
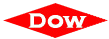




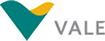

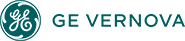




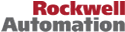

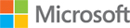
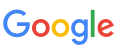

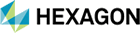


Rockwell Automation introduced new enhancements coming to its PlantPAx distributed control system (DCS). These are designed to help process operations capture additional value across the plant and enterprise where the requirements for secure connectivity between the device and the enterprise is needed to help achieve digital transformation. PlantPAx helps to make this connectivity possible through its alignment with plant-wide automation technology and use of open communication standards.
The next PlantPAx DCS release will help users to reduce unplanned downtime and improve system availability. This includes support for Parallel Redundancy Protocol (PRP), an industry standard for redundant Ethernet, helping to enable more secure controller and I/O communications.
The next release will also feature updated human machine interface (HMI) and trending tools to help increase productivity, and improve effectiveness of operations and maintenance functions. This includes an enhanced Library of Process Objects to better align with industry display design standards. The expanded library also includes more intuitive integration with electrical protection devices, leveraging both EtherNet/IP and IEC-61850 communication standards. This helps to further extends plant-wide control capabilities and connects electrical management and control, which helps to reduce infrastructure duplication, ease implementation and lower total cost of ownership.
Rockwell Automation introduced its new Project Sherlock artificial intelligence (AI) module, designed to help create and diagnose analytics solutions in industrial operations that have previously required data scientists with a deep understanding of the specific application to be analyzed, and often required a great deal of time to understand and model the system. Rockwell Automation embeds this expertise via a data-driven analytics algorithm into the new Project Sherlock AI module.
This data-driven analytics algorithm is delivered inside a module that fits directly into the controller chassis. Once installed, Project Sherlock AI leverages physics-based modeling to learn the application that controller manages. The solution searches through controller tags to identify the application or allows users to choose what they would like modeled by selecting inputs and outputs via an add-on-instruction (AOI). Project Sherlock AI can then learn from the stream of data passing through the controller to build a model. This process can be accomplished often in a short period of time. Large quantities of historical data are not required, nor must the data ever leave the automation layer.
Once the model is built, the Project Sherlock solution watches the operation looking for anomalies against its derived, principled understanding. If it spots a problem, it can trigger an alarm on an HMI screen or dashboard. Future iterations will go beyond diagnostics to direct users on how to remedy the issue or to automatically adjust system parameters to fix the problem without human intervention.
Project Sherlock diagnostics offer reduced false-positive alarms as compared to some other artificial intelligence solutions due to its physics-based modeling and foundation in industrial applications. For example, Project Sherlock AI can tell if a boiler temperature shift is related to a benign change in upstream operations or an abnormality that requires correction.
The initial version of Project Sherlock AI will include ready-to-use templates for boiler, pump and chiller operations, suited for process or hybrid applications. Users can model additional applications with guided configuration.
Communications with the module are prioritized by the controller, so users can select how much data is sent and intervals of communication. The module does not add to controller CPU-load nor add to network traffic. Project Sherlock AI pilots have been running for the past 18 months. Customers will be able to purchase the module in mid-2018.
Rockwell Automation announced the expansion of its Connected Services offerings portfolio, designed to help meet its customer’s information infrastructure and security needs. These Connected Services are designed to help the large number of industrial companies that are implementing digital technologies aimed at optimizing operations. Whether targeting point solutions or undergoing a full digital transformation, most organizations need support to plan for, deploy, and maintain new solutions, or to help them maximize the most value from digitalization.
Connected Services offerings include industrial infrastructure assessment, design, implementation, support and monitoring capabilities including Infrastructure-as-a-Service (IaaS), remote asset monitoring and predictive maintenance, cybersecurity threat detection and recovery, training and consulting offerings. These software-powered services build on existing application and product support services to help organizations access and use production data to help improve asset utilization and productivity, while reducing risk and time-to-market.
For example, according to ARC Advisory Group, the cost of unscheduled downtime in industrial operations exceeds $20 billion. Through traditional means of detecting, diagnosing and fixing downtime, approximately 76 percent of downtime occurs before any corrective action is undertaken. Connected Services can help users detect and resolve issues faster, reducing downtime reportedly by as much as 30 percent.
Connected Services offerings start with building a secure information infrastructure. Network and cybersecurity services include assessments and design, technical support, IT/OT training, remote monitoring, threat detection and recovery, turnkey implementation, pre-engineered network solutions, and network monitoring and management. These services help to speed the integration of new equipment and systems, improve security, and reduce downtime with access to technical resources.
Remote support, monitoring and response services can prove important for critical processes through around-the-clock operations and remote operations. These services can complement on-site maintenance teams, ranging from continuous machine monitoring and incident response to 24/7 remote support and software/firmware updates. Deployments can make use of the FactoryTalk Cloud gateway, on-premise Rockwell Automation Industrial Data Center servers, or a hybrid model that combines both options to help improve productivity and reduce downtime.
Data integration and contextualization services can help capture data and convert it into actionable information. These services can provide additional opportunities to help increase productivity. Producers can help to reduce skills gap challenges by leveraging Rockwell Automation to monitor, maintain and manage the network, equipment or full applications. Additional digital transformation and data scientist consulting services will be available in 2018.
Connected Services offerings are also scalable, allowing producers to help build ROI as they go, and rely more on OPEX than CAPEX funding. Rockwell Automation can deliver and execute Connected Services offerings globally, providing organizations with more consistent support across operations.
Rockwell Automation announced its enhanced machine safety portfolio, which includes a range of input, logic and output devices designed to help companies make it easier to provide safety as a core function of smart machines. The enhanced portfolio is designed to address the challenges of providing hardwired or add-on safeguards, which can lead to longer machine design times and lower operational productivity.
The Rockwell Automation machine safety portfolio now includes the new Allen-Bradley GuardLogix 5580 controller, Compact GuardLogix 5380 controller, and Compact 5000 safety I/O. The portfolio also has new safety functionality with the Allen Bradley Kinetix 5700 servo drive. All of the devices are designed to communicate over EtherNet/IP and are tested against machine safety standards to help to ease compliance.
The GuardLogix 5580 and Compact GuardLogix 5380 controllers expand the Integrated Architecture portfolio by bringing safety into the latest generation of the Logix 5000 series controllers. They provide faster system performance and new options for meeting SIL 2/PLd safety requirements or higher. This can help machine designers to simplify their architecture and reduce control chassis footprint by scaling machines to the specific required safety rating, rather than using a controller designed only for higher ratings.
The Kinetix 5700 servo drive now includes five safe-stop functions and three safe-speed monitoring functions to help create smarter and more productive machines. These functions allow a machine to remain active while simultaneously being safely monitored. They also allow operators to perform maintenance and minor servicing tasks while a machine is running. For example, when used with a SIL 2 VP motor, the Kinetix 5700 servo drive can help to reduce system wiring, complexity and costs.
Safety modules are also now available in the Compact 5000 I/O family. They provide local and remote safety I/O for the Compact GuardLogix 5380 controller and remote safety I/O for the ControlLogix 5580 controller. They also provide high-speed I/O communications and help to reduce the overall panel space required.
The portfolio also includes smart safety devices, such as safety relays and light curtains that can be connected via the GuardLink safety-based communications protocol. This allows users to more easily identify which device was activated during a production stoppage, rather than manually investigating all devices on a machine or line.