
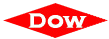




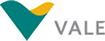

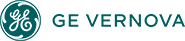




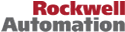

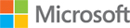
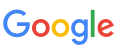

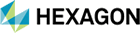


Yokogawa participated as a Platinum Sponsor at ARC Advisory Group’s 21st India Forum titled Driving Sustainability, Energy Transition, and Performance through Digitalization on July 12th and 13th, 2023. The 300+ delegates at the Forum networked extensively and disseminated information about new processes and technologies that are accelerating the digital transformation of industries. In the Forum session on Advanced Automation Enhancing Operational Excellence, Ajoy Kumar, General Manager - Product Sales & Marketing, Yokogawa spoke about wireless Sushi sensors for industrial IoT solutions. His presentation was structured in five distinct sections: need for IIoT sensors in the process industry; Sushi IIoT sensors; key differentiators; connectivity to higher end systems; and use cases. While this blog will capture the key points of Ajoy’s presentation, the entire presentation is available for viewing here.
Explaining the need for IIoT sensors, Ajoy said that earlier experienced operators would go close to or just touch an asset and gauge its condition. However, those days the number of assets in a plant were limited; that’s no longer the case. Today, the plants are huge and the number of assets have multiplied. Industry research reveals that 75 percent of these assets are disconnected and it is humanly impossible to monitor, record, and analyze this data; and that is where IoT enters the picture. The IoT wireless sensor can help monitor, record and take it to the higher system for further analysis and gain meaningful insights. Artificial Intelligence (AI) can be used to analyze changes in data, objectively judging the tendency of equipment degradation, and proposing effective measures. “Basically we are moving from a time-based maintenance to a condition-based maintenance (CBM),” said Ajoy. CBM enables reducing unnecessary replacements and repairs of equipment. Sushi sensors will be the most viable solution to move forward to CBM.
The Sushi IIoT sensors provide simple real-time monitoring to identify the unhealthy asset, improve asset maintenance and complement the existing methodology. Key attributes include:
Automatic data collection
Long distance communication
Data quantification/digitization
Sushi sensors also have the basic AI for indicating/predicting the anomaly in advance (normal/abnormal) and preventing failures. The wireless function, battery, and sensor are integrated in a single body.
Sushi sensors are of three types and measure vibration, gauge pressure, and temperature. These sensors are easy to install, configure and monitor. They are also flexible, and completely run on batteries; it works on LoraWan communication, which has an inbuilt antenna and connects to the Gateway. From here it can go to the cloud environment or to the on-premises environment. The system architecture of a typical Sushi sensor was shown via a diagram.
No repeaters are required
Compact and lightweight
Low power and long-lasting battery
Environmentally robust
All the information gathered through the Sushi sensors can be utilized in a planned manner by connecting to Artificial Intelligence. In this context, Ajoy spoke about the Sushi solution packages (Sushi On-Premises GA10; Sushi Edge CI Server or eRT3) and the 5G vision in IIoT.
Globally, 20,000 Sushi sensors have been installed in 500+ customer sites. Ajoy cited two customer success stories:
Customer 1: Six plants in Thailand, Indonesia and India. With over 800 Sushi sensors connecting about 1,000 devices through a cloud and then using AI for real-time equipment status and health monitoring.
Customer 2: Oil wells in Thailand with no power supply available. The challenge was to install sensors for wellhead pressure monitoring. The Gateway was also solar powered with battery powered Sushi sensors. The data inputs from multiple oil wells were sent to the Sushi Cloud.