
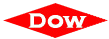




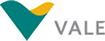

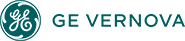




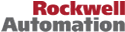

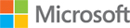
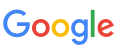

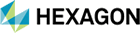


In the years ahead, scientific breakthroughs will lead to new technologies that will help define the new manufacturing with the next generation of products and the associated manufacturing processes. Physics, chemistry, materials science, biology, and mathematical simulation will all come together to enable manufacturers to design and build lighter, stronger, and more adaptable products for consumers, industry, and infrastructure, including both transportation systems and smart cities. Merging areas such as materials science and additive manufacturing will be the game changers for manufacturing in the 21st century.
Beyond just automation and robotics, future manufacturing will involve an interdisciplinary mix of physics, chemistry, biology, and material science. Technologies like generative design will allow product design engineers to create optimal functional parts that can then be produced by advanced additive manufacturing (AM) processes.
New advanced materials designed using simulation at the molecular and quantum levels are being developed to meet specific product requirements for fit, form, and function. This allows today’s engineers to create new materials that fit product requirements, rather than design a product based on available materials. Moreover, with additive manufacturing processes, designers can now create products using materials, shapes, and configurations that would only be possible to produce using additive approaches. Many products are being designed specifically for additive manufacturing.
AM also benefits directly from predictive material science modeling. AM techniques are becoming faster and more precise, yet still limited by the range of materials suitable for “printing.” Material behavior and physical characteristics can be tested in silico to develop new materials tailored for the AM process. 3D models and physics simulations can optimize structures iteratively for printing and use. Recognizing this transformative opportunity for AM and other advanced manufacturing technologies, leading PLM suppliers now offer a portfolio of complementary solutions designed to support end-to-end materials and product design.
The history of civilization is closely interwoven with the discovery and utilization of new materials. From stone to bronze to iron, each discovery catalyzed a significant advance in society, making new tools and technologies cheaper and more available. This is especially true today. New materials are modernizing everything from airplanes to smartphones. This creative churn has launched something of a global industry renaissance in materials science research.
Clearly, today’s consumers demand increasingly better products. Cars must drive farther using less gasoline, medical devices must become smaller and easier to manufacture (thus more affordable), batteries must charge faster and last longer. But there are limits to what existing materials can provide. New technologies like additive manufacturing offer groundbreaking opportunities in product design yet are restricted by the materials they can utilize effectively. Scientists and engineers must be innovative and adopt novel materials and approaches to take on these challenges. To make this quantum leap forward we need a thorough understanding of not only what materials could work, but also why they work. Technologies such as 3D materials modeling and simulation and generative design can move us toward this improved understanding.
Today’s material science researchers are beginning to leverage 3D modeling and simulation to characterize materials properties. By exploring their fundamental physical and chemical interactions down to the subatomic level, they can gain an understanding of the material properties we can see and feel. Each interaction – from the wave functions that govern the movement of individual electrons to the interface stability of a resin and carbon fiber composite – creates the properties we observe by modeling these materials. These models capture snapshots of these systems, helping researchers better understand how materials work in a relatively low-resource environment. Armed with this knowledge, researchers can refine materials to fit the unique requirements of their projects to intelligently design the next generation of advanced materials and products.
New, high-performing substances from exotic alloys to super-strong composites underpin many of the industry-disrupting technologies of the past few years. These advanced materials are also changing and disrupting many traditional manufacturing processes. As a result, companies face mounting pressure to create new, high-performing materials that can help them tackle today’s greatest business and manufacturing challenges. These include developing modern transportation platforms, improved civil infrastructure, “smart” cities, and sustainable consumer products; dealing with harsh environments; and even exploring beyond our planet. Traditional research methods that rely on physical experimentation alone are struggling to keep pace with the shortening product lifecycles required to excel in our 21st century marketplace.
Forward-looking manufacturers and advocates of nanotechnology envision the seamless integration of materials science into product design. Organizations that have adopted this philosophy are advancing breakthrough technologies and new materials with novel applications. We’re already seeing the effects of these technologies across the aerospace, automotive, industrial equipment, specialty chemicals, bulk petrochemicals, high tech, and consumer packaged goods (CPG) industries. For example, aircraft manufacturers like Boeing and Airbus have introduced new airframe structures made almost entirely of carbon fiber composites that are strong, stiff, lightweight, and easy to manufacture.
Likewise, automotive companies are utilizing carbon fiber-reinforced thermoplastics to lighten the body of newer model cars. Precursor components can be heated, combined with resin, and then injected into molds to form the components of the car body. Such techniques offer greater flexibility in body design while maintaining the strength required for passenger safety. Moving beyond traditional manufacturing techniques to additive manufacturing affords even greater flexibility in body design. New and recycled plastics create durable, aesthetically pleasing automobile components while also reducing noise, vibration, and production costs and improving fuel efficiency and sustainability. These and the other opportunities offered by additive manufacturing could significantly restructure the transportation and mobility industry as we know it.
In the same vein, new battery technologies are disrupting multiple industries. Beyond electric vehicles, which have already catalyzed a momentous shift in the automotive industry, consumers are placing increasing demands on personal electronics to keep pace with our increasingly digital world. Batteries must charge faster, last longer between charges, and offer extended lifespans.
As a result, leading producers of consumer electronics are exploring materials that improve upon traditional lithium-ion batteries. We are seeing a range of new compounds and materials including solid-state lithium-ion, graphene polymer cells, laser-produced supercapacitors, fluoride-ion, magnesium-ion, sodium-ion and more that offer higher theoretical capacities and energy densities than their mass-market counterparts. Some of these compounds are prone to shortened lifespans due to decomposition in their electrolyte formulations. To address this issue, researchers are exploring hybrid organic-inorganic gelled electrolyte matrices that can improve electrochemical stability during cycling. All these research approaches demonstrate the promise advanced materials offer.
Increasing demand for more advanced materials drives researchers to explore new areas for inspiration. Unconventional feedstocks, structures based on nature, and 2D materials provide the foundation for technologies such as flexible circuits for wearables, autonomous vehicles, and next-generation aircraft. Researchers will have to venture even further afield to answer today’s most pressing materials science questions. Some examples of material science innovation that are having an immediate effect on industry include:
Materials modeling and simulation provides the foundation for bringing materials science research into the 21st century. The few resources needed to build a model compared with physical experimentation allow researchers to explore a wider range of solutions to a given problem.
Consider the often contradictory nature of consumer goods research. A seemingly straightforward and mundane product like a laundry detergent must remove stains yet preserve colors; add fresh scents while eliminating unpleasant ones; and be strong enough to break down dirt yet safe enough for prolonged contact with skin. Each of these contradictions are critical to the performance of the final product, yet also presents unique engineering challenges. Modeling and simulation allow these challenges to be examined down to the subatomic level.
Advanced materials will also have enormous impact on vehicles for land, air, and sea transportation. Stronger, lighter, and more adaptable to the explicit function and form requirements of the vehicles, these advanced materials will change the very face and future of all these industries.
Due to the large variety of material properties, materials modeling must bring together a corresponding multiplicity of analysis tools to simulate and analyze mechanical and physical properties, from electronic and atomic models to mesoscale models. Design engineers can now look to the possibility of having a new and unique material designed to meet the specific form and functional requirements of the part. Quantum mechanics simulations can explore the thermodynamic stability of the material components and atomic-level simulations can assess the strength of molecular bonds and interface energies between the components to predict material strength.
Combining multiple approaches highlights the different aspects of exploratory material formulation and thus builds the foundation for the understanding scientists need to predict the properties of materials. Armed with this knowledge, they can better determine which materials (or combinations of materials) to test in the laboratory. In fact, virtual testing can (and should) precede and guide physical testing.
To achieve truly materials-based product design, researchers must, at some point, address the design of the structures and systems that will comprise the final product. Numerical simulation methods such as finite element analysis (FEA) can determine the behavior of a completed part based on its shape and composition. Such computational approaches allow engineers to optimize the shapes and structure of new parts. Coupled with modeling and simulation, this maximizes the use of materials developed upstream in the value chain. As a result, teams of modelers can attack design problems from multiple angles and collaborate to optimize parts and, eventually, systems without constructing a single physical prototype.
Modeling, simulation, and advanced analytics are excellent tools for transforming of data into knowledge, but that is only part of the story. Organizations must also manage this knowledge in such a way that it is available to all stakeholders across the product development lifecycle.
Beginning with the laboratory scientist’s research, this process progresses through various lab teams for reviews and confirmations under the direction of lab managers who plan, assign, and schedule research activities. The process can generate a vast number of reports, reviews, models, and test results. Multiply this work by hundreds or thousands of separate material variations and the volume of data and knowledge quickly becomes enormous. Sharing this knowledge effectively among all participants at each point in the research process requires moving beyond siloed approaches and adopting a more digitalized approach using tools such as an electronic lab notebook (ELN).
With many disparate sources of information, only a centralized knowledge repository like an ELN can provide a common thread along the entire R&D lifecycle. By connecting all the research related to a given product in a unified, shareable environment, the ELN reduces much of the complexity and elucidates many of the interdependencies of product development. By providing traceability, the ELN establishes the chain of intellectual property development. It collects and connects all scientific, engineering, testing, standardization, certification, and manufacturing data in a single place, creating a knowledge base for every organization’s most powerful asset, its people.
Research and development approaches across many industries are transforming as companies seek novel solutions to old problems such as light-weighting structures, improving energy storage, and democratizing AM. This is already impacting industries such as aerospace and defense, automotive, medical devices, and energy generation.
The next generation of batteries will need to store more power and last longer, especially as new technologies like electric vehicles become more widely adopted. However, today’s battery materials are reaching the limit of their capacity. To achieve true mainstream adoption of the electric vehicles and “smart” buildings and cities, discovering the next new material for these batteries of the future is becoming crucial. From solid-state to hydrogen-based, batteries are changing the world; materials science can help overcome the remaining roadblocks.
Researchers in this area have focused their attention on solid-state batteries and the materials needed to build them. Solid-state batteries promise to do away with the liquid compounds that have provided electrical current ever since early inventors dipped some copper plates into a brine solution. Liquid electrolytes soon became more hazardous as substances like sulfuric acid replaced the brine, a development still used in vehicles to this day.
Higher powered lithium-ion batteries can be a fire hazard. Solid-state batteries will mitigate this risk, recharge much faster, store significantly more power in a given volume, and - especially interesting for automobile engineers - can be molded into many shapes. However, solid-state batteries currently remain prohibitively expensive to produce at scale. Continued research into new materials is one way that researchers are working to tackle this challenge. Improving materials performance can drive large-scale industry acceptance, which could unlock the economies of scale needed to decrease initial costs.
Companies are looking at a more radical change in the technology. For example, Sakti3, a Michigan startup, is trying to commercialize a lithium-ion battery with a solid electrolyte. Sakti3 has found a way to make a solid-state lithium battery with a thin-film deposition process. This technique is already widely used to produce products such as solar panels and flat-panel display screens. This solid-state technology will offer about double the energy density, which could double the range in an electric car.
The firm’s edge is knowing what materials to use and how to make the process cost-effective. Everything was worked out, simulated, and tested virtually before the company built a pilot production line. As the firm selected materials and developed processes, the virtual computer tests enabled it to forecast the cost of scaling up production.
Researchers at the DOE’s Lawrence Berkley National Laboratory are working on a magnesium-ion battery that should provide higher energy density than lithium. The material they came up with, magnesium scandium spinel, has ion mobility comparable to solid-state electrolytes for lithium batteries. The team at Berkley point to a concerted effort to bring together computational science, synthesis, and a variety of simulation techniques to identify a new class of solid conductors that can transport magnesium ions at unprecedented speed. This is essential for conductivity and, ultimately, a new class of solid-state batteries.
Automotive companies, like Toyota, are focusing on solid-state battery R&D. Toyota maintains that solid-state batteries are the technology closest to the level of practical applicability required to equip their electric vehicles for volume production. Toyota plans to commercialize them by the early 2020s.
ARC Advisory Group clients can view the complete report at ARC Client Portal
If you would like to buy this report or obtain information about how to become a client, please Contact Us