
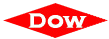




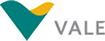

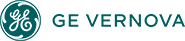




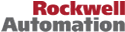

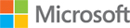
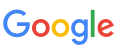

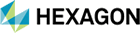


A session at the 2019 ARC Industry Forum in Orlando, Florida focused on leveraging Industrial IoT and operational analytics to realize digital transformation in oil & gas. At this well-attended session, one end user discussed how his company was being transformed by leveraging digital technologies to integrate and optimize its oilfield service operations. A second presentation discussed deploying wireless instrument networks to reduce costs and support mobile operators in the process areas at a refinery in Bahrain. The third presentation focused on how leveraging cloud-based solutions enabled that company to build a digital oilfield operations project from scratch.
As the lead in to this Forum session, ARC Advisory Group analysts provided a brief overview on the outlook of the oil & gas market, ARC’s definition of Industrial IoT, major upstream and midstream oil & gas applications that can benefit from digital technologies, the need for strong automation and technology partners to ensure successful implementation and integration of digital technologies; and briefly discussed the impact of edge computing and blockchain technology in oil & gas applications.
Dion Ballard, Technology Development Manager at Halliburton, spoke on his experiences at Halliburton over twenty years in engineering and operations groups and how, last year, he joined the digital transformation team. As we learned, Halliburton, which recently celebrated its 100-year anniversary, has two divisions: Drilling & Evaluation and Completions and Production. Within these two divisions are fourteen product service lines. These act as fourteen separate businesses spanning the entire cradle-to-grave well lifecycle, from evaluation and drilling through plugging and abandonment.
Halliburton generates a lot of data across these separate product service lines. Mr. Ballard provided the example of a single hydraulic fracturing blender, which can generate 22,000 signals per second. Halliburton needs governance around all that data and must deal with data silos within each of these product service lines, which manage their own businesses, business models, and track their data differently. Within the IT infrastructure, each Halliburton business had been free to put the data wherever it wanted to. Some of these businesses were still storing and sharing data on hard drives, thumbs sticks, or individuals’ laptops.
To overcome these hurdles, Halliburton started by developing a digital layer across the organization and that lets it share data internally and with customers. The company is building data lakes and real-time systems that will enable it to move data around in similar formats such as for edge devices. In addition, the company is trying to change from a siloed culture to one that’s much more collaborative. To this end, it has developed a horizontal data analytics team that works with each product service line to use that digital backbone to meet its business objectives. Mr. Ballard is part of the completions and production analytics team. He commented that some product service lines are making good progress, but others appear to be holding back in their adoption of this new initiative.
His final points were that the digital transformation teams have critical buy-in from management, the culture is beginning to change, and Halliburton is moving in the right direction to digitally transform the company over time.
Michael Thorsen, President of California-based, Temblor Petroleum Company, presented an overview of the company and its current operations as an independent oil & gas exploration and production firm.
Mr. Thorsen discussed the company’s first gas project as an operator, which enabled it to develop the project from scratch and thus avoid traditional, outdated oilfield operations such as manually operated valves and equipment, analog gauges, onsite operators to manage process flows and production streams, local alarming, visual beacons, audible alarms with no automated mechanical responses, and manual/mechanical shutdowns for alarm issues. The company wanted to avoid manual operations and data collection and management as much as possible to improve production and speed response to alarms and other issues.
The objective was to build a facility using the current technology to:
Given the company’s small size and lack of resources, Temblor partnered with Tyrion Integration to handle both the electrical and control system design and integration and cloud integration. Another partner, Pros Inc., was tasked to handle the oil and gas testing facility and management as well as vessel and equipment fabrication and design.
David Pitzer, Director of Automation, at Tyrion Integration, talked about how the company leveraged the Bedrock Automation platform for the project. This provided local, cyber-secure monitoring and control, secure power management and backup, automated reporting for well testing, and – in conjunction with Tyrion Cloud services – 24-hour remote surveillance and SMS alarm notification. Tyrion developed the system I/O, field instrumentation and controls hardwired to the Bedrock Automation controller, which handled all the shutdown and safety monitoring and it was backed up by Bedrock’s secure power supply and UPS. The reliability for mostly unmanned monitoring was critical to the project.
Tyrion developed a local network for local operator interaction while onsite using its Nucleus device to dynamically pull all the information from the Bedrock Automation controller and send it to the Cloud where operators and owners can see the data from any device, including mobile devices. According to Mr. Pitzer, Bedrock’s control system met the requirements for a control system that was quickly deployable, flexible, and scalable. It also offered elevated cybersecurity, which was critical for largely unmanned operations. Reliability was also critical and, as Mr. Pitzer explained, the Bedrock control system was designed to be a “bullet-proof” platform. For SCADA, Tyrion needed something simple. It leveraged Tyrion’s Cloud services for plug-and play-performance. The platform provides the needed trending, alarming, notification, and reporting capabilities, plus the protocols needed to connect to Bedrock’s cyber-secure system.
The system Tyrion provided enables 24-hour remote surveillance, access to the data from any device, and can notify the right person immediately to rectify any problem. The system also provides automated well testing and facility reports.
Mr. Pitzer claims the company saved $50,000 compared to a traditional control system due to simplified architecture, which reduced the amount of controls engineering and spare parts required. Also, there were no licensing fees. Cloud services streamlined deployment to minimize the time that would otherwise be spent installing traditional SCADA system infrastructure. He also mentioned that the system is well equipped for the future: it is built on industrial standards and programming languages, cyber-secure by design, and all data resides in the Cloud, offering opportunities to leverage future technologies.
Parameswaran Vaidyanathan, Superintendent, Instrumentation Engineering; and Bharadwaja Prabhala, Senior Engineer, Instrumentation, at Bahrain Petroleum Company (Bapco), discussed how the company successfully deployed a novel cellular approach to greenfield device networks at the Alba Gas Station (AGS) project in Bahrain.
Mr. Vaidyanathan kicked off the presentation by highlighting why the project won the 2019 Wireless Compliance Institute Wireless Excellence in Automation Award, awarded later in the session by Andre Ristaino, Managing Director of the ISA100 Wireless Compliance Institute. This award recognizes innovations, creativity, and engineering excellence in deploying ISA100-compliant wireless. He then provided an overview of Bapco, a state-owned oil & gas company engaged in exploration, refining, storage, marketing, training and development and environmental initiatives in the kingdom of Bahrain. Bapco owns a refinery with a storage capacity of 14 million barrels, a marketing terminal, and a marine terminal for the transfer of petroleum products. The company exports 95 percent of its products. The refinery is undergoing a capacity expansion from 270,000 to 360,000 barrels of oil per day.
Mr. Vaidyanathan then outlined the major automation technology milestones since 1984 and highlighted the greenfield wireless network infrastructure and scalable custody transfer skid for gas initiatives. He provided an overview of the Alba Gas Station project, a new unmanned gas distribution network designed to supply high-pressure Kuff gas and low-pressure residue to the upcoming Alba Line 6 expansion, which feeds one of the largest aluminum smelters in the world. The plant comprises gas pre-conditioning systems, condensate knock-out/transfer systems, metering skids, and vent/flare management systems.
ARC Advisory Group clients can view the complete report at ARC Client Portal
If you would like to buy this report or obtain information about how to become a client, please Contact Us
Keywords: Analytics, Bahrain Petroleum Co. (Bapco), Temblor Petroleum, Industrial IoT, Halliburton, Wireless, ARC Advisory Group.