
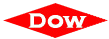




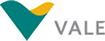

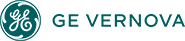




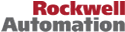

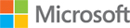
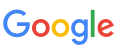

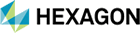


Bentley’s BIM Applications Improved Design Efficiency by 30% and Shortened Project Schedule
The Jinnan Steel Group, a merger of two steel production companies in Quwo County, China, has established a 10-million-ton-grade steel production base in the region. The steel manufacturing company hired WISDRI Engineering & Research Incorporation as the engineering, procurement, and construction contractor for the second phase of the Quwo plant’s steelmaking and continuous casting project. This capacity replacement project will improve production quality and efficiency by optimizing the plant’s layout. The upgrades included adding a 150-ton converter, a hot metal desulfurization station, a 1F furnace, and a notable 12-strand billet continuous caster to the steel production plant.
Jinnan Steel Group wanted this project to be economical, sustainable, advanced, and reliable. Therefore, they required WISDRI to meet environmental protection standards by lowering overall energy consumption, recycling waste gas and water, and minimizing any plant-related carbon emissions.
To meet these requests, WISDRI sought to construct an environmentally friendly steel plant with state-of-the-art equipment. However, the capacity replacement project at the Quwo manufacturing plant presented a variety of unique challenges. Design work had to be coordinated among 15 different engineering disciplines within 13 separate systems. Additionally, the engineers had to ensure that the new structural arrangement would fit within the existing building’s available space. As a result, the equipment required precise, intricate organization to avoid clashes.
Because collaboration with 2D drawings is inefficient, WISDRI needed an integrated 3D modeling platform that facilitated communication among the multidiscipline project team and could handle the creation of more than 400 models. Lastly, the COVID-19 pandemic required the project team to undertake all engineering design from a home office. With a dispersed workforce, WISDRI had to support continuous communication and deliver high-quality designs by the project’s deadline.
After considering their options, WISDRI implemented Bentley’s open modeling solution based on ProjectWise to overcome the project’s logistical and technical constraints. WISDRI created an original cloud platform to host the organization’s internal product lifecycle management system and ProjectWise. All design data and models were stored on the virtual platform. Designing on the original cloud platform enabled the multidiscipline design team to work remotely during the pandemic and collaborate in real time. The engineers, contractors, and client were engaged for feedback throughout the design phase by reviewing all models associated with the new plant layout through ProjectWise.
Bentley’s integrated BIM software—comprising OpenPlant, OpenBuildings, Bentley Raceway and Cable Management, and ProStructures—included a comprehensive component library for steelmaking projects, which included 50 parameterized equipment models, that were indispensable in creating accurate 3D models of the plant. Furthermore, automatic generation of drawings and material lists in Bentley software led to higher-quality designs. WISDRI also developed an automatic annotation tool that contained templates for specific design disciplines to facilitate easier collaboration.
WISDRI met Jinnan Steel Group’s environmental sustainability requirements on this project by calculating carbon dioxide emissions during design. The project team optimized the ventilation route with AutoPIPE to shorten duct length, reduce resistance loss, and make dedusting more efficient. BIM technology also allowed the team to increase casting speed with the ladle turret by 5% and decrease temperature distribution by an average of 5 degrees with the tundish to reduce overall energy consumption. Construction simulation in SYNCHRO increased the amount of prefabrication work prior to on-site installation. This advancement established safer working conditions and boosted efficiency to certify that the project was completed on time. Automatic steelmaking technology was incorporated into the design to certify employee safety during plant operations and maintenance. By combining the 3D models with intelligent manufacturing techniques, WISDRI delivered an innovative steel plant based in smart technology. Powering the overhead crane with an intelligent logistics system limits the need for an on-site operator and simplifies equipment maintenance.
Using Bentley applications, WISDRI saved 300 hours of communication time to lift design efficiency by 30% and cut design time by 45 days. The digital solutions supported simultaneous engineering work among 15 separate design disciplines to avoid 166 major collision points on the Quwo steel plant. Moreover, simulating construction in SYNCHRO removed 60 days from the construction timeline to save CNY 1.8 million on the project. Most importantly to the client, using the modeling software to quantify carbon dioxide release lowered the plant’s carbon emissions by 0.1 ton per every ton of steel to achieve the energy conservation requirements on this project. Conquering so many obstacles and building a cost-efficient, sustainable steel plant that contains intelligent, cutting-edge technology, WSIDRI is now a new leader in applying digital solutions in the metallurgical field.
Organization: WISDRI Engineering & Research Incorporation Limited
Solution: Manufacturing
Location: Quwo, Shanxi, China
Project Objectives
Project Playbook: AutoPIPE, Bentley Raceway and Cable Management, LumenRT, Navigator, OpenBuildings, OpenPlant, ProjectWise, ProStructures, SYNCHRO 4D