
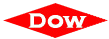




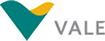

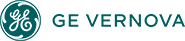




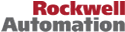

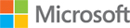
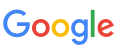

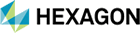


A company incurs capital expenditure (CapEx) – the capital utilized to buy fixed assets or to add to the value of existing fixed assets – to acquire or upgrade physical assets on plant and machinery, land and buildings, property, and such others. ARC Advisory Group captures CapEx in this report in two separate segments: based on the money spent on acquiring and upgrading total fixed assets, and on the money spent on acquiring and upgrading the plant and machinery.
ARC recently published its CapEx report (ARC’s Capital Expenditure Report Index for Industries) focused on industries for all world regions including North America, EMEA, Asia, and Latin America. However, ARC’s India capital expenditure report focuses exclusively on India’s capital expenditure analysis and includes the CapEx trends for leading industries in the country, such as automotive, cement, chemical & petrochemical, electric power, metals, oil & gas and refining, and pharmaceutical.
Economic expansion, especially in a domestic consumer demand-driven economy, such as India, boosts the country’s industrial growth. However, the demand and investment dynamics of each industry vary. For example, India’s electric power industry attracts large investments because the demand for electric power exceeds the country’s generating capacity. Industries such as metals and cement also spend more in terms of percentage of their total revenue due to the escalating demand from the growing investment in infrastructure projects. According to ARC Advisory Group’s India CapEx Survey 2015, capital spending as a percentage of revenue is relatively high in the electric power and metals industries in India. On average, while the electric power industry spends 27 percent of its revenue on CapEx, metals industry spends 39 percent of its revenue on CapEx.
However, India is still a highly price-sensitive market and continues to remain a country in which capital funding is expensive. End users of industrial technology, systems, and software often make the buy decision based on negotiated prices after a protracted evaluation process, which forces suppliers to be more competitive. Additionally, end users are more concerned about their ability to make cost-effective upfront investment and this often results in delay of project implementation. However, India is growing at a better pace than many developed economies and as consumer demand is more domestic driven, a growth rate near 7 percent makes India a preferred destination for global investments.
India’s GDP was approximately $2.1 trillion with a per capita GDP (PPP) of more than $6,664 in financial year (FY) 2015. India’s GDP value represents 3.3 percent of the global economy. In terms of purchasing power parity (PPP), India's GDP, at around $8.66 trillion, is the third largest in the world. In January 2015, the government changed the way GDP is reported. “GDP at factor cost” is now known as “Gross Value Added (GVA) at basic prices” for industry-wise estimates, whereas “GDP at market prices” is now known as “GDP.” According to the Finance Ministry of India, the annual growth rate of the economy is projected to have increased to 7.9 percent in FY 2015-2016 as compared with 7.4 percent in FY 2014-2015. India’s economy overtook China’s as the world’s fastest growing economy in the last quarter of 2014. The country’s GDP is mainly driven by the service sector, which constitutes over 54 percent, including IT and ITES contributing 8.1 percent to the overall GDP. Agriculture is the main occupation in India, accounting for over 16 percent of GDP and 50 percent of employment. The industrial sector (manufacturing, mining, and utilities) accounts for over 29 percent of GDP.
Looking at the purchasing manager’s index (PMI) for the manufacturing sector, it started strong at 54.5 in January 2015 but dipped to 52.7 by mid-year and experienced a further dip in December closing the year with 50.3, indicating a slowdown in the country’s manufacturing sector. Often, when bearish sentiments take control of the market, companies begin to liquidate inventories believing in the adage that “cash is king.” With most of the economic fundamentals remaining relatively strong, most analysts believe that India will continue to remain a destination of choice for manufacturing companies, including automation companies with appetite for growth.
Despite the current slowdown in manufacturing, the country has drawn a plan to boost the manufacturing sector in India. The country has re-emphasized its focus on manufacturing and set the target for 25 percent share of GDP from manufacturing by 2022 from the present 16-17 percent. The Indian government has introduced the Make in India program that includes major new initiatives designed to facilitate investment, foster innovation, protect intellectual property, and build best-in-class manufacturing infrastructure.
In terms of capital expenditure, while almost all industries contribute to the growth of India's automation market, automotive, cement & glass, electric power, metals, pharmaceutical, oil & gas, and refining represent the most significant share.
India ranks among the top 10 worldwide in terms of factory output and quantity produced by the industrial sector. Heavy process industries such as gas, mining, electricity, and quarrying also play major developmental roles and contribute significantly to the GDP; hence, ARC expects demand for automation technology to rise significantly over the next few years. Also, as companies in India currently underutilize information technology, which could significantly improve production and supply chain management efficiencies, ARC expects to see rising demand in these areas as well.
ARC Advisory Group’s India Capital Expenditure Survey 2015 tracks total capital expenditure, capital expenditure on plant and machinery, total revenue, total assets, and return on assets. The sample size includes 97 companies from eight major industries representing over $491 billion revenues in 2015. This capital expenditure survey is based on the analysis of the information from the annual report of India’s leading companies in the following important and growing industries: automotive, cement, chemical & petrochemical, electric power, metals, oil & gas, refining, pharmaceutical, and food & beverage.
India imports around 80 percent of its annual oil & gas requirements from the Middle East, North Africa, and other regions. The reduced oil prices not only lower the import bill but also help save foreign exchange. As per rough estimates, a $10 fall in crude can reduce the current account deficit by approximately 0.5 percent of GDP and the fiscal deficit by around 0.1 percent of GDP.
Brent crude oil price hovered around $48 per barrel in the second quarter of 2016 and is expected to stay close to the $50 per barrel mark in 2016. Privately held Indian upstream oil & gas companies have suffered significant losses in 2015 since the oil price realized by them is directly linked to the global oil prices, as opposed to publicly held upstream oil & gas companies that have done reasonably better, as the subsidy they provide to state-run refineries has reduced with the decline in oil prices. The downturn in oil prices has had significant impact in 2015 shipments, and some mild effects may be felt in 2016 as well. How quickly the oil prices can recover will be a major factor deciding the rate of recovery of the upstream oil & gas industry.
In the past several years, it became evident that energy prices will have a large impact on manufacturing in all industries. The energy required to generate heat, cooling, steam, compressed air, electricity, and such others is becoming an increasingly important cost factor that must be measured, monitored, and controlled, just as any other cost component. Instability in energy prices is a source of concern for both manufacturers and automation suppliers since it impacts production cost directly.
Inflation rate in India averaged 8.51 percent from 2012 to 2015, reaching an all-time high of 11.16 percent in November 2013 and a record low of 3.78 percent in August 2015. Consumer price changes in India can be very volatile due to dependence on energy imports, the uncertain impact of monsoon rains on its large farm sector, difficulties transporting food items to market because of its poor roads and infrastructure, and high fiscal deficit. Particularly the food inflation, which has remained above 8 percent for many months, is highly detrimental as a majority of the people spend almost 55 percent of their income on food bills. Many analysts ascribe high inflation on one hand to the food price issue and on the other to the demand pressure, which has remained consistently high due to supply-side constraints. The country’s central bank (Reserve Bank of India), concerned with the stubborn high inflation, controls the bank rate. The bank has announced several rate cuts in the past year; however, high inflation and high fiscal deficit both get in the way of implementing the rate cuts.
The declining trend of exchange rate value of rupee is affecting the country’s economy, making imports expensive. In such a situation, when the higher cost is passed on to the consumer, inflation increases. While the rupee’s value against the dollar touched low of 62.11 in January 2015, it was at 66.52 in December 2015. The state is taking several fiscal initiatives to make the currency stronger and ease inflation, and these are likely to have their impact on the CapEx trend by industries.
India’s National Manufacturing Policy (NMP) aims to uplift the manufacturing sector and has set a target of 25 percent share of GDP from manufacturing by 2025. The policy also aims to enhance the manufacturing sector’s global competitiveness. Some of the state initiatives in the NMP include setting up a national manufacturing and investment zone (NMIZ) to promote investments in the manufacturing sector, promoting green technologies, promoting skill development programs to cater to the needs of the manufacturing sector, and such others. The policy will enable the country to emerge as a global manufacturing hub with extended forward and backward integration with the global supply chain.
While the state can only create the necessary policy ambience, the key players who can exploit the growth opportunities are the industry thought leaders. Meeting the consumer demand, which continues to remain relatively good compared with many other countries, rests with the industrial companies and the strategies they adopt to fulfill the demand while protecting their margins. While there is further scope to refine it, the state has played its part by announcing the NMP.
India’s sustained economic growth continues to propel demand for energy and basic materials. This will lead to increased production of electricity, oil and gas, metals, and chemicals, driving the use of automation technologies.
Capital investments are likely to increase in the metals & mining sector due to rising commodity prices. Other industries where increased capital investments are expected include oil & gas and chemical & petrochemical industries. In the short term, the market may face reduced growth opportunities with “clean energy” and alternative energy applications due to lower government incentives. This may reduce private investments.
The most robust industries in India are automotive, cement, power, metals, pharmaceutical, and oil & gas. India’s economy remains strong, but there are signs of a slowdown due to the euro debt crisis, high domestic inflation, rupee depreciation, low oil prices, and fiscal deficit.
India’s automotive industry was worth over $95 billion in 2012 and is expected to grow to nearly $300 billion by 2026. The automotive industry accounts for 7 percent of the country's GDP and 22 percent of the country's manufacturing GDP. Over the last five years, India’s automotive industry has expanded at an impressive 19 percent compound annual growth rate (CAGR). Automobile exports grew at a CAGR of 14.65 percent during 2010-2015. Cars account for almost two-thirds of the overall automotive market. Approximately 31 percent of all small cars sold globally were manufactured in India in 2014-2015.
The rising middle-class segment and strong domestic demand are the key drivers of the automotive industry in India. A wide range of products is now available for customers across various strata of society. In addition, reduced product lifecycle has forced manufacturers to expedite new launches. Even though there is a slowdown in the growth of India’s automotive industry, the increased competition in the industry led to the adoption of more plant software. According to industry trackers, India’s robust domestic sales have made it the third largest automotive market in 2016 and account for 5 percent of global sales. Additionally, India is emerging as the center of excellence for compact cars. The industry has attracted FDI worth $14.32 billion during the period April 2000 to December 2015.
Auto makers in India produce the entire range of passenger vehicles: multi-utility vehicles (MUVs), sports utility vehicles (SUVs), commercial vehicles, trucks, buses, tractors including farm, earthmoving, and construction equipment, and two- and three-wheelers. Almost all automotive segments (small cars, SUVs, luxury vehicles, and such others) have been experiencing growth. The country is becoming a global hub for automotive manufacturing, with increasing presence of the world’s top auto majors. The global automotive OEMs and Tier 1 companies are making India a supply chain center.
Over the last five years, India’s automotive industry has expanded at an impressive 19 percent CAGR. Cars account for almost two-thirds of the overall automotive market.
According to the ARC India CapEx index, capital spending in the automotive industry is around 6 percent of revenue. Out of the total CapEx, the automotive industry in India spends around 31 percent on plant and machinery.
The cement industry in India is expected to increase its total installed capacity to about 550 million tons per annum (mtpa) by FY 2020 from the current capacity of more than 390 mtpa, and retain its position as the second largest cement producer in the world. With over 209 large cement plants and 365 mini cement plants, India’s cement industry has tremendous potential for future growth due to the robust growth in housing, infrastructure & construction, and such other sectors. The escalating demand for housing and office complexes, hotels, hospitals, roads & highways, multiplexes, industrial construction, and such others spurs the growth of the cement industry in India. In 2016, the cement demand growth rate is expected to be 9.8 percent, which exceeds the supply growth rate of 6.7 percent; this will drive investments in this sector and improve realizations. Industry experts are of the opinion that the industry would experience double-digit growth in the years to come, as the government has planned to invest $1 trillion in infrastructure during the 12th five-year plan (2012-2017) and boost infrastructure and economic growth by developing 100 smart cities.
The industry’s dominant players include large domestic companies, such as UltraTech, Gujarat Ambuja, JK, ACC, Century, and Madras Cement. Global cement majors with a large domestic presence include LafargeHolcim, Italcementi, and Heidelberg. Global companies entered the Indian market in the last decade lured by the opportunities in this industry. Some also plan to add production capacities through new projects or brownfield project expansions.
According to the ARC India CapEx index, the cement industry is the second largest in India in terms of capital spending as a percentage of total revenue. The capital spending in the cement industry is around 20 percent of revenue, and out of this total CapEx, the industry spends over 49 percent on plant and machinery. As the cement industry’s investment grows steadily, the growth in CapEx as a percentage of revenue will follow the revenue growth.
India’s chemical and petrochemical industry accounts for 3 percent of the global chemical industry. It is the third largest producer in Asia and 12th largest in the world in terms of volume. The industry, having a large domestic demand potential and a diversified manufacturing base to produce quality chemicals, is likely to grow at 14 percent per annum, and is expected to exceed $350 billion by 2021. The chemical sector accounts for 13-14 percent of total exports and 8-9 percent of total imports in India.
Alkali chemicals form the largest segment of India’s chemical industry, with 71 percent of the total production share. Total chemicals export stood at $19.2 billion in FY 2014.
The government has approved 100 percent FDI in the chemicals sector, and policies are in place to set up integrated Petroleum, Chemicals, and Petrochemicals Investment Regions (PCPIR). PCPIR is a dedicated investment region for manufacturing domestic and export-related products of petroleum, chemicals, and petrochemicals.
The expanding markets for automobiles, consumer durables, textiles, and such others stimulate the demand for petrochemicals. Fine chemicals, dyes and intermediates, and knowledge-based chemicals also play a significant role in driving the growth of India’s chemical industry. India being a net importer of crude oil poses a challenge for the growth of the petrochemical industry in the country.
Petrochemicals (olefins and aromatics) are a major component of the domestic chemical industry, accounting for over 60 percent share by revenue. Demand for olefins and aromatics is expected to grow at about 10 percent and at 12 percent per annum, respectively, over the next four to five years.
According to the ARC India CapEx index, capital spending in the chemical & petrochemical industry is around 15 percent of revenue. Out of the total CapEx, the chemical and petrochemical industry in India spends around 56 percent on plant and machinery.
The country’s electric power industry, with a total installed capacity of about 303 GW as of June 30, 2016, is globally the fifth largest in terms of generating capacity and third in terms of transmission and distribution network coverage. Out of the total installed capacity, 211 GW is produced via thermal energy, 42 GW via hydroelectric power plants, close to 5.7 GW from nuclear energy, and the remainder 42 GW via other renewable energy sources. India became a power surplus country by the end of 2015, with a huge power generation capacity idle for want of demand. However, project delays, inability of the electric power industry to bill and recover payments, and such other factors hinder the power industry’s growth. Additionally, non-availability of coal, setback in the construction of nuclear power plants due to the recent Fukushima catastrophe, and other challenges thwart its growth potential.
The electric power industry has to overcome the constraints and expand at least at the rate at which the economy expands so as to not hamper the country’s economic growth ambitions. The country’s economic growth is entering a phase where its dependence on expansion of infrastructure and manufacturing would increase, making the country’s economy more energy intensive. In order to meet the demand for electric power, the industry must expand to cover not only generation, but also creation of transmission and distribution assets.
The Ministry of Power, a nodal agency responsible for the country’s electric power industry, is targeting to add more than 76,000 MW during 2012-2017, taking into account fuel constraints and the expected needs of an expanding economy for electric power. In addition, it has planned to add more than 93,000 MW to the generating capacity during 2017-2022. Several number of steps and initiatives have been adopted, like the 10-year tax exemption for solar energy projects, in order to achieve India's ambitious renewable energy targets of adding 175 GW of renewable energy, including addition of 100 GW of solar power, by 2022. India’s electric power industry needs to explore the benefits of investing in distributed generation, smart grid, and such other verticals. Renewable industry presently constitutes around 13 percent of the total installed base and is on an accelerated growth path in both solar power and wind power generating plants. Presently, India's clean energy capacity is 33,000 MW. India’s Economic Survey stated that the clean energy sector was likely to generate $160 billion in the next five years. This in turn is leading to the development of distributed generation topology and associated technologies.
According to the ARC India CapEx index, capital spending in the power industry is 41 percent of revenue. Out of this total CapEx, the industry spends over 51 percent on plant and machinery.
India’s rising infrastructure and automobile market, along with power and cement, is the key driver of the metals & mining industry. In 2011, the industry size was nearly $142 billion, which has reached $305 billion in 2015 and is expected to grow at a 5.2 percent CAGR in the next five years. The government of India has allowed 100 percent FDI in the mining sector under the automatic route. India produces 88 minerals, and at present India is the largest producer of mica, fourth largest producer of crude steel, and fifth largest producer of bauxite and zinc, globally. Minerals like manganese, lead, copper, and aluminum are expected to witness double-digit growth in the years to come.
Capacity for crude steel production has expanded from 56.8 mtpa in 2007 to over 101 mtpa in 2013-2014. The total market value of India’s steel sector was $77 billion in 2015-2016. India was a net importer of steel till FY 2013, but turned a net exporter of the same in FY 2014. India imported 9.32 MT of steel while export declined to 5.59 MT in FY 2015 from 5.98 MT during 2013-2014. This indicates the high growth potential that exists for the metals and mining industry in India. NMDC, along with Sesa Goa, SAIL, and Orissa Minerals, is the major player in the iron and steel industry in India. Coal India Limited, holding over 80 percent of India’s total coal market, is the leader in the coal segment. HINDALCO, NALCO, and BALCO are the major players in the aluminum sector in India. Based on the current investment plans of leading companies, India’s production capacity will double in the coming years.
The growing CapEx trend of these leading companies creates huge opportunities for automation suppliers in India. According to the ARC India CapEx index, capital spending in the metals industry is 25 percent of revenue. Out of this total CapEx, the industry spends over 56 percent on plant and machinery.
The oil & gas industry plays an important role in India’s economy, and the country depends on imports to the extent of almost 80 percent. The recent slump in global oil prices has benefited the refining sector and helped the country in reducing its trade deficit. India has emerged as a refining and petrochemical hub, and export of refined petroleum products accounts for high forex earnings. India has the potential to become self-reliant in the oil & gas industry, as over 55 percent of the 3.14 million sq km of the country’s sedimentary basins are either poorly explored or unexplored. India’s government is targeting an investment of $100 billion in the oil & gas sector in the next five years to contribute to its Make in India plan. As part of this initiative, the government has allowed 100 percent FDI in many segments of the sector, including natural gas, petroleum products, and refineries, among others.
India’s oil & gas sector is estimated to be worth $139 billion in 2016. India’s total crude oil production was 761,000 barrels per day (BPD) in 2014-2015 and is expected to cross 1 million BPD by the end of 2016. Total gas production rose to 90 billion cubic meters (BCM) in 2014-2015 from 35 BCM in 2013-2014. Gas pipeline infrastructure in the country stood at 15,808 km in December 2015. Currently, the country has 23 refineries whose production capacity exceeds 230 million metric tons per annum (mmtpa) and the refining capacity is likely to rise by another 90 mmtpa by the end of FY 2016-2017, with capacity augmentation of existing refineries. The refining industry has significant overcapacity, created deliberately to meet the global demand for refinery products. Currently, petroleum product exports contribute to almost 20 percent of India’s export earnings. India has some state-of-the-art refineries that enjoy relatively better refining margins as compared with its global peers, and more refineries are in the pipeline. Due to the upgradation in vehicle emission standards from Bharat Stage IV to Bharat Stage VI, many refineries will be required to invest in producing cleaner fuel to meet regulatory norms.
According to the ARC India CapEx index, capital spending in the oil & gas and refining industry is 16 percent of its revenue. The oil & gas and refining industry in India spends 36 percent of the total CapEx on plant and machinery.
The performance of India’s pharmaceutical industry has been impressive, and the market size may exceed $55 billion by 2020 from the 2009 levels of close to $12.6 billion at a CAGR of 14.5 percent. The industry has grown by targeting opportunities in the generic market and leveraging its strengths in drug formulation technology. The country has 523 manufacturing facilities that comply with US FDA (Food and Drug Administration) requirements, the highest for any country outside the US, and 80 that meet UK MHRA (Medicines and Healthcare products Regulatory Agency) manufacturing requirements. The overall drug approvals given by the USFDA to Indian companies have nearly doubled to 201 in FY 2015-2016 from 109 in FY 2014-2015. India’s pharmaceutical industry has emerged as a producer of quality drugs complying with global standards. It has learned the nuances of the generic drug market dynamics – identifying medicines that are going off-patent, filing the necessary abbreviated new drug applications (ANDA) and drug master files at the appropriate time, securing the appropriate FDA approvals, and such others, including willingness to overcome legal tangles. The industry has largely grown organically, but it has also ventured into global acquisitions and mergers. India’s government has unveiled "Pharma Vision 2020" aimed at making India a global leader in end-to-end drug manufacture. The government has also put in place mechanisms such as the Drug Price Control Order and the National Pharmaceutical Pricing Authority to address the issues of affordability and availability of medicines.
India’s biotechnology sector is among the top 12 globally. It has been growing at an impressive year-on-year growth rate of above 30 percent and is expected to reach approximately $100 billion in 2025. It consists of biopharmaceuticals, bio-services, bio-agriculture, bio-industry, and bioinformatics. Biopharmaceuticals (comprising diagnostics, vaccines, and therapeutics) alone contribute approximately 62 percent of the total revenues.
In recent years, global pharmaceutical companies are increasingly investing in India’s pharmaceutical companies to meet global demand and to reduce labor costs. The pharmaceutical industry invests not only in plant and equipment to produce drug and formulations, but also in enabling technologies to ensure regulatory compliances, maintain consistent quality products, and reduce costs. With the health costs going up globally, there is increasing awareness about the benefits of generic drugs. The industry, with deep domain knowledge, proven track record in the production of generics, and the largest number of production facilities that meet FDA requirements outside the US, is well positioned to exploit the growth opportunities and expand in double digits. India’s pharmaceutical exports account for 10 percent of the global markets by volume.
According to the ARC India CapEx index, the pharmaceutical industry’s capital expenditure is around 6 percent of revenue. The industry spends around 81 percent of the CapEx on plant and machinery.
India’s food processing industry was about $250 billion in FY 2015-2016 and is expected to grow at a CAGR of 10-13 percent, according to industry experts. It is one of the largest industries in India and is ranked fifth in terms of production, consumption, and exports. India’s food processing industry accounts for 32 percent of the country’s total food market; 14 percent of manufacturing GDP; 13 percent of exports; and 6 percent of total industrial investment. The food processing sector is expected to attract $33 billion investment over the next 10 years. According to industry experts, the ready-to-drink tea and coffee market in India may touch $404.78 million in the next few years. Several favorable factors, such as the increasing trend in the consumption of processed food products and fiscal incentives being planned by the government, are capable of maintaining the growth momentum in the future. Anticipating the future growth, many global players are entering the India market by collaborating with the domestic players. This trend has emerged more strongly in 2015, providing opportunities to local players to widen their product portfolios.
According to the ARC India CapEx index, the food & beverage industry’s capital expenditure is around 2 percent of revenue. The industry spends around 71 percent of the CapEx on plant and machinery.
The ARC India CapEx survey reveals the downward trend of overall capital expenditures, but even more so for plant and machinery for improving operations. ARC believes that companies must focus on building strategic competencies that will make them best in class and invest in enabling automation and enterprise technologies to achieve productivity-led growth. Such investments would help companies manage their costs and protect their margins, a viable strategy to tide them over uncertain times.
India’s economic fundamentals, especially on the demand side, are still strong compared with the global economy. During times of global economic crisis and in a flat world, manufactured goods can freely move from countries with excess production capacity to countries like India that face supply-side constraints.
ARC believes that industrial companies typically invest in automation systems based on health, safety, and environmental considerations. During the project engineering or conceptualization stages, in particular, companies do not place adequate focus on achieving operational excellence. However, in the long term it is important for companies to focus on operational excellence. Here, automation systems can play an important role in empowering companies to achieve continuous improvements.
If you would like to buy this report or obtain information about how to become a client, please Contact Us