
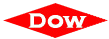




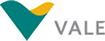

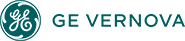




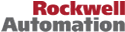

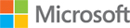
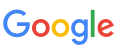

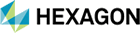


Currently, tens of thousands of control systems that are well past their expected lifespans are still installed and operating in industrial plants around the world. Often, however, plant personnel must make extraordinary efforts to keep the aging technology functioning without significant system downtime or production outages. This includes scavenging replacement parts from other systems or obtaining them from sometimes-questionable internet sources, but it must be understood that DCS Migrations Justified by Business Case
Ironically, because of these efforts, management frequently does not understand why the systems must be replaced. Since the systems are still “doing the job” (more or less), management will ask, “What’s the justification for replacing them?”
During the recent ARC Industry Forum in Orlando, Florida, three owner-operator companies presented their recent control system migration projects. While each selected a different DCS supplier and used a different approach, we learned that all three suppliers provided very good technology and services to make the implementation and startups go smoothly.
The size and scope of the respective projects differed, as did the ultimate migration paths taken. But what all three projects had in common was that the risk of doing nothing was increasing rapidly. Each project team was able to provide its management with a convincing argument to replace and upgrade the existing distributed control system (DCS) technology. The key was to justify the request for capital expenditures in financial terms, using a risk/reward approach.
Unfortunately, management often views control systems and other automation technology as a basic utility. To convince management of the business benefit that could be obtained by upgrading current obsolete and/or unsupportable control systems to a modern platform, the project team must avoid using technical arguments. Instead, it’s best to present the argument in financial terms; focusing on both cost and potential financial benefits to the enterprise.
The team must first perform a rigorous cost and value analysis to create a compelling business case for DCS migration relative to other capital investment projects that might be competing for funding. Lifecycle cost modeling, a well-proven technique, can often provide a definitive economic justification using terms that the CFO will understand and appreciate.
At a session on justifying DCS migration projects at the recent ARC Forum in Orlando, ARC Associate Mike Williams reminded the audience about prior work by Dr. Peter Martin, vice president at Schneider Electric (and ISA Fellow). Dr. Martin, in collaboration with ISA, has published two books on lifecycle cost modeling for process automation in which he defines a lifecycle cost model representing not only the initial cost of procuring, configuring, and installing an automation system; but also the ongoing maintenance and upgrade costs incurred to ensure system reliability throughout its expected life. These books provide detailed descriptions and examples of the lifecycle cost components.
Unfortunately, while the “cost” side of the model (expressed as a complex equation) has always been relatively easy to define, until recently it had not been easy to quantify the “benefits” side of equation.
Session attendees were informed of on-going research by Professor Peter Sandborn from the University of Maryland’s Center for Advanced Life Cycle Engineering (CALCE). CALCE, a globally recognized expertise center, focuses on the reliability of electronic systems. Many commercial vendors and nation states contract with CALCE to perform failure analysis for both newly developed and legacy systems to determine lifecycle support strategies. Under Dr. Sandborn’s direction, CALCE has extended its reliability-centric research to the process automation domain.
Using proven stochastic modeling techniques, CALCE has amended value creation algorithms to the established economic model to derive the optimal balance between system benefits and their associated costs. This rigorous approach enables end users to evaluate their existing system integrity and reliability and determine the optimal degree and timing for a process automation investment relative to business expectations and functional capability.
At this Forum session, we learned about the three different approaches the presenters used to justify their DCS migration projects.
Emilio Paramo, Head of Systems and Telecommunications for DAK Americas, a leading global manufacturer of polyethylene-based resins, presented the process that his plant went through to justify an upgrade to the NovaTech D/3 process control system originally installed in 1995. The system had run for 20 years with “not a single failure on the production side due to the DCS,” according to Mr. Paramo. He went on to explain that when it comes to justifying investment in a system upgrade, historically high reliability can make the case for change more difficult.
Mr. Paramo and several of his predecessors discovered the hard way that vendor-provided component lifecycle analysis alone was not sufficient to convince management to reinvest in process automation. Using life expectance calculations for individual components, information about vendor supply of spare parts, and risk analysis techniques; the project team constructed a comprehensive risk analysis model based on varying degrees of system failure and the resulting consequences (including the business consequences associated with doing nothing). The team calculated that the worst-case scenario would be a business outage of 11 working days. Based on the time to repair after a catastrophic system failure, management was presented the following economic risk assessment for this scenario:
Cost of Doing Nothing versus the Cost of Upgrading
Though the effect of a catastrophic failure was considered material to the business, on the surface, this appeared manageable. The impact of a failure, however, could have broader impact if this outage resulted in a force majeure supply chain event. This event could have far-reaching impact on customer relations, with potentially permanent loss of business. Projected over the lifetime of an asset (10-year NPV), this provided a compelling case for change. But the story doesn’t end there. The team still had to do a significant amount of “internal selling” to convince both local plant management and corporate executives about the urgent need to invest in a new DCS. This required using arguments based both on the technological obsolescence and functional viability of the current system and the potential impact of system component failures on future revenue streams.
Once the project was approved, the team worked with their existing vendor, NovaTech, to prepare for the system upgrade. The project took 21 months from project approval to commissioning. The conversion involved 33 racks of control equipment managing 2,700 I/O. According to Mr. Paramo, one of the keys to project success was exhaustive preparation prior to the cutover. This included having the supplier preassemble and test all modules in the factory before they arrived on site. Thanks to extensive factory acceptance testing and end user training, the actual switchover took only seven days. By staying within the existing product architecture, the plant minimized business interruption during cutover. The upgraded system also requires much less day-to-day human intervention, has a native language graphical user interface, and offers 25 percent future expansion capability for I/O.
Based on DAK learnings from this migration project, to successfully justify a control system migration, Mr. Paramo urged the attendees to “involve everyone” from the beginning. This includes finance, logistics, operations, and maintenance. By extending stakeholder involvement, every point of view can be considered to help break down cross-functional barriers and gain widespread support for the business case. He also emphasized that it is important to consider all elements of the computer system design to understand the full value potential of a control system migration and thus improve your business case for change.
For Dow Corning, a global leader in silicon-based technology and innovation, every control system migration project represents a potential opportunity to create value. Sharla DeFrain, a Dow Corning Project Manager, explained that the automation function at Dow Corning utilizes a four-step process to evaluate and improve the level of automation for all process control system migration projects. The process automation team employs a rigorous lifecycle cost/value analysis to prioritize and authorize individual projects within a corporate-wide migration program. To provide input to the lifecycle cost model, the company has developed a composite Automation Health Assessment Index (AHI) that clearly shows management the current integrity of legacy systems. The AHI score enables a normalized comparison of one system migration opportunity to another, thus prioritizing migration projects based on their respective potential to help close specific opportunity gaps.
In addition to the AHI tool for assessing equipment health, Dow Corning has developed an Automation Value Index (AVI) tool to be able to rigorously assess the value that could be gained through an automation system migration. The AVI helps determine the functional “uplift” that a migrated system could deliver if implemented. This enables the company to quantify the benefits as operational savings or revenue generation for the new system.
For both tools, the scores are determined by a trained assessment team using both internal and external industry best practices as guidelines.
In combination with the Lifecycle Economic Model, the two indexes provide the individual businesses and the overall corporation with a rigorous method for reviewing investment options to use to be able to make informed decisions.
Ms. DeFrain presented results from several completed projects that verified how the methodology, tools, and implementation techniques have created value through legacy system migration.
In one example, by deploying a new Siemens PCS7 during a polymer plant control system upgrade, a $300 thousand investment in automation produced $4.6 million return. The company determined that the higher levels of automation provided by the new Siemens system improved overall equipment effectiveness (OEE), which in turn helped increase product sales to improve business growth.
As additional projects are implemented, rationalizing multiple vendor plants and reusing common application schema further enhances the program’s value contribution to the corporation by reducing both the initial and long-term cost of ownership.
Trinseo, a new plastics and chemicals company, was created when Dow Chemical divested a significant number of its legacy production assets. With facilities in 27 countries, Trinseo has 19 production sites, 67 manufacturing units, and 32 plants; but only 2,100 employees. A large part of the company’s automation assets and associated intellectual are based on Dow’s proprietary and soon-to-be-unsupported MOD 5 control system. Under the terms of the divesture, Dow will provide support for the legacy systems through 2020. This will forces Trinseo to migrate to a new automation platform at a number of its plants located around the world in the coming years.
David Garrett, senior process automation leader for Trinseo, explained that due to the significant capital investment this would require, the new corporation set a high expectation for this program.
To achieve its challenging economic objectives Trinseo selected ABB as its OEM and systems integrator to replace all legacy systems. One significant obstacle to developing an economic justification for migrating to a new system is that the legacy MOD 5 system already delivers a high level of automation, making it mandatory to preserve the existing functional capability. However, simply replacing the existing functionality would deliver zero incremental value to the new owners. More value creation was necessary to proceed.
In addition to the large impact the expansive system migration project would have on the company’s capital expenditures and cash flow, the company would have to migrate at least seven plants per year to the new platform to complete the migrations by 2020. To avoid potentially crippling business interruption, the company and ABB, its automation partner, needed a well-structured and standardized approach to reduce the cost of conversion, retain existing process capability, and take advantage of yet-to-be-defined uplift opportunities.
The automation team first created “architectural principles” to provide guidance for all the plant migrations within the overall program. These principles required improvements to existing implementation practices, engineering tools, and functional capability. One example that Mr. Garrett cited was embracing ISA standards such as ISA 88 and ISA 106 to create reusable, modular control strategies rather than having to create new solutions on every project.
Other changes included improvements to the engineering configuration tools and associated work processes. These included deploying a “cloud-based” central configuration database to support multiple versioning and global distribution of control applications.
The goal for the transformed implementation practices and leveraged solutions was to drive the long-term cost of ownership to one-third of the historical costs. According to Mr. Garrett, after completing four of 32 planned migrations, it appears that the company is well on its way to achieving the business objectives for this corporate-wide program.
For any migration project – large or small – it is important to speak the language that the approvers understand. It is not enough to just reduce the number of failures of obsolete hardware components no longer available from the original supplier. The justification must provide both cost and expected benefits (value) relative to the next best investment option.
Given that the investment for a control system migration will compete for limited funds that could be invested any number of other ways by the corporation, it is also important to be as rigorous and credible as possible when creating a business case. In some cases, it may make sense for companies to engage with a third-party consultant or other organization to help build consistency and credibility into their economic analysis.
Before investing time and effort in economic analysis, it is important to identify and get the key stakeholders and influencers involved. ARC recommends a multi-functional team approach to migration projects. This will ensure that key stakeholder views and needs are heard and considered in the ultimate solution.
ARC recommends the following actions for owner-operators, systems integrators, and main automation contractors involved in legacy control system migration projects:
In the end, management will compare the proposed system migration investment to other potential company capital investments. These alternative investment opportunities may or may not involve technology, but all will be judged on their respective financial returns.
If you would like to buy this report or obtain information about how to become a client, please Contact Us
Keywords: DCS, Migration, Work Processes, CapEx, ARC Advisory Group.