
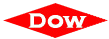




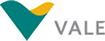

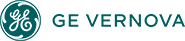




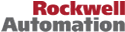

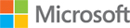
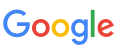

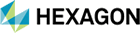


Disruption in power supply can result in huge losses for companies, hence reliable power networks are vital for continuous operations. Asset maintenance can play a key role in avoiding such breakdowns and moreover, predicting component failure would yield huge benefits in terms of cost and time. For instance, contactor is one of the most important electromechanical components, which is used widely for many applications in large electrical networks. It has a broad range of applications in switching and safe operation of electrical circuits. LTTS developed predictive maintenance program for switchgears manufactured by a major European electrical equipment company.
Background and Challenges: The client supplied large switchgears for power distribution lines, and sudden, unexpected breakdowns of these equipment was proving to be extremely costly. Such breakdowns led to the shutdown of an entire power line, causing disruption to thousands of households and offices. Damage to even a small component in a switchgear requires the entire system to be replaced. This resulted in escalating warranty costs. Additionally, service level agreements (SLAs) between switchgear manufacturers and grid owners stipulate penalties for downtime exceeding a certain threshold. This caused additional cost burden on the client. Also, routine field trips by the client’s service technicians to inspect the equipment was time consuming, expensive, and led to routine shutdowns of the grid.
The Solution: To avoid such failures and shutdowns, LTTS designed, built and implemented a predictive analytics program. This helped to automate health monitoring of switchgears and anticipate problems long before they occurred. This algorithm uses historic and real-time data to accurately predict product life. LTTS developed advanced analytics as illustrated below:
Quantifiable Benefits: LTTS predictive maintenance program delivered the following benefits to the client:
Keywords: Predictive Maintenance, Predictive Analytics, Switchgears, LTTS, Power Supply, ARC Advisory Group.