
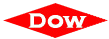




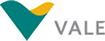

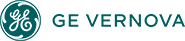




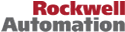

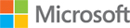
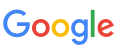

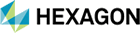


Customer Profile: The North America based manufacturer of electric vehicles wanted to set up a 44,000 square feet warehouse with the space capacity and warehouse design optimized to meet the demand of 5,000 units per annum. This is a greenfield project, and the customer wanted to analyze the layout with material flow options and uninterrupted flow of goods, personnel, and equipment. The customer also wanted CapEx and OpEx to be calculated for budget allocation, and a customized racking design for material replenishment and storage. After careful evaluation, LTTS (L&T Technology Services) was selected to execute the plan and help the customer overcome challenges on multiple fronts.
The Challenges:
LTTS’ Holistic Approach:
LTTS’ master plan of a practical warehouse design helped in arranging the processes in a logical sequence layout that streamlined operations, maximized productivity and efficiency, and optimized expenses. Using its cross-functional team, LTTS provided the detailed warehouse design validated by simulation analysis that helped the customer’s budget planning and implementation.
How it was done
Improved Statistics: LTTS’ strategic layout design accommodated all manufacturing and utility needs within the available space with CapEx of over $1 million and OpEx of up to $1 million. Other benefits include: