What is the value of improving operator effectiveness? In the early days of industrial automation, there were stories of some developing countries arguing that labor costs were so low they could put a human at every instrument, pump, and valve and avoid the expense of the process control system. This was swiftly rejected by the design firm. Engineers knew you could not actually operate a refinery or a chemical plant efficiently or safely in that manner. Based on ARC benchmark data, operators in the process industry typically have responsibility for between 90 and 180 control loops each. It is clear the operators main tool is the control system that informs and empowers an operator to outperform an army of workers without such a control system. A recent ARC study on operator collaboration asked survey respondents which past investments have resulted in the most benefit to operator effectiveness. The survey results indicate that improvements in the control, HMI, and alarming as the best of several investment options, with Operator Training simulators ranked as second.
In the blog post just a few days ago on Justifying Control Systems, the cost/benefit formulas show "improved process performance" is a key variable to justify the upgrade of an aging but highly automated control system. So how does operator effectiveness translate into improved process performance? And how does upgrading the operators control system play into the business interests of the company? Depending on the process, effective operators can get significantly more value out of the process in day-to-day normal operation. Production limited processes have a huge incentive to push against the production limiting constraints. Distillation is a workhorse process and notoriously hard to control. The distillation unit can process a lot more feed if the operator carefully regulates product purities. This can have the added benefit of shifting production to products that are more valuable and reducing reboiler heat. Distillation operating pressure can be adjusted to improve fractionation efficiency and energy use. Fin Fan motors can be turned off to save energy in cooler weather. The feed tray temperature can be adjusted to save energy and increase capacity. The reboiler consumes lots of thermal energy and in many cases, reboiler energy can be reduced, such as trimming excess O2 in fired heaters or fixing leaking steam traps for steam reboilers. Attentive operators with some collaborative help and an effective control system can make a big difference to the bottom line for facilities with distillation involved. Paper machines fill rolls of product at high-speed but a paper break halts production and valuable time is lost to clean out the paper jam and ramp production back up to full line speed. Many factors can influence paper breaks. Operator attention and effective regulatory control of the paper machine and the upstream pulping process can reduce paper breaks and really help the business. A pharmaceutical process can stack up expensive inventory waiting for quality approvals if batch production had aberrations that deviate from the perfect batch. Careful operators may be able to avoid such aberrations and free up such inventory for shipping. Operator effectiveness can be especially valuable during abnormal process operation. During explosions, accidents, or fires, the quick action of operators can save lives, protect the environment, and protect equipment from damage. It is not just operators that need to act, as maintenance staff, process engineers, and control system engineers can all contribute if they collaborate as a team. Many facilities act as if serious accidents will not happen at their facility and training programs can skimp on abnormal situation training. The cost of the top 10 industrial accidents is close to a $1 Trillion dollars with great human, environmental, and equipment losses. Chernobyl and Fukushima had the two largest damage estimates, but chemicals and refining had many multi-billion dollar accidents. Perhaps more investment in operator training could have saved maybe 10% of this damage or maybe $100 Billion dollars. Let us say an average operator-training simulator costs roughly $1 with immersive 3-D and dynamic process simulation capability. Accident savings alone would be enough to justify building a large number of training simulators - enough for virtually all manufacturing facilities involved with chemicals and petrochemicals. The dilemma faced by Fukushima operators was overwhelming as their control system quickly went black and they struggled to regain situational awareness without their main source of information. In April 2015 the NRC responding to lessons learned from Fukushima issued new guidelines to expand training for abnormal situation management. New technology abounds in the area of immersive 3D simulation used for operator training, and this complements the more established dynamic process simulation technology. The new millennial generation of workers already know gaming engines and high performance graphics interfaces using 3-D visualization, virtualization, and augmented reality. Control system suppliers now routinely provide the ability to execute the complete HMI, alarming, and control functions on a virtual computer with a connection to a dynamic process simulation. Collaborative training can resemble a multi-player video game and involve multiple operators, maintenance staff, process engineers, and certainly control engineers.
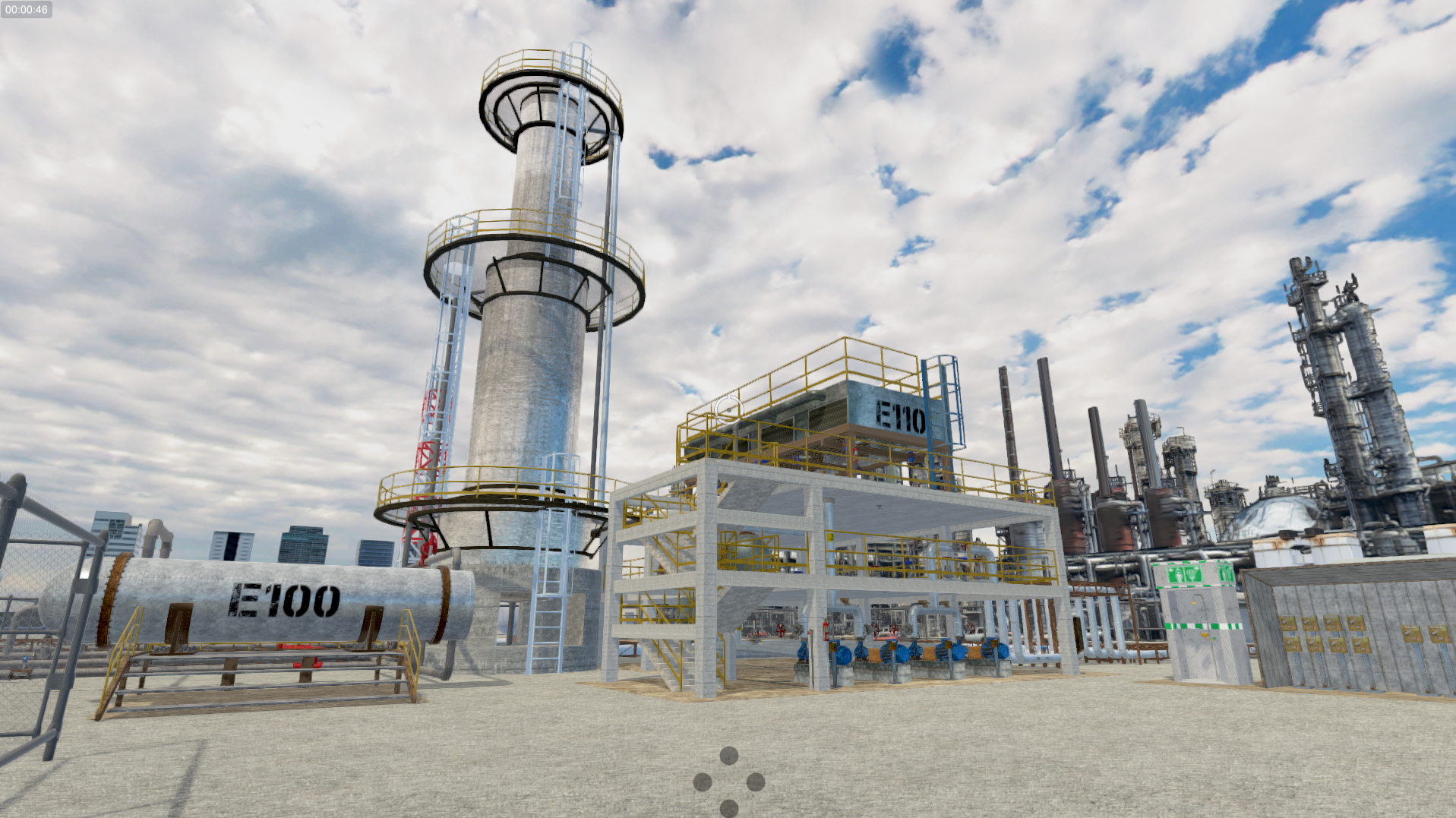
When immersive 3-D environments are integrated with dynamic process simulation using the exact control system HMI, training and control system testing are highly realistic. Simulation construction typically connects unit operation model templates to match the physical plant. A key part of cost control is to share common data. The instruments, P&ID drawings, and the entire control and HMI database all shared data elements. Sharing data with a single version of the truth should keep the simulation and the running plant synchronized when adding a new instrument or updating an alarm setting. There are many examples of sophisticated simulation efforts that are used once and abandoned. It takes some extra planning if simulation capability is to be maintained long-term. The development and use of a simulation likely involves a software platform and some consulting services for initial construction. The development process should encourage effective collaboration between operations, engineering, maintenance, and business management. The maintenance and use of the simulator requires teamwork and encourages collaboration. Nuclear plant operators like aircraft pilots are required to use dynamic training simulators as a key part of their training. Aircraft simulations are relatively high fidelity, as they are useful for a large number of identical aircraft. Simulations for manufacturing plants tend to be one-of-a-kind so value decisions need to be made. Using modular first principle models for dynamics can be easier to build and maintain. Steady state and dynamic fidelity needs to be optimized and it is cheaper to move from low to higher fidelity. 3-D immersive simulation is gaining traction. It is more useful for training in abnormal situations and there is more challenge to justify this for brownfield projects. Immense progress in software and technology has been made already and any simulation project should expect this 3-D immersive technology arrive soon. A key challenge is how to gain value from this new technology.