bosch and Siemens contributed to a white paper on Industrie 4.0.
Bosch has close to 270 plants worldwide, of which 250 plants have started implementing Industrie 4.0 use cases. The company works as a solution and integration partner for customers and its own plants. Mr. Payik presented several relevant end user case studies.
Located in the south of Germany, close to the border with Switzerland, this Bosch plant is considered a leader in applying Bosch production systems and best practices. The challenge here was to make the entire plant compliant with Industrie 4.0 concepts. After two and a half years of effort, all 5,000 systems in the plant are now connected in the production network. Logistics is streamlined with 100 percent traceability. With this solution, the company gained complete automation of flow of material using RFID to track both components and finished products. Any errors detected triggered notifications for the critical development operators, helping avoid output losses.
Recurring errors were linked to error patterns to enable the operators to derive suitable solutions. For previously unknown errors, the company’s video-enabled remote service support system could be used to help reduce crucial response times.
Facing issues with its warranty analytics, a large automotive OEM in India needed to be able to more accurately predict warranty claims whenever a product was released. Bosch provided warranty analytics to help this OEM reduce the previous 60 to 70 percent deviation down to just 4 to 5 percent, helping the company realize almost $6 million in savings.
Texmo Industries, a large agricultural pump manufacturer in India needed a detailed value stream mapping. The greatest challenge was to enhance the forecasting accuracy. The company also needed to improve its delivery commitments through flexible and agile manufacturing systems to help ensure that the right products were available at the right locations at any given point in time.
Bosch started off by implementing a smart manufacturing simulation. Man, machine, and materials were interconnected through HMIs, adapters, and RFID technologies. The solution automated and regulated the entire material flow in the factory. Seamless integration of information and messages helped connect the shop floor with the top floor. The solution helped integrate key manufacturing functions like production, maintenance, stores, and quality. Role-based manufacturing dashboards with relevant KPIs were deployed to increase efficiencies.
Mr. Payik also spoke about Bosch’s APAS family of manufacturing robots designed to work in tandem with humans. These robots utilize 180 sensors to help ensure human safety. A video demonstration showed how the robot’s sensor “skin” stops the robot when it detects a human being within a 5 cm radius. Also, once sensors indicate that the human is outside the danger zone (about a meter radius), the robot increases its operational speed.
Chandrashekar Bharathi, MD, from Ace Micromatic, India’s largest machine tool group, spoke about the company’s innovative contributions to manufacturing intelligence and machinery automation.
Mr. Bharathi elaborated on the role of IT in manufacturing, explaining how core manufacturing functions are surrounded by a layer of peripheral functions such as MRP, PLM, and PDM; which in turn are surrounded by functions such as ERP, SCM, and CRM. Industrie 4.0/IIoT-enabled manufacturing intelligence helps connect the shop floor to the top floor in real time.
In 2005, Ace Micromatic introduced the TPM-Trak manufacturing intelligence to provide real-time decision support to enable users to enhance asset performance in their discrete manufacturing operations.
The TPM-Trak Decision Engine processes and analyzes all the data, providing strategic analytics, tactical reports, or operational scoreboards as appropriate with the organizational hierarchy.
Challenged to help manufacturers automate machinery data capture to overcome human limitations, Ace Micromatic engaged with SMEs and other companies in brainstorming sessions to develop a solution with a “360-degree” perspective that addresses all concerns. These sessions revealed that:
Based on these takeaways, the company developed its MachineConnect solution, which eliminates the need for operators to collect, record, and communicate machine data. The solution provides a domain-specific hourly run chart without human input. Dr. Bharathi emphasized how the solution addresses critical pain points:
Mr. Bharathi concluded his session by mentioning that this is designed to be integrated with any automation system.
Nuclear Fuel Complex (NFC), one of the important units within India’s Department of Atomic Energy, is responsible for manufacturing fuel bundles for the country’s nuclear reactors (currently operating or planned). NFC’s presentation had two parts. R.S. Kulkarni first explained about NFC and what it does in its plants. Jeetendra Bhavrani then focused on the upgrade of one of the die making machines used in the manufacturing process.
The division manufactures fuel bundles – from ore to core. There are two manufacturing lines - one for fuel manufacturing and another for pellet manufacturing. Mr. Kulkarni discussed the brownfield project at Hyderabad which has various systems with varying complexities. He also discussed a greenfield project coming up at Kota, Rajasthan. This plant will have a rated capacity of 500 tons per year to cater to the fuel requirements of Kakrapar & RAPP 700 MWe atomic reactors.
Mr. Bhavrani explained the company’s development of electronic cam-based technology for manufacturing of rolling mill dies and contrasted this to conventional hardware template-based systems.
NFC manufactures around 200,000 quality-assured tubes per month. The process involves multiple steps, including melting, extruding, and rolling steps for seamless tubes. Making the dies is the most important step in the process as it progresses from lower depth to higher depth and this profile change is very smooth from 0 to 360 degrees.
In the conventional method, the die-making process involved a time-consuming three-step process using manually made metallic templates.
With the new electronic cam-based system, motion-controlled servos are used to make the dies, rather than physical templates.
According to Mr. Bhavrani, the new electronic cam-based technology provides a number of key advantages over conventional systems. These include electronic compensation of mechanical errors, higher accuracy, improved tube quality, shorter design-to-delivery times, and improved manufacturing safety and reliability.
All three presentations provided detailed insights into a variety of technology trends, applications, and benefits. These sessions reiterated that Industrie 4.0 and IIoT have definitely gone beyond the conceptual and hype stage into real-world use cases and are transforming manufacturing.
If you would like to buy this report or obtain information about how to become a client, please Contact Us.
Keywords: Ace Micromatic, Bosch, MachineConnect, TPM-Trak, Industrie 4.0, APAS, RFID, NFC, ARC Advisory Group.