
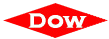




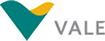

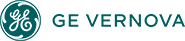




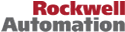

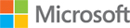
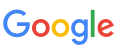

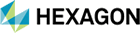


At Bentley System’s annual Year in Infrastructure conference, there were 302 nominations from 51 countries, and 2 projects from China emerged as winners. Meanwhile, it is noteworthy that the 3 finalists in the Process and Power Generation category all come from China, namely Shenyang Aluminum & Magnesium Engineering & Research Institute Co., Ltd. (SAMI for short), MCC Capital Engineering & Research Incorporation Limited (MCC for short), and Shanghai Investigation, Design & Research Institute Co., Ltd. (SIDRI for short).
This project is invested and constructed by Shanxi Chinalco China Resources Co., Ltd, located in Lvliang City, Shanxi Province. The Phase I construction includes an electrolytic aluminum production system and supporting facilities with a capacity of 500,000 tons/year. With a total investment of RMB 3.94 billion and an area of 750,000 square meters, the project was put into operation in May 2018.
With China expected to achieve carbon dioxide peaking in 2035 and carbon neutrality in 2050, Chinalco responded quickly and rolled out strategic plans to accelerate the digital transformation of the group company. The goal is to establish a complete digital model for the whole factory, linking static information such as design and construction to the model, forming a professional digital delivery outcome, and applying digital twin technology to project design, construction, and operation management. However, this project involves 13 disciplines, 52 sub-projects, and a large scale of construction, which increased the project complexity and difficulty.
SAMI undertook the digital modeling, digital delivery, and digital operation and maintenance implementation of the project. It took five years from the start of 3D design in 2017 to the final implementation of digital twin plant operation and maintenance application in 2022. SAMI almost made full use of Bentley’s integrated software solution, which contributed a lot in this project.
Bentley series software and engineering database were used to build 3D digital modeling of the entire plant's facilities. Its openness and data standardization enabled lightweight model creation and data structuring more efficiently.
Bentley applications, like Synchro4D, Navigator PC and mobile devices were used for project control and quality management.
Bentley iTwin platform was used to integrate project models with various information, creating a digital twin factory and setting a model for aluminum industry digital transformation.
Bentley design platform and iModel technology ensures the smooth digital delivery and implementation of the project.
Bentley ProjectWise collaborative management platform to centrally manage project resources. Through a standard identification and coding system, SAMI scientifically and efficiently managed over 300GB of data for this project.
This is the first plantwide and full-stage digital twin model in the aluminum industry, with the digital model built by Bentley series software, combined with SAMI's digital delivery platform. Fangbo Liu, Director of Project Operation of the Digital Center from SAMI shared with us their breakthroughs and experience on this project:
Data-based models were built to cover data of this project and nearly the whole aluminum industry.
Automatic coding, as digital DNA, was realized via Smart PID platform, instead of coding and assigning attributes manually.
Full digital simulation for core projects was developed innovatively to control engineering quantity, project progress and cost.
Optimizing space layout via 3D models helped save materials for civil engineering and process pipelines.
Progressive digital delivery was realized, including coding, database, 3D designs, procurement documents, etc.
Operation and maintenance came in when automation level of personnel and production lines reached a certain level.
This project has set a good example for peers from the non-ferrous industry in China and even worldwide. Many benefits have been achieved in quantitative ways:
Modeling time shortened by 15 percent (~200 working days).
Comprehensive management costs reduced by 10 percent (over RMB 6 million annually).
Non-predictable equipment failures down by 40 percent.
Fluoride emissions decreased by 5 percent.
Headcount reduced by 10 percent (~RMB 1 million in annual labor cost saving).