February 6-9, 2023 - Orlando, Florida
Executive Keynotes Highlight Sustainability, Digital Transformation, and Security
Digital transformation, sustainability, and cybersecurity were the major themes at the 27th annual ARC Advisory Group Industry Forum. With approximately 900 attendees, the Forum featured dozens of end user case studies and presentations, many workshops, panel discussion sessions and networking opportunities.
A key takeaway from the week is that while the COVID pandemic was a sufficient impetus for many end users to begin their journeys into digital transformation, the impact of increasing sustainability and ESG-related business requirements are providing end users with even more of an incentive to pursue these programs. Many end users, however, have embarked on digital transformation projects only to find that they lose momentum for a variety of reasons, but most often due to inability to scale.
Forging a Successful Digitalization Strategy
Tuesday’s keynote sessions focused on the advancement of digitalization strategies and some of the issues surrounding recent lack of momentum in digitalization projects. Allen Pertuit, vice president of downstream projects at Shell, discussed Shell’s transformation from a conventional integrated oil and gas company to a diversified energy company. Gabriel Gonzalez-Alonso, senior vice president and head of corporate development at ZF Group, spoke about his company’s journey to sustainability through digital transformation and renewable energy. ZF Group is an integrated mobility company that offers solutions for autonomous driving, integrated vehicle safety, and electric mobility.
Greg Gorbach, vice president of digitization and IoT at ARC Advisory Group, discussed some of the growing pains around digital transformation, why digital transformation (DT) projects stall or fail, and some strategies for making DT projects transition into long-term successes. A recent ARC survey shows, for example, that only 35 percent of survey respondents were either well underway with their digital transformation programs or have reached the point where they have gone beyond simple integration and are now deriving real time insights to drive optimization into manufacturing processes and workflows that deliver tangible business results.
Executives Share Views on Successful Digital Transformation
The Tuesday morning executive panel discussion included the presenters as well as Axel Lorenz, CEO of Process Automation at Siemens, Antonio Pietri, president and CEO of AspenTech, and Colin Masson, global industry marketing director Microsoft Cloud for Manufacturing. The discussion followed a range of DT topics, from digital twins to justifying the cost of digital transformation projects.
The panel discussed how end users need to convince top management to take the budget for long-term digital transformation projects out of the normal budget of the company, which is often subject to short-term capital expenditure cost management and other cost containment factors. Successful digital transformation projects can also benefit from special financing.
The Role of Sustainability in Digital Transformation
The role of sustainability was also discussed in the context of digital transformation strategies. Many companies are implementing both sustainability and digital transformation initiatives at the same time. Shell, for example, has an initiative called the Sky Scenario, which outlines a technological path to achieving the emissions and climate goals outlined in the Paris Agreement.
Although many end users are looking at their own supply chains and making effort to decarbonize them, the automation suppliers are also doing the same within their own operational ecosystems. Axel Lorenz pointed out that Siemens is reducing the carbon footprint of its own supply chain. For example, Siemens has redesigned its DCS controllers to reduce the carbon footprint of production.
Antonio Pietri of AspenTech stated that while customers have not always been concerned with optimizing for emission reduction, this is now changing. Customers are now looking to model things like hydrogen production, storage, and transportation. Aspen is also finding growth in sustainability-related digital applications like doing molecular analysis of oils and biodiesel fuels. Colin Masson pointed out that Microsoft is undertaking efforts within its data centers to make it easier for its customers to model carbon impact, as well as implementing a program to recycle used hardware components in data centers.
Speed of Adoption, Company Size, and Worker Skills
All panelists echoed that speed of transformation need not be fast, though it needs to be consistent. Companies should walk before they learn to run. It may not be feasible for companies to move as quickly as some investors may want you to. The end users on the panel also stated that the size of your company should not be a barrier to digital transformation adoption. Small and medium- sized companies can benefit from digital transformation as much as larger companies. The shift to new technologies will require a whole new set of workers with a new set of skills that we don’t have today.
Overcoming Sustainability and ESG Challenges
Wednesday’s executive keynote sessions were more focused on sustainability issues. ARC’s Mike Guilfoyle kicked off the session with a discussion of new sustainability initiatives at ARC, including the formation of a new Energy Transition and Industrial Sustainability (ETIS) team. Market pressures around sustainability metrics are increasing. More aggressive policies, laws, and regulations are being enacted around the world, with more than 100 countries adopting policies on sustainable consumption and production. At the moment, the greatest challenge for industrial companies is that their desire to change is greater than their capacity to do so.
The current environment is making it more challenging to implement effective sustainability and ESG (environmental, social, and corporate governance) initiatives. Scope 3 emissions, or emissions in the value chain that aren’t directly controlled by the reporting organization, remain the biggest focus for emissions reduction and present the biggest challenge to manufacturing and critical infrastructure end users.
Rapid growth in electrification, driven by innovation such as adoption of EVs, is also greatly increasing demand for electric power. By 2050, electricity demand is expected to triple, with almost all growth coming from decarbonization innovation that will exceed today’s total energy investment.
Sean Bushart, senior fellow at the World Economic Forum (WEF), gave a presentation on the WEF program, in collaboration with Accenture and the Electric Power Research Institute (EPRI), that develops industrial clusters in different regions of the world that are rapidly transitioning to net zero emissions. These clusters are geographic regions with high concentrations of traditionally carbon emitting manufacturing applications. Two examples given were HyNet Industrial Cluster in the UK near Liverpool and the Houston H2 Hub. A total of 17 of these Net Zero clusters were started at COP26 and development of these clusters is accelerating globally, with the aim of growing the number to 100 within three years. The clusters communicate with each other on progress, and share lessons learned.
HyNet includes manufacturing, steel, chemicals, cement, and shipping. They are looking to see how they can transform themselves by investing in common infrastructure to lower carbon footprint and advanced decarbonization. HyNet includes pipelines for CO2 removal, taking it offshore to disposal facilities. HyNet also includes a large natural gas infrastructure, and they are also introducing hydrogen into the cluster.
Sustainability as a Business Driver for Success
Kelly Lopez, executive vice president of enterprise services at Scout Sourcing, discussed how sustainability today is really a business metric, and how the future success of manufacturers depends on their ability to implement successful sustainability strategies. Lopez cited those changes in regulation both in EU’s Corporate Sustainability Reporting Directive and US SEC legislation driving public disclosure. According to Lopez, 85 percent of investors now consider ESG metrics as part of financial health/risk mitigation.
Sustainability Executive Panel Discussion
In addition to Mike Guilfoyle and Kelly Lopez, the Wednesday executive panel discussion on sustainability included Lizabeth Stuck, vice president of workforce development at MxD (The Digital Manufacturing Institute) and Steven Pullins, senior vice president and chief technology officer at AlphaStruxure, an energy-as-a-service provider. Key topics discussed included the competencies that need to be developed for sustainability. These include a deep understanding of scope 1, 2, and 3 emissions, how to financially model sustainability initiatives, and more.
Leading industrial companies are actively engaged in transformation programs that will reshape their production operations to be more integrated, responsive, and optimized to meet business and customer needs. Realizing these innovations requires an understanding of the emerging 21st century operations ecosystem and how it interacts with business, engineering, supply chain, and other organizations. Today's connected environments surface machine data that was heretofore unavailable, and so enable new business models. New systems may monitor the assets, and new actors may interact with the assets in new ways. Industrial plant operations, typically siloed and fairly isolated today, will be reshaped as the core of a 21st century industrial production operations ecosystem. A similar evolution is taking place for field operations - such as mining or agriculture. In other cases, such as automotive, where the assets operate in public spaces and both the assets and ecosystems are evolving quickly, other factors come into play.
In 21st century production operations, work is accomplished with a combination of internal and external actors (such as asset manufacturers, 3rd party machine monitoring services, spare parts suppliers, etc.), putting new demands on data requirements and cybersecurity strategies. New types of production systems (such as additive manufactuiring) and new types of data are being generated (from wearables, vision systems, machine health sensors, etc.). And digital twins and machine learning systems can work at various levels to optimize the overall system in synchrony with the needs of customers and business operations.
An important enabler for this innovation in industrial companies is the convergence of IT (Information Technology at the enterprise level), OT (Operations Technology, the information and automation technologies employed in the plant), and ET (Engineering Technology, the newer technologies that create virtual models). IT/OT/ET convergence is among the drivers of the digital transformation that leading companies are embarking upon. A wide range of technologies, such as Ethernet/Wi-Fi, virtualization, cloud, SaaS, analytics, Big Data, mobile, social, modeling, augmented reality, machine learning, remote monitoring, and digital twin are now being employed in industrial operations to improve operating performance, create a virtual environment, or introduce the Industrial Internet of Things. But the big payoff comes when companies begin to operate in new, collaborative ways across the whole of the enterprise.
This program features speakers talking about moving to 21st century operating models, and how they utilized the IT/OT/ET enablers of digitization and innovation to improve performance in their production operations and throughout their organizations.
Most industrial companies still tend to make decisions based on habitual ways of doing things, tribal knowledge, rules-of-thumb, and the opinions of in-house experts. But leading companies are moving to an information-driven culture and business model in which all decisions are made based on analysis of operations and business process data. Throughout the organization, these companies employ software to collect, contextualize, visualize, and analyze data to gain new insights. The common question is, “What does the data tell us?” Armed with new insights, organizations can anticipate changes and drive better business results.
It is clear that the use of analytics in industrial companies is growing rapidly. With the industrial space becoming much more dynamic, manufacturers are turning to advanced analytics and machine learning to support predictive and prescriptive solutions. More companies are pursuing analytics solutions and more employees throughout the enterprise want more and better decision tools. And the increasing focus on Smart Manufacturing, Industrie 4.0 (I4.0), and Industrial Internet of Things (IIoT) is driving demand for predictive maintenance and operating performance improvement solutions, which rely on advanced analytics.
This program will:
- Cut through the confusion surrounding 'analytics' in the industrial space
- Provide a useful conceptual framework for differentiating modern analytics platforms from previous approaches
- Highlight new technologies, platforms, architectures, and processes
- Present case studies and examples from early adopters of new analytics systems
- Provide industrial companies the information they need to begin their own analytics journey
Asset Performance Management incorporates Industrial IoT (IIoT) and new analytics solutions like machine learning. It uses information from production management, control systems, and asset management applications to provide new opportunities to optimize asset availability and operational performance. This optimization goes beyond functional silos and occurs between silos where significant inefficiency, waste, and sometimes dysfunction often reside.
Balancing the objectives of operations for on-time delivery, volume, and quality with those of maintenance for asset availability, longevity, and reliability requires sharing information and harmonizing these objectives with the goals of the enterprise. New information technologies provide functionality to intensify cross-functional collaboration, business process improvements, and higher levels of performance to achieve asset performance management excellence.
The ability to interact with equipment – like a variety of devices on a single site, or widely dispersed machines – presents new opportunities for industrial companies, utilities, and equipment suppliers. These networks provide a new “connected ecosystem” of equipment manufacturers, systems integrators, and end users. Some manufacturers and utilities have begun adopting these technologies.
Those attending this Asset Performance Management program will learn what was successful, and gain insights into what is next. The objective is to make fact-based decisions using reliable information that aligns with the organization’s objectives. An APM strategy helps ensure the best possible returns on capital investments over the lifecycle of the asset. If you are involved in operations, maintenance, or industrial IT, you will want to attend these program sessions.
We have entered a period of intense innovation in industrial automation. In the areas of high value-added manufacturing there is growing global competition. Countries with developed economies want to maintain and grow their existing competitive advantages and support their exporting industries. Countries with developing economies want to improve their competitiveness as well.
This competition is, in part, taking the form of national initiatives to improve manufacturing competitiveness. These initiatives are found in Germany, the US, Japan, Korea, and China. In the US the Industrial Internet Consortium has formed. Platform Industrie 4.0 is the German initiative; the “4.0” referring to a 4th industrial revolution (following steam, mass production, and IT). This can be thought of as a set of new technologies that are fusing the physical, digital, and biological worlds, and impacting all disciplines, economies and industries.
Some of the topics that will be covered in the sessions for this program include:
Devices that will use the future 2‐wire Ethernet standard now in development by the IEEE 802.3cg committee. This 2019 standard will enable high speed communication to process field devices over distances as long as 1 kM.
The Open Process Automation Forum: The Latest Update
The Open Group’s Open Process Automation Forum is noteworthy for several reasons. First, because of its genesis within ExxonMobil, a leading international oil company with a long reputation for operational excellence. Second, because the products of this program will be technologically quite different from the process automation systems used today. Third, because the value chain envisioned for this program is also quite different from the way the process automation market works today. The latest developments in this initiative will be presented and discussed.
Industrial Automation and the Industrie 4.0/Industrial Internet Initiatives
What will be the impact on manufacturing and automation of these major national initiatives? How will the process industries, discrete manufacturers, and automation suppliers adapt and change their products in response to these programs? What are thought leaders in Europe and North America doing now and planning for the next few years? End users will present the current programs for rapid integration of skid-mounted process systems, based on the Module Type Package (MTP) initiative of the NAMUR group in Europe. Also, European end users will discuss their pilot work with the future 2‐wire “single pair Ethernet” standard now in development by the IEEE 802.3cg committee. This 2019 standard will enable high speed communication to process field devices over distances as long as 1 kM.
New business processes are driving higher performance and lower costs across the industrial landscape. Companies are leveraging new developments in cloud computing, AI, IoT, edge solutions, and digital twins to identify bottlenecks and opportunities for improvement. Technological developments are likewise driving improvements in the safety and reliability of critical operations. Benefits from these developments can be large, but they can be quickly erased unless companies also address the increased risks of serious, costly cyber incidents.
Industrial cybersecurity has never been more important. New business processes and technologies are rapidly expanding the pathways for attackers to steal information and disrupt operations. At the same time, industrial security teams are struggling to deal with ransomware and sophisticated nation-state attacks. This situation is jeopardizing worker safety, delivery of critical services, and the operational continuity of plants and facilities that fuel profitability.
Conventional industrial IT and OT security programs weren’t designed to handle all of these new challenges. Digitalized organizations need security strategies that monitor, control, and coordinate security across every corporate device, application, system, and network regardless of where it is located. Security programs also need to ensure consistent management across IT, ET, OT, Cloud, Mobile and IoT environments. Likewise, security needs to span every business process and worker regardless of where, when, and how they are performed. Developing a comprehensive cybersecurity strategy that addresses the current and emerging risks of digitalization has never been more urgent.
The Industrial Cybersecurity program at the 2023 ARC Industry Form Americas addresses these issues with informative workshops, panel discussions, and case study presentations. It is the ideal venue to learn what others are doing, how they are doing it, and the benefits they are achieving. Attendees will also have opportunities to discuss their unique challenges with peers, researchers, educators, service providers, and solution providers.
Autonomy and intelligence embedded pervasively in automation equipment is one of the key attributes to realization of connected smart machinery. Connected smart machinery is important in virtually every application imaginable, but is even more valuable in cases where there is limited communications. Machinery that analyzes and compresses large data sets are essential to ensuring that the data traffic on the Internet does not overwhelm the system or data can be analyzed local to the device. The connected smart machine will require not just more sensors, but also more intelligent sensors. Sensors must perform more sophisticated signal processing “at the edge” to provide accurate signals that filter out the noise before it gets to the automation system.
In this program, machine builders employing intelligent sensors into the machinery to perform complex condition monitoring algorithms into automation systems will be highlighted. Key topics for discussion include:
- Creating new maintenance service revenue streams for machine builders
- Development of equipment protection algorithms that increase resilience of machinery to stay operational for much longer periods of time.
- Adaptive control algorithms allowing systems to operate over a wider range.
- Predictive condition monitoring systems that use real-time control algorithms to provide a new level of maintenance information.
- Exploring the potential of the Industrial Internet of Things (IIoT) to combine the benefits of multivariate analysis, predictive modeling, and inferential information to preempt abnormal situations.
The digital transformation of industry, infrastructure, and cities is under way, with new business processes, services, and models being pursued. This energy and investment is a rational response by organizations to digital economies that present new and very real opportunities. When combined appropriately, data and technology can provide competitive advantage, that – in some cases – enables organizations to leapfrog their peers.
Yet, when planning or executing this transformation, what is often missing is a focus on the human element of digital transformation. Where do people fit in? The changes that digital transformation will have on the workforce are likely to be the most far-reaching and sustained effects. Not only will digital transformation change the number of people needed to do work, it will rewrite how that work gets. Those going through digital transformation quickly realize that managing the human element can be the most difficult aspect. However, as they work through their journey, people begin to better understand the human-centric benefits of digital transformation. Enabled by technology, the workforce will become more empowered to identify challenges, adapt to circumstances, and find new ways to solve problems.
This program will:
- Discuss digital transformation through the lens of people, examining the changes in the workforce as organizations become increasingly data-enabled and service-based.
- Identify the common human-centered challenges to successful digital transformation.
- Provide a framework for creating an organizational strategy and culture for digital change
- Present case studies of how companies organized people and work cultures around digital-first thinking
- Outline how to evolve customer relationships and engagement for a digital world
Energy transition and sustainability are now being woven into the core business strategies of industrial companies, who now have the mandate and opportunity to tackle environmental and social challenges. What are the market drivers behind the dramatic uptick in board-level attention - and the ensuing formalization and execution - of environmental, social, and governance (ESG) strategies? How are companies tackling decarbonization, new tracking requirements, and the many, complex threads associated with the energy transition and improved environmental stewardship? How are these efforts being balanced with demands for financial performance and ongoing digital transformation?
Companies who are more advanced in their digital journeys are already integrating sustainability and energy transition initiatives, together with competitive excellence, resilience and agility, and workforce goals, into a comprehensive strategy driving towards becoming a focused, integrated, digital organization. Powered by transformative technologies, innovative processes, and data, they are creating smart integrated systems that can develop new insights and, in some cases, even automate decision making, while optimizing to corporate performance goals and improving competitive excellence. These new systems can also support improved cybersecurity, helping industrial companies protect against a significant and growing risk.
Industrial Internet platforms are emerging as pivotal, value-added components of the Industrial Internet of Things (IIoT) architecture. These platforms add incremental value by functioning not only as the glue linking connected industrial devices to higher level performance-enhancing applications, but also as the execution environment for the applications themselves.
Industrial Internet platforms play an integral role in analytics, big data, remote asset monitoring, performance management, decision support, universal visualization, and the value chains for connected products and products-as-a-service. The ability of these applications to access, analyze, and process industrial data is central to the IIoT value proposition.
Industrial Internet platforms architecturally reside between intelligent devices and higher levels of the enterprise architecture. Device connectivity platforms monitor, collect, process, and transmit data from a variety of intelligent sensors, devices, machines, products, and other assets to higher levels of the architecture, while analytics, big data, machine learning, and numerous other applications that deliver incremental process improvements typically reside in enterprise-level platforms.
The IoT network edge has emerged as a primary vehicle for delivering incremental business value via internet-enabled business strategies such as the Industrial Internet of Things (IIoT), Industrie 4.0 (I4.0), and Smart Cities and Infrastructure.
Escalating demands to feed information from data-rich intelligent edge devices to the cloud is one of the most pressing issues facing OT and IT professionals in the era of internet-enabled business strategies. Standard options include support of common API or protocols, but cloud-based agents themselves are migrating into network edge devices. These agents are increasingly viewed as not only vehicles for closer edge-to-cloud integration, but also as platforms for edge computing applications that execute locally, offloading processing from the cloud and providing enhanced security and closer to real time performance.
This program will highlight current and prospective demands on both network edge infrastructure, such as gateways, routers, and switches, as well as smart end devices that function as edge nodes in the IoT architecture. In addition, this program will look at the central role of Industrial Internet platforms in the emerging Industrial Internet of Things and how to use them to achieve incremental business benefit.
Agenda at a Glance
Sunday, February 5
Casino Night Reception, 6-9 PM
Monday, February 6
8:30 AM | Workshop Sessions |
10:00 AM | Break |
10:30 AM | Workshop Sessions |
2:00 PM | Workshop Sessions |
3:30 PM | Break |
4:00 PM | Workshop Sessions |
6:00 PM | Welcome Reception |
Tuesday, February 7
8:30 AM | Keynote Presentations |
10:00 AM | Break |
10:30 AM | Executive Panel |
12:00 PM | Lunch |
2:00 PM | Concurrent Track Sessions |
3:30 PM | Break |
4:00 PM | Concurrent Track Sessions |
5:30 PM | Evening Receptions |
Wednesday, February 8
8:30 AM | Keynote and Executive Panel |
10:00 AM | Break |
10:30 AM | Concurrent Track Sessions |
12:00 PM | Lunch |
2:00 PM | Concurrent Track Sessions |
3:30 PM | Break |
4:00 PM | Concurrent Track Sessions |
6:30 PM | SeaWorld Reception |
Thursday, February 9
8:30 AM | Concurrent Track Sessions |
10:00 AM | Break |
10:30 AM | Concurrent Track Sessions |
12:00 PM | Forum Ends |
Featured Speakers
The following executives are featured speakers at the Forum.
Allen Pertuit
Vice President, Downstream Projects
Shell
Allen has over 34 years of experience including assignments in Shell’s Upstream, Downstream and Projects & Technology divisions. He has held various senior leadership positions, managing engineering, downstream assets, upstream assets, and major capital projects. In his career at Shell, Allen has worked and lived in several geographical locations including Asia, Europe, and the United States. He considers it a privilege to have worked in such diverse cultural environments and leverages this experience in driving the success of Shell’s Powering Progress Strategy. In his current role of VP Downstream Projects, Allen has accountability for the development and delivery of Shell’s conventional downstream chemicals major projects as well as projects in the Low Carbon & Renewable Fuels, Sustainable Chemicals, CCS and Hydrogen Businesses.
Gabriel Gonzalez-Alonso
SVP, Head of Corporate Production Management
ZF Group
Gabriel is in charge of Industry 4.0, industrial performance management, performance analytics and industrial strategy as well as advanced manufacturing engineering. He has 28 years of manufacturing experience, 25 of which was with Renault-Nissan Alliance. Gabriel went from a supervisor at a body shop and head of a paint shop to Automobile and Powertrain Plant Manager, with a high focus on lean manufacturing. In mid-2012, he took the role of Regional Industrial Director in South America for Renault-Nissan with responsibilities in production as well as supply chain management and process engineering. He then moved to Corporate taking the Head of Manufacturing Quality position for 3 years with intensive work with teams from both companies - Renault and Nissan - on different aspects as Suppliers Quality, Build in Quality, and Shipping Quality as well for Assembly Plants as Powertrain. He was Head of Industrial Performance since 2017 during 3 more years for Renault Group in close contact and developing similar working methods with Nissan on strategic Lean approaches to make one of the most competitive brands in the world from a manufacturing point of view.
Sean Bushart
World Economic Forum Project Fellow
Electric Power Research Institute
Sean is working to develop and execute a global initiative for accelerating the transition of industrial clusters to net zero. He is the North American lead for the initiative, which has a broad team of experts from EPRI, the Forum and Accenture focused on decarbonization technology deployment, financing, policy, and partnerships. Sean’s previous role was Director of the Environmental Sciences and Technology Team in EPRI’s Generation Sector. He led multi-disciplinary R&D teams working to address air, water, land, and chemistry challenges and opportunities related to industry decarbonization, electrification, and operational performance objectives. He has also led broad based research initiatives covering a range of topics including water availability, radiation safety, waste management, plant chemistry, plant decommissioning and groundwater protection.
Jim Haw
Vice President, Program Management & Digital Strategy
PureCycle Technologies
Jim is responsible for all worldwide project/program execution, as well as PureCycle’s Born Digital program. He has over 33 years of experience in the industrial manufacturing sector in industrial automation/electrical engineering, capital project/program management, as well as PMO development. Jim holds a Bachelor of Science degree in Electrical Engineering from the University of Arkansas at Fayetteville and is a registered Professional Engineer in the state of Texas. He has been a career leader of the International Society of Automation having served at the local, regional, and national levels. He is also a Certified Maintenance and Reliability Professional as well as a Certified Project Management Professional.
Axel Lorenz
CEO, Process Automation
Siemens
Axel has been CEO of Process Automation at Siemens in Karlsruhe since October 2022. The graduate engineer was previously Vice President of Control at Factory Automation, which included responsibility for the Simatic PLC, as well as Sales Manager of the Process Automation Business Unit. Prior to this, he held various roles, including General Manager of the Automation & Engineering Business Segment responsible for process control systems for several years. Axel started his professional career in 1992 as an Engineer for Process Control at Siemens in Berlin. Axel is driven by leveraging digital transformation to create real value for the company’s customers and ensuring their competitiveness – making the most of resources and bridging progress and sustainability.
Antonio Pietri
President and CEO
AspenTech
Antonio serves on AspenTech’s Board of Directors. Prior to his appointment to President and CEO, he served as Executive Vice President, Worldwide Field Operations, where he led global Sales, Sales Operations, Professional Services, and Customer Support & Training. He previously served as Senior Vice President and Managing Director, Regional Operations, Asia Pacific, based in Singapore and Beijing, China. Antonio joined AspenTech through the company’s acquisition of Setpoint, Inc. in 1996. At Setpoint, he held a range of sales, services implementation, and consulting roles, where he oversaw integration of AspenTech solutions at European refinery and process manufacturing sites. In 2002, he relocated to Singapore as Vice President, Business Consulting, and was subsequently promoted to Managing Director of the Asia Pacific region.
Colin Masson
Global Industry Marketing Director, Microsoft Cloud for Manufacturing
Microsoft
Colin has over 35 years of experience evaluating, implementing, marketing and selling manufacturing, enterprise and supply chain platforms and solutions. Over the last 15 years at Microsoft, Colin has been focused on enabling manufacturers to create a more resilient and sustainable future, enabling 'Digital Transformation', and the 'Servitization' of manufacturing with solutions that leverage Microsoft's intelligent edge and cloud capabilities (Azure, Dynamics 365, Microsoft 365 and Microsoft Power Platform), and co-innovation with the leading partner ecosystem for manufacturing.
Attendee Perspectives
It was an honor and pleasure to be invited to speak at the ARC event. I was impressed with the level of knowledge I was exposed to at this conference; this will become an annual event for me. A sincere thank you to ARC for organizing a "WOW" event.
Marty Martin
Director, Process Control Technology
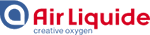
ARC Advisory Group industry events are extremely valuable (to Saudi Aramco). ARC is the barometer for our industry.
Abdullah Al-Khalifah
Senior Engineering Consultant
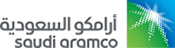
For me, since I’m from the pharma industry, coming to the ARC forum gives me a chance to interact with folks in like roles from different industries. It’s been very valuable for me to bring ideas and new connections back to my company and apply them to our business.
Kevin Fulton
Director of Engineering

It was a high honor for me to participate [at ARC's Forum] on behalf of the City of Orlando!
Charles Ramdatt
Director, Smart Cities and Special Projects
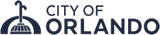
Innovations Showcase
New industry solutions are on display at the Innovations Showcase. The Showcase provides an excellent opportunity for executives to assess the potential for emerging applications in production management, interoperability, virtual manufacturing, process improvement, asset management, operations management, supply chain synchronization, and more. Exhibits have application scenarios for attendees to see how emerging technologies are applied to help solve issues across all industries.
The Showcase is open during the Monday Evening Reception and during breakfasts, breaks, and lunches. It is held adjacent to the forum where refreshments are served.
Location
The Forum is held at the Renaissance Orlando Hotel in Orlando, Florida.
Renaissance Orlando at SeaWorld
6677 Sea Harbor Drive
Orlando, Florida 32821
renaissanceseaworldorlando.com
The Renaissance is just a short shuttle or taxi ride from the most popular Orlando attractions and within easy access of Orlando airports. Hotel amenities include complimentary 24 hour fitness center use; transportation to SeaWorld Orlando, Discovery Cove, Aquatica, and Universal Studios Orlando based on shuttle schedule; and public area wireless Internet.
Previous Attendees
The following companies have attended recent ARC forums:
Adani Power
Aegea Saneamento
Air Liquide
Akzo Nobel
Albensi Group
Alliance Pipeline
AMEC Natural Resources
Analog Devices
Anglo American
Archer Daniels Midland
Artera Services
Avgol
Axiall
Bahrain Petroleum
BHP Billiton
Blackrock
BorgWarner
Bosch Rexroth
Brady
Bracell Celulose e Papel
Capenture
Cambell Soup
Casa da Moeda do Brasil
CBMM
Cenovus Energy
CF Industries
Chevron
Church & Dwight
Colonial Pipeline
Comau
Connacher Oil and Gas
Consumers Energy
Constellation Energy Group
Correios
Corteva Agriscience
CORYS
CSN - Companhia Siderurgica Nacional
Cummins
Danaher
DCM Shiram
Dell
Dominion Energy
DTE Energy
Duke Energy
Eaton
Ecopetrol
Eldorado Brasil Celulose
Elkay Manufacturing
Embraer
Emirates Global Aluminum
Enbridge
Endress+Hauser
EnQuest
Entergy
EQUATE Petrochemical
Ergon Refining
Ero Brasil
FiberVisions
Fidelis New Energy
Flint Hills Resources
Florida Power & Light
Freeport McMoran
GE
Goodrich Petroleum
Goss International
Greater Cincinnati Water Works
Green Bay Packaging
Hemlock Semiconductor
Hill Labs
Hirschmann Automation & Control
IDEXX
Independent Belgian Refinery
Indorama
Inductive Automation
Infosys
Ingersoll Rand
Ingredion
International Paper
Intertape Polymer Group
INVISTA
Iscar Metals
Itafos Conda
JHP Pharmaceuticals
John Deere
Joy Mining Machinery
Kalbe Morinaga Indonesia
Kaneka
Kellogg
Kings Hawaiian
Kollmorgen
Kongsberg
KUKA
L&T Infotech
Lafarge
LD Cellulose
Lilly
Lockheed Martin
Logan Aluminum
Lopez Foods
Lucky Peak Power
LyondellBasell
Magna International
MESA
Middlesex Country Utilities Authority
MillerCoors
Momentive Specialty Chemicals
Morgan Stanley
Mori Seiki
NAMUR
Nexen
Nissan
North West Redwater Partnership
NuScale Power
Oak Ridge National Laboratory
OBE Power
Okuma America
Olympic Scientific Solutions
Orange County Government
Orlando Utilities Commission
Osaka International Refining
Pacific Northwest National Lab
Palmer Foundry
Pan American Energy
Panasonic
Panduit
Paper Converting Machine
Parker Hannifin
Patti Engineering
Penske Logistics
Petro Rabigh
Petrobras
Phoenix Contact
PTC
Public Service Co. of New Mexico
PureCycle Technologies
Quiet Logistics
Rain Manufacturing
Raizen
Red Arrow Logistics
Rolls-Royce
Ryder System
Sabic
Sagar Cements
Sandia National Laboratories
Seattle City Light
Sekuworks
Shell
Smurfit-Stone Container
Solvay Brazil
Sony Electronics
Sonoco Metal Packaging
South Jersey Industries
Spire
SSR Mining
Suburban Renewable Energy
Sun Chemical
Syngenta
Takeda Austria
Tallgrass Energy
Tampa Electric
TetraPak
TOTAL
TotalEnergies
Toyota Motor Manufacturing
Transpetro
Transportadora Associada de Gas
U.S. Corrugated
U.S. Dept. of Energy
Universal Parks & Resorts
Vale
Valero Energy
Vallourec & Mannesmann
VEOLIA
Veracel Cellulose
Walt Disney World
WestRock
Whirlpool
Wipro Technologies
Xerox
Yanbu National Petrochemical
Yaskawa