
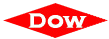




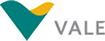

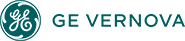




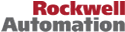

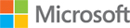
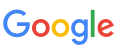

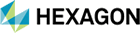


Client Profile: Established in the Netherlands in 1977, the WP Group is a leading supplier of performance-defining components for motorcycles and automobiles. It consists of two main companies: WP Performance Systems GmbH, which designs and manufactures suspension parts such as shock absorbers, front forks and frames as well as exhaust systems; and WP Components GmbH, which produces water and oil radiators. Headquartered in Austria since 2009, the group has more than 600 employees. It manufactures over a million parts per year, serving market-leading OEMs in Europe, USA, and Asia. Although WP also operates a radiator plant in China, the company manufactures nearly 90 percent of these radiators in Munderfing, near Salzburg, Austria.
Background and Bottlenecks: Since the company focuses on vehicle performance as well as user experience, WP components are used by virtually all major motorcycle racing teams and manufacturers. Almost every motorcycle produced in Europe has a WP radiator on board, and in total 400,000 radiators per year are produced for more than 200 different custom-made products. Although this quantity is not particularly high for automotive components, the volume has grown rapidly since the production facility opened in 2012, and so has model variety. Increasingly, assembly workers had to work overtime to meet the production requirements. The challenges were:
Fabian Steinbacher, project manager at WP Performance Systems, conducted a material flow analysis of the radiator assembly process. He deduced that the workshop-like environment in which all radiators were assembled on an array of individual stations was hampering the material flow. To address this problem, he pursued a solution path involving the separation of high and low runners and flow production for the high-quantity parts.
Working out a Solution: Further, he investigated the feasibility of various concepts to rearrange the radiator assembly. To build and optimize the digital twin of the radiator assembly facility, he used the Plant Simulation solution in the Tecnomatix portfolio from Siemens PLM Software. The Tecnomatix portfolio includes software products for the digital factory primarily used by original equipment manufacturers (OEMs) and suppliers to streamline their production lines, and provide the scalability needed to adapt to smaller applications. By creating a digital twin of the radiator assembly facility the workplace layout and tool arrangement was optimized.
The Tecnomatix software enabled simulation of different scenarios in a realistic manner, optimizing the internal material flow. Using the 2D and 3D capabilities of Plant Simulation, a functional model was created of the entire radiator assembly facility, including the workers at their stations. The entire process of creating and optimizing the material flow using the digital twin of the production plant was achieved in less than three months. With the SimTalk advanced simulation programming language in Plant Simulation, it was easy to add and modify special features as needed. What was particularly useful is the ability of Plant Simulation to automatically reallocate the employees dynamically among the stations to optimize throughput depending on the time required for individual processing.
Quantifiable Results: Although the investment for redesigning the radiator assembly system was significant, it brought in cost-justifiable results. As it is based on reliable simulation results, the optimizations and fine-tuning are done before installation and not during operation. An effective doubling of production capacity is not the only advantage of the simulation-based remodeling and introduction of the two-shift operation. This arrangement is also less sensitive to disruptions, requires fewer tools and generally reduces investment and improves capacity utilization. Siemens Plant Simulation solution:
Following the success of this project, the company has decided to create digital twins of all their production facilities to streamline and optimize functions and processes.
Keywords: Siemens PLM Software, Tecnomatix, Plant Solution, Digital Twin, Simulation, ARC Advisory Group.