
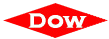




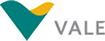

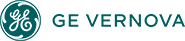




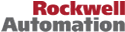

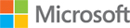
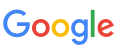

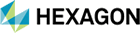


A company incurs capital expenditure (CapEx) – the capital utilized to buy fixed assets or to add to the value of existing fixed assets – to acquire or upgrade physical assets on plant and machinery, land and buildings, property, and such others. In this periodic report, ARC Advisory Group looks at the CapEx for India’s Manufacturing Industries to identify trends.
We calculate CapEx in two separate segments: based on the money spent on acquiring and upgrading total fixed assets, and on the money spent on acquiring and upgrading the plant and machinery.
ARC also publishes a global CapEx report (ARC’s Capital Expenditure Report) focused on industries for all world regions including North America, EMEA, Asia, and Latin America. However, ARC’s India capital expenditure report focuses exclusively on India’s capital expenditure analysis and includes the CapEx trends for leading industries in the country, such as automotive, cement, chemical & petrochemical, electric power, metals, oil & gas and refining, food & beverage, and pharmaceutical.
Industrial companies are seizing the present growth opportunity that India offers. Companies are building best-in-class industrial facilities to meet the growing needs of the country’s expanding consumer class. Major investments have been planned for infrastructure development that would in turn push the domestic steel companies to increase production and plant capacity. The plan for expansion and upgrades of refineries to meet the BS norms for vehicle fuels is also underway. There are some sectors like power generation and cement that are burdened with overcapacity and underutilization of assets. However, in the long run the rise in domestic demand will increase the value creation through these assets. On the infrastructure front, government has allocated huge investments for building roads, railways, airports, and ports; and companies are likely to rev up their capacity expansion activities to meet domestic demand in the coming years. According to ARC Advisory Group’s India CapEx Survey 2016, capital spending as a percentage of revenue is relatively high in the cement, chemical, electric power and metals industries in India. On average, while the electric power industry spends 28 percent of its revenue on CapEx, metals industry spends 14 percent of its revenue on CapEx. Cement and chemical sectors spend more than 10 percent of their revenues on CapEx.
The overall CapEx in India has been declining since 2011 and a break in this trend was observed during 2013- 2014. The structural reforms in the form of demonetization and GST implementation in late 2016 and mid of 2017, respectively, have led to a temporary and short-term dip in industrial activities. India has nearly overcome this disruption, and is expected to sustain the growth momentum going forward. Moreover, gains from GST and other structural reforms, combined with low oil prices will contribute towards the country’s growth.
India’s GDP was approximately $2.26 trillion with a per capita GDP of more than $6,658 in financial year (FY) 2016, and the economy grew at 7.1 percent in 2016-17. In terms of purchasing power parity, India’s GDP, at around $8.7 trillion, was the third largest in the world in FY 2016. According to the Finance Ministry of India, the annual growth rate of the economy decreased to 6.8 percent in FY 2016-2017 as compared with 7.6 percent in FY 2015-2016. However, India’s economic growth is expected to pick up speed from 6.8 percent in 2016 to 7.2 percent in 2017 after a modest setback due to weaker-than-expected investments and effects of withdrawal of large denomination bank notes. The country’s GDP is mainly driven by the service sector, which constitutes over 53 percent, including IT and ITES contributing 8.1 percent to the overall GDP. Agriculture is the main occupation in India, accounting for over 17 percent of GDP. The industrial sector (manufacturing, mining, and utilities) accounts for over 29 percent of GDP. According to the Department of Industrial Policy & Promotion, India received foreign direct investment (FDI) inflows worth $46.4 billion during the FY 2016-2017, with services sector attracting the highest investment of $7.5 billion.
The purchasing manager’s index (PMI) for the manufacturing sector, started at an expansion mode in January and rose in March on account of higher business activities. However, due to lack of new orders and shortage of raw materials, the PMI again dipped in April, and gradually increased in August indicating growth in the country’s manufacturing sector as a result of rise in domestic demand as well as exports.
India undertook demonetization of high value currency notes in November 2016, because of which there was a sharp dip in the manufacturing and construction sectors as can be seen in the contraction of PMI in December. The effect on some industries was more pronounced than the others due to lack of liquid cash. Cash-based sectors, including the unorganized sector, and small and medium scale industries (SMEs), which account for nearly half of the manufacturing GDP, was hard hit. Labour intensive construction industry, cement industry, and medium and small sized secondary steel sectors also witnessed slow growth. Moreover, investment in plant and machinery, as measured by gross fixed capital formation (GCFC), was down to 25.5 percent in FY Q4 from 27 percent in FY Q3 2016, as per Central Statistics Office (CSO). However, the effects of demonetization was temporary and started to wane by the end of Jan-March quarter 2017. The Indian government’s Make in India program has helped to attract significant FDI flow, and the country’s position in the World Bank’s ease of doing business ranking has gone up from 134 in 2015 to 130 in 2016, and projected to rank 100 in 2018.
ARC Advisory Group’s India Capital Expenditure Survey 2016 tracks total capital expenditure, capital expenditure on plant and machinery, total revenue, total assets, and asset turnover. The sample size includes 94 companies from eight major industries representing over $491 billion revenues in 2016. This capital expenditure survey is based on the analysis of the information from the annual report of India’s leading companies in the following important and growing industries: automotive, cement, chemical & petrochemical, electric power, metals, oil & gas and refining, pharmaceutical, and food & beverage.
Private consumption remains one of the key drivers for India’s economy. The growing consumer class and their rising purchasing power has opened a huge market in India for both domestic and global companies. The demand for good quality electricity, fuel, urban infrastructure, transportation, consumer products and so forth, are propelling the country as one of the fastest growing markets in the developing economies. The domestic consumption has remained more or less steady over the last 3-4 years and there is ample room for per capita consumption to increase.
India imports around 80 percent of its annual oil & gas requirements from the Middle East, North Africa, and other regions. The reduced oil prices not only lower the import bill but also help save foreign exchange and lower the current account deficit (CAD). As per rough estimates, a $10 fall in crude can reduce the CAD by approximately 0.5 percent of GDP and the fiscal deficit by around 0.1 percent of GDP.
Brent crude oil price hovered around $48 per barrel in the second quarter of 2016 and is expected to stay close to the $50 per barrel mark in 2016. The downturn in oil prices has had significant impact in 2015 shipments, and some mild effects may be felt in 2016 as well. How quickly the oil prices can recover will be a major factor deciding the rate of recovery of the upstream oil & gas industry.
In the past several years, it became evident that energy prices will have a large impact on manufacturing in all industries. The energy required to generate heat, cooling, steam, compressed air, electricity, and such others is becoming an increasingly important cost factor that must be measured, monitored, and controlled, just as any other cost component. Instability in energy prices is a source of concern for both manufacturers and automation suppliers since it impacts production cost directly.
According to IMF, CPI inflation declined from an average of 9.8 percent during 2011–13 to an average of 4.9 percent in FY2015/16, driven by the collapse in global commodity prices, a range of supply-side measures, and a relatively tight monetary stance. It averaged around 5.4 percent in the first half of 2016-17, and dropped to a record low of 3.6 percent in November 2016 largely due to a fall in the prices of vegetables.
Consumer price changes in India can be very volatile due to dependence on energy imports, the uncertain impact of monsoon rains on its large farm sector, difficulties transporting food items to market because of its poor roads and infrastructure, and high fiscal deficit. Particularly the food inflation, which has remained above 8 percent for many months, is highly detrimental as a majority of the people spend almost 55 percent of their income on food bills. Structural reforms in the food supply chain like better buffer stock management and addressing the supply side constraints to ease the demand side pressures, are needed.
The declining trend of exchange rate value of the rupee is affecting the country’s economy, making imports expensive. In such a situation, when the higher cost is passed on to the consumer, inflation increases. The rupee has remained above 66 (per dollar) over 2016. The state is taking several fiscal initiatives to make the currency stronger and ease inflation, and these are likely to have their impact on the CapEx trend by industries.
India’s National Manufacturing Policy (NMP) aims to uplift the manufacturing sector and has set a target of 25 percent share of GDP from manufacturing by 2025. The policy also aims to enhance the manufacturing sector’s global competitiveness. Some of the state initiatives in the NMP include setting up a national manufacturing and investment zone (NMIZ) to promote investments in the manufacturing sector, promoting green technologies, promoting skill development programs to cater to the needs of the manufacturing sector, and such others. The policy will enable the country to emerge as a global manufacturing hub with extended forward and backward integration with the global supply chain.
While the state can only create the necessary policy ambience, the key players who can exploit the growth opportunities are the industry thought leaders. Meeting the consumer demand, which continues to remain relatively good compared with many other countries, rests with the industrial companies and the strategies they adopt to fulfill the demand while protecting their margins. While there is further scope to refine it, the state has played its part by announcing the NMP.
India’s sustained economic growth continues to propel demand for fuel, energy and basic materials. CapEx as a percentage of revenue seems to be higher for electric power industry, with NTPC and PGCIL sharing the majority of the capital investments for generation and transmission, respectively. Cement industry is also a major investor in capital assets, and cement production has been consistently increasing between 2008 and 2016.
The metal sector is witnessing recovery in demand mainly due to rise in exports. According to the world steel association, of the total global steel demand in 2016-17, 25 percent was supplied by India. Improved cash flows have also helped companies to regain confidence.
The Indian machinery market will also see strong expansion of production in coming years, with textile, construction, machine tools, and energy technologies being the key user industries. Since 2000, foreign companies have invested about $4.3 billion in machinery. According to VDMA (German Engineering Federation), this market in India is expected to grow by 8 percent in 2017 and the production index grew by 5.5 percent in 2016-17 compared to the previous year. India's machine operators serve the lower to middle price segment and compete with second-hand products and imports from Asia. Indian associations are trying to make imports of competitive products more difficult. This may result in more foreign companies setting up factories in India for supplying the domestic market. India’s economy remains strong, but headwinds like high domestic inflation, rupee depreciation, and fiscal deficit may continue to impede high growth.
The production of automobiles in 2016 has grown at around 5.4 percent compared to 2015. Passenger vehicles, commercial vehicles, and two-wheelers registered a growth of 9.3 percent, 4.6 percent, and 6.89 percent, respectively, in April-March 2017 over April-March 2016. More than 31 percent of all small cars sold globally were manufactured in India. However, automobile exports dropped by -4.5 percent on account of decline in export of both three and two wheelers.
The rising middle-class segment, young population, and strong domestic demand are the key drivers of the automotive industry in India. A wide range of products is now available for customers across various strata of society. In addition, reduced product lifecycle has forced manufacturers to expedite new launches. The industry attracted FDI worth $15.79 billion during the period April 2000 to September 2016.
The increased competition in the industry led to the adoption of more plant software. According to industry trackers, India’s robust domestic sales have made it the third largest automotive market in 2016 and account for 5 percent of global sales. Additionally, India is emerging as the center of excellence for compact cars.
Auto makers in India produce the entire range of passenger vehicles: multi-utility vehicles (MUVs), sports utility vehicles (SUVs), commercial vehicles, trucks, buses, tractors including farm, earthmoving, and construction equipment, and two- and three-wheelers. Almost all automotive segments (small cars, SUVs, luxury vehicles, and such others) have been experiencing growth. The country is becoming a global hub for automotive manufacturing, with increasing presence of the world’s top auto majors. The global automotive OEMs and Tier 1 companies are making India a supply chain center.
Capital spending in the automotive industry is around 3 percent of revenue, and out of the total CapEx, the automotive industry spends around 24 percent on plant and machinery. The overall revenue has been increasing since 2011, and the sales-per-asset showed a marginal rise in 2014 and has remained stagnant after that. The reason for this could be the gradual build-up of excess capacity in 2015, and surprisingly more capacity addition in 2016, albeit at a slower rate, as vehicle makers anticipate domestic demand to pick up.
The cement industry in India is expected to increase its total installed capacity to about 550-600 million tons per annum (mtpa) by FY 2025 from the current capacity of more than 395 mtpa, and retain its position as the second largest cement producer in the world. With over 188 large cement plants and 365 mini cement plants, India’s cement industry has tremendous potential for future growth as the government has planned to invest $1 trillion in infrastructure during the 12th five-year plan (2012-2017) and boost infrastructure and economic growth by developing 100 smart cities.
The cement output over the last decade has been on the rise, until it slipped in November 2016 due to implementation of demonetization. On top of this, excess plant capacity accumulated over the years has led to decline in utilization rates in 2017 compared to 2016, which is struggling to surpass 70 percent mark.
The escalating demand for housing and office complexes, hotels, hospitals, roads & highways, multiplexes, industrial construction, and such others is likely to spur the growth of the cement industry in India. Cement majors in the country as of now are expecting to grow by around 6 percent. The industry’s dominant players include large domestic companies, such as UltraTech, Gujarat Ambuja, JK, Grasim, ACC, and Century. Global cement majors with a large domestic presence include LafargeHolcim, Italcementi, and Heidelberg. Global companies entered the Indian market in the last decade lured by the opportunities in this industry. Some also plan to add production capacities through new projects or brownfield project expansions.
According to the ARC India CapEx index, the cement industry is the second largest in India in terms of capital spending as a percentage of total revenue. The capital spending in the cement industry is around 12 percent of revenue, and out of this total CapEx, the industry spends about 57 percent on plant and machinery. The CapEx spending has seen a downhill trend since 2012. Some improvement was seen during FY16 and similarly asset turnover ratio has also improved during that period. Period during 2015 and mid of 2016 turned out to be positive as demand outpaced capacity addition, which is reflected in the improved sales/asset ratio. This ratio is expected to improve in the medium term.
Indian chemical industry continues to retain its position as the third largest producer in Asia and 12th largest in the world in terms of volume. It also accounts for about 3 percent of the global chemical industry. The industry, having a large domestic demand potential and a diversified manufacturing base to produce quality chemicals, is likely to grow at 14 percent per annum, and is expected to exceed $350 billion by 2021. The chemical sector accounts for 13-14 percent of total exports and 8-9 percent of total imports in India. To further boost this sector, the government has approved 100 percent FDI in the chemicals sector, and policies are in place to set up integrated Petroleum, Chemicals and Petrochemicals Investment Regions (PCPIR). PCPIR is a dedicated investment region for manufacturing domestic and export-related products of petroleum, chemicals, and petrochemicals.
The expanding domestic market for automobiles, consumer durables, textiles, and such others is stimulating the demand for petrochemicals. Fine chemicals, dyes and intermediates, and knowledge-based chemicals also play a significant role in driving the growth of India’s chemical industry.
Petrochemicals (olefins and aromatics) are a major component of the domestic chemical industry, accounting for over 60 percent share by revenue. Demand for olefins and aromatics is expected to grow at about 10 percent and at 12 percent per annum, respectively, over the next four to five years.
According to the ARC India CapEx index, capital spending in the chemical & petrochemical industry is around 10 percent of revenue. Out of the total CapEx, this industry spends around 48 percent on plant and machinery. Over the last few years the capacity addition has been constant as can be seen from the CapEx/revenue KPI. Increased product and production complexity are the reasons why investment is stable. The conditions in the global chemical industry have been sluggish, whereas the Indian chemical manufacturers have fared better on account of stronger domestic demand. These companies have the opportunity to increase the utilization rate of their existing assets and improve sales per asset by catering to both the foreign and growing domestic market.
The electric power sector in India is witnessing several changes and new trends. The Government’s focus at present is on renewable energy, mainly solar power plants, which may have impact on the automation market as the requirement for solutions like DCS is less. Project delays due to financial/environmental clearances, and fuel unavailability have caused a delay in setting up power plants.
The country’s electric power industry, with a total installed capacity of about 319 GW as of March 2017, was globally the fifth largest in terms of generating capacity and third in terms of transmission and distribution network coverage. India became a power surplus country by the end of 2015, and this excess capacity has led to a slowdown in the capital expenditure in this sector.
According to the government, 188 thermal power plants out of a total 396 are more than 25 years old, and have a total installed capacity of about 56 GW. The government is planning to scrap many of these plants as they are beyond retrofitting.
Lately, there is an unprecedented price fall in the solar power sector in the country, and right now it’s cheaper than coal power. On the other hand, falling capacity utilization of power generation plants is compelling the industry to come up with innovative technical solutions including upgrades and modernization to bring more flexibility into operations that would allow quick ramp up or ramp down. Given these conditions, the industry is expected to remain in a state of flux in the medium term.
Once the structural problems and supply-demand gap in the power sector are addressed, the cash flow is expected to recover. The country’s economic growth is entering a phase where its dependence on expansion of infrastructure and manufacturing would increase, making the country’s economy more energy intensive. In order to meet the demand for good quality electric power, the industry has to upgrade the transmission and distribution assets and invest in automation to minimize energy losses. The government has planned to add more than 93,000 MW to the generating capacity during 2017-2022. Several number of steps and initiatives have been adopted, like the 10-year tax exemption for solar energy projects, in order to achieve India's ambitious renewable energy targets of adding 175 GW of renewable energy, including addition of 100 GW of solar power, by 2022.
India’s electric power industry needs to explore the benefits of investing in distributed generation, smart grid, and such other verticals. Renewable industry presently constitutes around 13 percent of the total installed base and is on an accelerated growth path in both solar power and wind power generating plants. Presently, India's clean energy capacity is 33,000 MW. India’s Economic Survey stated that the clean energy sector was likely to generate $160 billion in the next five years. This in turn is leading to the development of distributed generation topology and associated technologies.
According to the ARC India CapEx index, capital spending in the power industry is 28 percent of revenue. Out of this total CapEx, the industry spends over 67 percent on plant and machinery. The utilization rate and the plant load factor (PLF) has not been able to cross the 70 percent mark over the past five years. Due to the overcapacity in 2015, the CapEx/revenue KPI has also nosedived in 2016. The planned CapEx in renewable power is expected over the medium to long term, it remains to be seen how the gap between demand and supply is met using both thermal and renewable power. If renewable power is not scaling up as planned, then capital investments in thermal power plants will again pick up.
Investments in infrastructure is getting a huge boost with about $60 billion allocated for the current financial year for upgrading urban infrastructure, ports, airports, roadways, and railways that get the largest chunk of investments. To meet this domestic demand, India is planning to triple local steel production over the next decade. This would give a boost to local steel companies as well as attract investments from global majors.
A growing automobile market, along with power and cement, are the key drivers of the metals & mining industry. In 2011, the industry size was nearly $142 billion, which reached $232.4 billion in 2016. The government of India has allowed 100 percent FDI in the mining sector under the automatic route. India produces 88 minerals, and at present India is the largest producer of mica, fourth largest producer of crude steel, and fifth largest producer of bauxite and zinc, globally. Minerals like manganese, lead, copper, and aluminum are expected to witness double-digit growth in the years to come.
India’s crude steel production grew by 7.4 percent year over year (YoY) to 89.7 million tons (MT) in 2016. The total market value of India’s steel sector was close to $100 billion in 2016. Steel imports into the country fell 34.5 percent YoY to 3.01 MT, whereas steel exports rose 23.6 percent YoY to 2.38 MT during April-August 2016. NMDC, Sesa Goa, SAIL, and Orissa Minerals are the major players in the iron and steel industry in India. HINDALCO, NALCO, and BALCO are the major players in the aluminum sector in India. Based on the current investment plans of leading companies, India’s production capacity will double in the coming years.
The growing CapEx trend of companies in the industry creates huge opportunities for automation suppliers in India. According to the ARC India CapEx index, capital spending in the metals industry is about 17 percent of revenue. Out of this total CapEx, the industry spends over 78 percent on plant and machinery. The industry has been suffering from overcapacity in the last few years and the plant productivity levels had also dipped in 2015. It can be observed that the revenues as well as the asset utilization levels have picked up in 2016. This was mainly due to increase in exports and curbs put on preventing predatory imports. The utilization level in the industry is still low and is expected to rise in the coming years as companies increase production to meet domestic demand.
The oil & gas industry plays an important role in India’s economy, and the country depends on imports to the extent of almost 80 percent. The recent slump in global oil prices has benefited the refining sector and helped the country in reducing its trade deficit. India has emerged as a refining and petrochemical hub, and export of refined petroleum products accounts for high forex earnings. India has the potential to become self-reliant in the oil & gas industry, as over 55 percent of the 3.14 million sq. km of the country’s sedimentary basins are either poorly explored or unexplored. India’s government is targeting an investment of $100 billion in the oil & gas sector in the next five years to contribute to its Make in India plan. As part of this initiative, the government has allowed 100 percent FDI in many segments of the sector, including natural gas, petroleum products, and refineries, among others.
The demand for oil & gas is also set to rise significantly to support the growing population and expanding industrial base. The country’s oil consumption grew by more than 8 percent in 2016 as compared to global average of 1.5 percent. India is also trying to get investments from major oil & gas players in the Middle East as well as renew the lease of 28 oil & gas blocks in the country. The Government of India is also planning to merge state oil companies to create an integrated oil major that could compete globally, and leverage the synergy between the various entities to achieve efficiency and cost competitiveness.
Environmental regulations and policies have also put guidelines for clean fuel with minimum sulfur content. This will require huge expansion in India’s refining capacity. India is in the process of upgrading the automotive emission regulation known as the “Bharat Stage” (BS) norms, equivalent to the European emission standards, from the current BS IV stage to BS VI by 2020. This entails skipping stage V and in the process, would involve large capital investments in refinery sector, estimated to be about $7.6 billion for cumulative capacity expansion of more than 125Mtpa, over the next three years.
Currently, export of petroleum products contributes to almost 20 percent of India’s export earnings. India has some state-of-the-art refineries that enjoy relatively better refining margins as compared with its global peers.
According to the ARC India CapEx index, capital spending in the oil & gas and refining industry is 5 percent of its revenue. The oil & gas and refining industry in India spends 67 percent of the total CapEx on plant and machinery.
The CapEx has gradually increased after 2012-13 as companies intensified activities in upstream, LNG and shale gas production that resulted in investment in automation and field devices. Post June 2014, the CapEx/revenue KPI has dipped drastically due to low oil prices, and the sales per asset has also reduced together with the revenue. During 2016, growth in revenue continued to be sluggish and companies experienced reduced margins. Sales per asset may rise in the next 12-18 months, as companies are expected to utilize existing assets to improve productivity.
The Indian pharmaceuticals market grew at a CAGR of 17.5 percent during 2005-2016 with the market increasing from $6 billion in 2005 to $36.7 billion in 2016. The performance of the pharmaceutical industry has been impressive, and the market size is expected to exceed $55 billion by 2020. The industry has grown by targeting opportunities in the generic market and leveraging its strengths in drug formulation technology. The country has 523 manufacturing facilities that comply with US FDA (Food and Drug Administration) requirements, the highest for any country outside the US, and 80 that meet UK MHRA (Medicines and Healthcare Products Regulatory Agency) manufacturing requirements. Moreover, the US FDA has approved 630 drugs in 2016 and given tentative approvals to 183, higher than its 2015 figures of 580 final approvals and 146 in the previous year.
India’s pharmaceutical industry has emerged as a producer of quality drugs complying with global standards. Especially in the generic drug category, Indian companies have become experts in reverse engineering these formulations. However, much needs to be done in the operational aspects including supply chain efficiency and cost of delivery. It has learned the nuances of the generic drug market dynamics – identifying medicines that are going off-patent, filing the necessary abbreviated new drug applications (ANDA) and drug master files at the appropriate time, securing the appropriate FDA approvals, and such others, including willingness to overcome legal tangles. Third-party manufacturing holds a significant share in the production of drugs. The government is planning to phase out such manufacturing units or curtail it to only 10 percent of the total production of a company. This may put pressure on the companies to increase capacity, production and take up efficiency measures across the value chain.
The high margin biosimilar segment is emerging as a potential market and the industry needs to build up capacity and R&D to manufacture these. India’s government has unveiled "Pharma Vision 2020" aimed at making India a global leader in end-to-end drug manufacture. The government has also put in place mechanisms such as the Drug Price Control Order and the National Pharmaceutical Pricing Authority to address the issues of affordability and availability of medicines.
India’s biotechnology sector is among the top 12 globally. It has been growing at an impressive year-on-year growth rate of above 30 percent and is expected to reach approximately $100 billion in 2025. Global pharmaceutical companies are increasingly investing in India’s pharmaceutical companies to gain cost advantage and to meet global demand. As a result, India has been able to garner significant market share in exports.
However, the scenario in 2017 has changed and India’s pharmaceutical industry is dealing with several key challenges like reduced revenues and margins, and negative investor sentiments. Rising competition and fast approaching expiry of patented drugs, has made the generic drugs cheaper; the segment where India is a leading supplier. Regulatory compliance and quality issues also should be adhered to strictly. In order to recapture the slowly eroding market share and regain its foothold in the global market, will largely depend on how the industry redefines the business model, diversifies products, and evolve as innovators.
According to the ARC India CapEx index, the pharmaceutical industry’s capital expenditure is around 4 percent of revenue. The industry spends around 66 percent of the CapEx on plant and machinery. The capacity addition over the past year has given good results as can be seen from the rise in revenues and sales per asset KPI. For many companies, the profit rose by more than 40 percent in 2016. A substantial part of this came from exports and depreciation in the rupee also aided in realizing higher profit. The sales per asset is further expected to rise as companies aim to improve operational efficiency and productivity. Going forward, increase in plant productivity levels, capacity addition, compliance and product innovations would be needed to meet the global and domestic demand.
India’s food processing industry was about $258 billion in FY 2016-2017 and is expected to grow at a CAGR of 10-13 percent, according to industry experts. It is one of the largest industries in India and is ranked fifth in terms of production, consumption, and exports. India’s food processing industry accounts for 32 percent of the country’s total food market; 14 percent of manufacturing GDP; 13 percent of exports; and 6 percent of total industrial investment. The food processing sector is expected to attract $33 billion investment over the next 10 years.
The greatest influencer for this industry comes from megatrends, such as the increasing urbanization of the populace and growing purchasing power. Today’s food and beverage companies strive to be able to respond to consumer demand for a wide variety of fresh, nutritious, convenient, and high-quality foods. As many manufacturers operate globally, new product streams and their packaging/labeling must meet country-specific requirements and regulations. In addition, product formulas need to be adapted to suit different consumer tastes.
Several other favorable factors, such as the increasing trend in the consumption of processed food products and fiscal incentives being planned by the government, are capable of maintaining the growth momentum in the future. Food processing sector is emerging as a big market in India as only about 10 percent of India’s food production is processed. Anticipating the future growth, many global players are entering the India market by collaborating with the domestic players. This trend has emerged more strongly in 2016, providing opportunities to local players to widen their product portfolios. Several major players like ITC, PepsiCo, Coca Cola, Patanjali and such others have planned to invest in setting up greenfield plants and processing units in the next few years.
According to the ARC India CapEx index, the food & beverage industry’s capital expenditure is around 4 percent of revenue. The industry spends around 72 percent of the CapEx on plant and machinery. It can be observed that there has not been much variation in the sales per asset KPI over the years. The revenue growth has been steady and the industry has consistently expanded the manufacturing base by adding new production lines and extending plant capacity to meet the growing demand, even though productivity level could be improved. The combination of increased CapEx and constant sales per asset indicate that product and asset lifecycles may get shorter. The growing food processing sector in capital intensive and the CapEx/revenue KPI for this segment is likely to gradually rise.
The ARC India CapEx survey reveals the downward trend of overall capital expenditures, and it is necessary to address the productivity and utilization levels of the existing plants before embarking on undertaking new capacity expansions. India’s economic fundamentals, especially on the demand side, are still strong compared with the global economy. ARC believes that companies must focus on building strategic competencies that will make them best-in-class and invest in enabling automation and enterprise technologies to achieve productivity-led growth. Such investments would help companies manage their costs and protect their margins, a viable strategy to sustain market share as competition gets stronger.
ARC believes that industrial companies typically invest in automation systems based on health, safety, and environmental considerations. During the project engineering or conceptualization stages companies do not place adequate focus on achieving operational excellence. However, in the long term it is important for companies to focus on operational excellence. Here, automation systems can play an important role in empowering companies to achieve continuous improvements.
If you would like to buy this report or obtain information about how to become a client, please Contact Us