
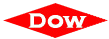




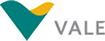

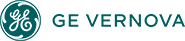




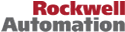

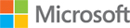
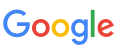

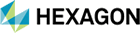


For the past 38 years, AspenTech has been successfully growing its portfolio of industry-specific applications for process engineering simulation, advanced process control, process optimization, and supply chain activities. Five years ago, Antonio Pietri, President, and CEO of AspenTech announced the company’s intention to pursue a new industrial strategy focused on optimizing the overall asset performance of industrial process facilities.
AspenTech briefed ARC Advisory Group on its latest initiative to this end. This involves helping its users move forward on their respective journeys to a self-optimizing plant.
AspenTech’s recent major software release (V12) includes functionality to support its Aspen Unified solution. This functionality rearchitects and further unifies its production planning, scheduling, and operations software. This helps break down organizational silos and optimize overall asset performance in refineries. Our key findings of the briefing include:
Today, many refinery planners, schedulers, and optimization engineers work independently using different data models with very little data integration. Even with these isolated practices, they have been reasonably successful at keeping units running to target. However, significant opportunities to improve margins remain. Planners will often run an off-line linear program (LP) optimization model to develop an average operating plan across the planning period (i.e., weeks and months into the future). Schedulers will break down the current planning period into a sequence of scheduled steps of the operation to ensure feasible management of inventories. This is subject to both scheduled and unscheduled events. Excel spreadsheets are often used to prepare a schedule. The scheduler will then manually pass along these spreadsheets with the operating targets to the unit control operator to implement via the on-line control system, typically utilizing advanced process control (APC).
This approach leaves operations with a plan based on average process behavior, but one that’s less than optimal. The daily schedule is feasible, but not necessarily optimized each day. The manual exchange of information between planner and scheduler leaves room for error. Unit control and optimization is based on regression models and, in many cases, the schedule cannot be achieved due to process variability, mechanical issues, or unplanned asset failures. After accounting for process interruptions, delayed startups, reduced rates due to supply or delivery issues, or other unplanned for problems, there’s a gap between plan vs. actual, often leaving significant money on the table. This gap is mainly due to modeling inaccuracy in both planning/scheduling and control models, and mismatches between planning, scheduling, and control constraints and targets.
According to the company, the “V12” release of its Aspen Unified solution is a critical component of its overall strategy to address what the company refer to as “margin leakage” between plan, schedule, and operations (process controls). AspenTech claims that, by aligning these activities, a refinery could increases margin, capturing from $0.05 to $0.15/bbl by vertically integrating planning, scheduling, and advanced process control in a closed loop. The V12 release includes a unified GDOT Builder (Generic Dynamic Optimization Technology) with data synergies to Unified PIMS. This offers future opportunities for tighter integration between planning, scheduling, and dynamic optimization.
According to the company, Aspen Unified can simplify and speed the refinery planning function for all users by streamlining scheduling through automated workflows. These unified planning and scheduling functions are built to deliver better business results, faster. V12 also includes the following key product updates:
All V12 Aspen Unified solution enhancements were engineered to help industrial process plants on their respective journeys to more autonomous operations. AspenTech shared with ARC Advisory Group its vision for a self-optimizing plant and where technology is heading.
An underlying factor in the future of the software solutions is to embed artificial intelligence (AI) into solutions so that it is transparent to end users. The company’s deep knowledge of the fundamental chemistry and knowledge of process plants is evident in this vision.
The company has defined key characteristics of a self-optimizing plant:
Each set of technologies and processes work together to predict future state and prescribe or automate optimal actions.
With the V12 release of its visionary Aspen Unified solution, AspenTech has made a large step forward to help transform production optimization business processes and – ultimately – help end users realize a self-optimizing plant. The re-architecture of the software means that previously isolated planning, scheduling, and operations work processes can now use a common data model. Unification of the planning, scheduling, and operations helps users close the gap between plan and actual. These connected and automated processes effectively unify planning, scheduling, and operations and enable the plant to run consistently closer to its limits. Operations gain a more accurate view of current performance and constraints. Models are more easily sustained by a simplified user experience to build consistency in models, enabling better business results faster with improved margins.
On a grander scale, AspenTech is creating industrial AI-enabled applications and embedding AI (combined with first principles science) to create a whole new class of applications and capabilities.
ARC Advisory Group clients can view the complete report at ARC Client Portal
If you would like to buy this report or obtain information about how to become a client, please Contact Us
Keywords: Refinery, Self-optimizing Plant, Planning, Scheduling, Optimization, Advanced Process Control, AspenTech, Aspen Unified, ARC Advisory Group.
Aspen, AspenTech, Aspen Unified Multisite, Aspen Unified, and Aspen GDOT are trademarks of Aspen Technology, Inc. All other trademarks mentioned are the property of their respective owners.