
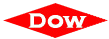




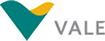

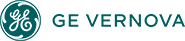




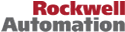

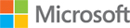
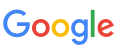

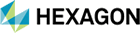


APC Performance, LLC, recently briefed ARC Advisory Group on the company’s “next-generation” solution for advanced process control (APC). As we learned, this is designed to provide many of the benefits of conventional model predictive control (MPC) solutions, but without the associated cost and complexity.
Traditional MPC solutions require extensive model-building and subsequent maintenance by APC engineers and typically involve large, compute-intensive matrices plus an embedded optimizer. The resulting ownership challenges have led a handful of APC suppliers to take a fresh look at APC, one that improves operational performance while reducing cost-of-ownership. APC Performance calls this emerging paradigm “APC 2.0.”
As we learned, APC Performance’s approach leverages the intuitive knowledge of plant operations and process engineering staffs, and employs a “small-matrix” approach that can be deployed directly on a typical DCS platform. According to the company, its solution can greatly reduce dependence on outside APC expertise; an increasingly scarce resource.
Key takeaways about APC Performance’s solution include:
Designed to take advantage of the process and control knowledge of plant operations and engineering staffs
No models to build or maintain
Small-matrix approach focuses on key variables and core application value
Includes solutions for single-loop control and multivariable APC, using a common, “model-less” approach
Novel control algorithm adapts to changes in process gain, thereby enabling the “model-less” solutions
More scalable for smaller plant applications where, in the past, APC might have been considered impractical to implement and maintain
Focuses on “operational” performance to help solve the competing priorities that have long undermined both single-loop and multivariable control performance
Conventional MPC Not a Panacea
Conventional, model-based multivariable predictive control (MPC) has been around for almost 30 years and is widely used in refineries, petrochemical plants, power generating plants, and other process plants. In principle, MPC allows industrial processes to operate safely closer to constraints, providing significant opportunities for economic optimization.
However, it’s widely known that conventional MPC solutions can come with challenges. As Allan Kern from APC Performance, LLC, explains in a recent white paper:
“Large matrix, model-based multivariable control has been the dominant advanced process control technology in industries such as oil refining, chemicals, and petrochemicals for going on three decades. The virtues and successes of MPC aside, it has also earned a reputation as an ownership challenge in many areas, including cost, maintenance, support, and performance. While MPC may always be the preferred solution in select applications, many end users have long been moving away from MPC as an everyday tool.”
ARC research indicates that while traditional MPC implementations continue to provide many companies with a competitive advantage, other users have become frustrated with the technology due to the need to frequently update the models to adapt the MPC to changing process conditions, new equipment, variations in feedstocks, environmental factors, etc. In fact, we occasionally hear end users comment that, since their process control operators don’t trust the APC, they frequently turn it off, reverting to either PID control, or – in all too many cases – to manual control. Other companies that could potentially receive significant economic benefit from MPC (primarily smaller companies with smaller budgets and fewer resources) have avoided conventional MPC altogether.
Certainly, the leading MPC suppliers are working diligently to make their solutions easier to implement, use, and maintain. In the past, many have also been more than willing to supplement their clients’ internal engineering staffs with expert services to build and maintain the models and implement the software. But, as previously noted, that type of specialized expertise is becoming an increasingly scarce commodity across industry.
As we learned, APC Performance believes it has a solution to these problems; one that is designed to take advantage of the knowledge, skill, and expertise of in-plant operations and engineering staffs. The argument here is that the plant operators and process engineers are already very familiar with process dynamics, how to manage constraints, and identify potential optimization opportunities; making large detailed model matrices and embedded optimizers largely superfluous.
Small-matrix Multivariable Control
Conventional MPC solutions are based around models and matrices. While APC Performance eliminates the use of detailed models, it maintains the matrix concept for multivariable control, albeit at a smaller scale. According to the company, the matrices for conventional multivariable MPC are over-designed to cover all possible permutations. This leads to large, compute-intensive matrices on the order of 50 x 50, often with hundreds of models, with commensurate reliability, support, and operating burdens.
APC Performance’s approach, in contrast, focuses on key variables that are already used routinely to manage constraints and improve performance. This results in much smaller and more manageable matrices on the order of 10 x 10 or less. The company believes that this translates into more reliable and effective APC applications at the DCS level, avoiding the need for separate computers and leveraging in-house control engineering resources.
“Operational” Performance Criteria
Returning to Mr. Kern’s white paper: Virtually every aspect of modern process control technology is rooted in the concept of models. But it turns out that control performance is one area where industry does not want a model-based solution. Industry wants operational performance. In a nutshell, that means having preset process ‘speed limits;’ approaching targets and constraints in a stable first-order manner; avoiding overshoot and oscillation; and taking extra precautions where appropriate to preserve and assure process stability at all times. This is quite a different statement - and often directly conflicts – with traditional error-minimization control performance criteria, which is based on process models.”
APC Performance currently offers both single-loop and multivariable control solutions. Rate Predictive Control (RPC) is a model-less, inherently adaptive alternative to conventional single-loop PID control. Model-less Multivariable Control (XMC) uses RPC as its internal control mechanism, along with additional innovations. These include a “directional move solver” to help solve the multivariable constraint control and optimization problem without the use of models. The company has trademarked both brands and earned US patents for RPC.
According to Mr. Kern, “The patents are very gratifying since there are hundreds of patents for auto- and self-tuning control systems, but this is the only patent for an inherently adaptive, or naturally self-tuning controller.”
RPC is designed to provide “operational” control performance. This is achieved by using preset move rates, which are like process “speed limits.” As Mr. Kern explains, “Just as drivers know appropriate speed limits, operators know appropriate move rates. Moreover, appropriate speeds are not based on how far you’ve got to go or when you’d like to get there – that’s error minimization – but on traveling safely along the way.” Having adopted the concept of preset move rates, APC Performance proceeded to develop a novel method to taper the preset moves predictively.
RPC Single-variable Model-less APC
RPC, or “Rate Predictive Control,” is APC Performance’s single-variable APC solution, a potential alternative to traditional panel-mounted or DCS-based PID controllers. According to the company, RPC is adaptive to changes in process gain and the preset move size, and deals well with non-ideal process behavior, such as deadtime.
RPC is inherently adaptive in the sense that the method RPC employs to taper its preset control action is based on the actual real-time process response, rather than on a prior expectation (model) of process response. For example, if the process gain increases, the process response will increase, and RPC will taper correspondingly sooner. In the same manner, RPC is inherently adaptive to changes in the preset move rate, so that move rate can be adjusted for operational performance, without undermining control performance.
In addition to move rate, the RPC algorithm uses a “prediction time” parameter that ideally matches process response time. To some extent, this constitutes a model. But Mr. Kern points out that RPC is relatively insensitive to actual process response time and that prediction time serves as both a tuning parameter and modeling parameter, so does not necessarily have to reflect actual process response time. A third RPC parameter, control band, is set intuitively, like move rate, based on where the operators would begin to taper the moves to manage overshoot and settle on target.
RPC’s simplicity, adaptive qualities, and operational performance make it a potential alternative to industry-standard PID for many basic process control applications.
XMC Multivariable Model-less APC
XMC model-less multivariable advanced process control builds on the proven-in-use RPC model-less approach. According to the company, it can be implemented and maintained by in-plant personnel, without having to rely on external experts.
XMC’s directional move solver utilizes “gain direction” only (a concept analogous to single-loop direct/reverse control action), plus constraints and targets to determine the necessary moves, without the need for detailed models. According to Mr. Kern, XMC can be thought of as automating the traditional manual methods of multivariable process operation employed before computers came along.
Proven in Use
When asked about actual use cases, Mr. Kern explained that the applications and products have been in use since 2015. These include an implementation at one large US refinery where RPC has been running successfully for more than two years. The solution is now also up and running full-time at a second large refinery in the US Gulf Coast, with many other sites expressing interest.
APC Performance developed actual products – RPC and XMC – on industry-standard DCS platforms, collaborating with clients to carry out successful proof-of-concept applications. Going forward, APC Performance sees RPC and XMC as fundamental process control building blocks (like PID) that can serve as built-in function blocks within industry-standard control systems. The company’s technology and market development are now also focusing on control system manufacturers and open system function blocks (such as IEC 61131), in addition to direct end user applications.
Conclusion
Clearly, traditional MPC has been helping many refineries, chemical plants, power generating plants, and other process plants around the world improve their economic performance for several decades now, and will continue to serve an important role into the foreseeable future.
However, it’s equally clear that traditional MPC is not appropriate for all plants and applications, and industry is increasingly open to new “APC 2.0” concepts and innovative solutions such as RPC, XMC, and others.
ARC recommends that industrial plants that have been searching for less expensive and resource-intensive solutions for improving operational performance should consider these types of alternative solutions. What’s more, with the current challenge in the marketplace for suppliers to differentiate their panel-mount controllers and/or DCSs, it would also appear that there is an opportunity here for suppliers to embed some differentiating technology into their offerings.
ARC Advisory Group clients can view the complete report at ARC Client Portal on Office 365 or Box.com or New Client Portal on this website
If you would like to buy this report or obtain information about how to become a client, please Contact Us
Keywords: Model Predictive Control (MPC), Advanced Process Control (APC), Model-less, Small Matrix, Adaptive, RPC, XMC, APC Performance, ARC Advisory Group.