
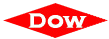




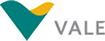

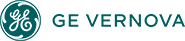




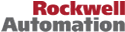

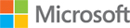
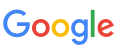

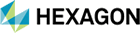


This Insight focuses on two of the most engaging and interesting sessions presented in ARC Advisory Group’s 14th India Forum. The sessions were presented by Dr. B. Ashok, Deputy Project Director, Aeronautical Development Agency (ADA) and Mr. Chethan. K, Group Director, Quality and Excellence Champion and Mr. Praful Kushwaha, Manager – IT Services, leading Industrie 4.0 deployment from Bharat Forge.
While Dr. Ashok spoke about how the aerospace industry has evolved and what we can expect in the near future, Mr. Chethan and Mr. Kushwaha shared the details of how Industrie 4.0 has helped their organization perform better. Both presentations provided perceptive details about the latest technologies and trends in their respective industries.
Dr. Ashok began the session by talking about how the aerospace and defense industries have been the pioneer in embracing technology; from the Internet to smart systems. He said that GE is planning to make various components in 3D printing technology. Military aircraft now use Big Data to monitor the flights and the health of the aircraft.
According to Dr. Ashok, the industry uses a “cocktail” of cutting-edge technologies. However, investors have not received consistent returns from this industry. The efforts required for vendor development and certifications are tremendous. As a component maker, if a company is manufacturing a part, besides regular standards like Nadcap for the aerospace industry, the component maker should also comply with the company's regulations and get it certified by the company.
Since aerospace is a low-volume but high-value/high-risk industry, Dr. Ashok suggested that it is more suitable for government or specialized organizations. Often, the number of aircraft that are actually manufactured is less than initially projected. From design concept to fleet induction takes at least 15 years.
The technology is also very complex - the gas turbine engine is still regarded as the most complex mechanical system. This means the designs should make provisions for implementing new technologies as they emerge. Also, in this highly regulated industry, managing and integrating the diverse vendors and their components is a task in itself.
Dr. Ashok went on to speak about the evolution of manufacturing technologies in the aerospace industry. He mentioned how the first aircraft were made of wood, but now employ sophisticated metallic components and intense machining, with 400 kilos of aluminum plate/bar machined down to 25 kilos of finished product. An array of disruptive technologies is also employed, like SPF-DB, 3D printing, and stealth coatings. The major systems in an aircraft include hydraulic, fuel, landing gear, ECS, health monitoring, fire warning, and avionics. Today’s aircraft also include smart systems like self-healing parts.
Computers and avionics are the game changers. Today, the aircraft practically fly themselves; essentially the pilots only need to take over on takeoff and landing. The aircraft has machine computers, which are on auto pilot control and the flight deck has flight, engine, and navigation instruments. Fly-by-wire technology with mission control computer takes care of routine functions. The sensors are based on MEMs (micro-electro-mechanical systems) revolutionized operational, handling and maintenance.
Dr. Ashok explained that work is cyclical in this industry. Initially, designers have maximum work and the manufacturing team is hardly engaged; later just the opposite is true. Hence, utilizing the manpower effectively is a big challenge. The volumes are low and the challenge is to innovate constantly.
Previously, aerospace was a separate industry vertical; but today it requires integration with vendors from many other industries. In India, aerospace is a government sector that cannot scale up without support from vendors that specialize in niche domains. Attention needs to be given to supply chain efficacy and strong R&D linkages.
Some present concerns in the industry include the noise levels of civilian aircraft and the cumbersome entry and exit procedures. Other than competing on cost (which is difficult to reduce), these are the only ways different airlines can differentiate themselves. The multiple standards and regulations in the industry also inhibit industry participants.
He said that remote monitoring is both a boon and a bane. For example, the Airbus A380 aircraft is controlled by a computer; so if someone hijacks the computer, it can be controlled remotely.
While concluding, he mentioned that this is the best of times for innovators and risk takers; and the worst of times for those wanting predictable cash flows. The challenge is in creating ecosystems and understanding the new age customers.
The session began with an introduction to Bharat Forge and the integration of value stream mapping and Industrie 4.0 in the company. According to the distinguished presenters, Bharat Forge has 16 plants spread over India and Europe and is the world’s largest forging company. It ranks among the top suppliers of engineered steel in India. As we learned, the company’s five pillars of excellence include: people management, performance management systems, operating systems, engineering systems, and customer satisfaction systems.
Operating systems - Value stream mapping involves doing more with less - not just in manufacturing, but across all operational layers. The company has competed 617 VSM projects; leading to a 225 percent improvement compared to 2014-2015. New Industrie 4.0 approaches are being added to analyze the breaks in information flow and provide digitizing services to strengthen the system. The company plans to view all operations based on information/data being generated and utilize it to make intelligent decisions. It has begun using an ECRS (eliminate, combine, re-arrange and simplify) approach to remove waste and implement Industrie 4.0.
Implementation scope - This includes smart connected enterprise, real-time electronic equipment (EE) monitoring, automated dashboards to track logistics performance index (LPIs) in real time, real-time equipment and process monitoring, real-time quality monitoring, real-time statistical process control, email and mobile alerts with escalation, and predictive analysis about equipment and process failures.
The five building blocks on which the Industrie 4.0 design will be based include:
In one of the company’s press lines, a 10,000-ton forging press is used in the manufacture of crankshafts and axle beams. The company procures bars and cuts them into pellets, which are heated to 1200 degree Celsius, before processing further. This is followed by the blocker operation and trimming where the extra material is removed. It is then padded to give it a neat finish and cooled.
The reports generated include seven of the company’s excellence charts, shift reports, operational charts, quality charts, machine health reports, audit forms, and so on to cover the activities from shop floor to top floor and vice versa. This has been captured on a single system and is also available online. Since the machines in the press line are on a shop floor network that is not connected to the office network, the company installed an intermediate computer to communicate these data. This centralized machine gets the data from the master controller and releases it to the firewall-protected data center.
According to the company, employing Industrie 4.0 in the press line eliminates manual data entry, saving over 2,000 man-hours annually. It has increased data integrity and availability. It also provides real-time OEE monitoring and automates dashboards tracking KPIs. The real-time equipment and process monitoring has improved response times. Real-time statistical process control (SPC) monitoring is also used to improve product quality. The system provides rule-based email and mobile alerts for escalation and predictive analysis of equipment and process failures.
These India Forum sessions reinforced how new product designs compel manufacturers in aerospace, automotive, and other industries to identify and implement new technologies, processes, and manufacturing approaches, such as IIoT and Industrie 4.0. This applies to public and private enterprises alike in India and all other countries with a significant manufacturing base.
Both sessions provided the participants with insights and meaningful takeaways about the various technical aspects and uses of the current trends in their respective industries.
If you would like to buy this report or obtain information about how to become a client, please Contact Us
Keywords: Aerospace, Industrie 4.0, Bharat Forge, ADA, ARC Advisory Group.