
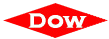




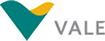

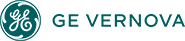




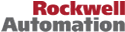

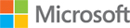
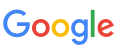

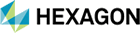


After years of discussion and debate about the merits of concepts like IIoT and Industrie 4.0, in the last two years our industry has witnessed the move from theory to practice. Automation suppliers now offer everything from gateways that IIoT-enable legacy devices, to full-blown IIoT platforms that provide the underpinnings for hardware and software connectivity. And yet, if the 1,749 exhibitors at this week’s Drinktec trade fair in Munich, Germany are a reliable indicator, there is still a disconnect between the promise of an IT-driven future in manufacturing and the acceptance among users of these new technologies.
Held every four years, Drinktec is THE place to meet for bottling and packaging machine builders, as well as for makers of food & beverage processing equipment. This is the show where large OEMs rent whole halls to set up complete filling and packaging lines. This is a hands-on show where automation suppliers take a back seat. And this is the show where end users large and small come to inspect the technology they plan to invest in over the next decade.
And yet, in terms of future-looking concepts like digitalization, this week’s Drinktec was rather sobering. Marketing messages about new technologies as differentiators were lacking, at least in terms of how they relate to concepts like IIoT and Industrie 4.0. With some exceptions, few machine builders exhibiting were concerned with painting a vision of the future around fully digitalized processes, taking advantage of machine-level analytics, or creating digital twins of products to reduce design time and optimize manufacturing processes. Instead, machine builders shared mostly the same marketing messages as in previous years focused on the specific technology advantages they offer, whether it be new packaging designs, more compact machinery, scalable line solutions, or new non-intrusive quality assurance methods.
While larger machine builders demonstrated the benefits of using more information technologies in plant architectures, this focus was mostly inward-looking: more efficient raw materials tracking, integrating machines and lines in MES, and providing a seamless link to enterprise software. No machine builder demonstrated new IT-enabled analytics capabilities or showed how machine learning can improve operations and maintenance.
There were exceptions. KHS, a supplier of complete bottling and packaging lines, presented its “Technology 4.0” initiative, which promises customer benefits from digitalization, such as “…realize more economical and more reliable processes”, but was vague about its implementation. KHS is said to be deploying its own app to remotely monitor machines worldwide, developed on the Siemens Mindsphere platform.
Krones, the market leader in this segment, also presented its digitalization-based concept of the “Factory of the Future”, stating that “only when all business processes along the entire value added chain are digitalized can flexibility, efficiency and results be significantly upgraded”.
Krones also demonstrated how it implements condition monitoring in a variety of machine areas, including monitoring of filling valve, lifting cam rollers, rotary plate control, stretching system drives, as well as leak detection in pressurized systems. Condition monitoring is often the gateway application to adding analytics to new or existing machines, and while Krones has offered this functionality for years, the company just doesn’t market it as being IT-driven or a product of digitalization.
Digitalization has many aspects, some internal and some external. New offerings for third party machine analytics often involve sending machine data to an external third party in the cloud. However, many machine builders say the risk of exposing their systems and data to the outside world is too high. Even after six years, the spectre of Stuxnet and cyber security still spooks the industry. On top of that, many machine builders view IIoT platforms like Mindsphere from Siemens and Predix from GE as a threat to future after-sales revenue streams. That’s why some companies like Trumpf in Germany have launched their own platforms both to control development and to secure future remote monitoring and maintenance contracts for themselves.
Automation suppliers, not known for their modesty at shows like the Hanover Fair, play a smaller role at machine shows like Drinktec, but top suppliers like ABB, Siemens, B&R and Beckhoff exhibited this year. Siemens led the pack, presenting its vision of the benefits of digitalization in the food & beverage industry, while celebrating the 40th anniversary of its BRAUMAT supervisory software for breweries.
So maybe there is more digitalization happening in the machine building industry that meets the eye. Machine builders are arch-conservative, and for good reasons. Their machines have long product lifecycles, so they are loath to experiment with new or risky technologies, unless their customers demand it. For machine builders, maybe it’s not a question of jumping on the digitalization bandwagon, but rather addressing specific customer demands with highly application-specific features and capabilities than may or may not be “IT-driven”. Digitalization is driving machine and product design, but a lot of it is happening behind the curtain. And that, precisely, is the disconnect.