
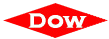




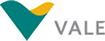

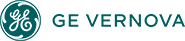




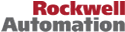

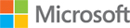
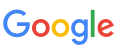

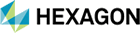


New material formulations in metal powders and plastic polymers are being commercialized that allow additive manufacturing of finished parts with mechanical properties comparable to or better than those possible with traditional production methods. These types of developments are expanding the scope of applications for additive manufacturing. In addition, the introduction of hybrid machines specifically for metal based printed parts, machine builders have combined both additive and subtractive processes. This now offers another opportunity for manufacturers to consider incorporating additive manufacturing into their production processes.
In today's industrial market, additive manufacturing is primarily used for rapid prototyping; ARC estimates that approximately 75-80 percent of the applications are for rapid prototyping. In the product engineering and design process, rapid prototyping has become an integral part of the validation tools used by design engineers. However, increasingly more manufacturers are using additive manufacturing to produce manufacturing tooling, molds and dies, trial production runs, and end-use parts. It’s relatively easy to build a solid business case for using additive manufacturing to produce complex, high-value parts for which small order quantities are required. The increased freedom of design saves time in the production planning process and eliminates any specialized tooling required. A part normally produced in multiple production steps may now be manufactured using a single piece of production equipment. It is also possible to consolidate multiple features/parts into a single part with additive manufacturing.
The challenge for many manufacturers is that they do not have the internal expertise or a well-defined process to objectively evaluate a production part’s suitability for additive manufacturing. In a recent briefing with Tata Consultancy Services (TCS), the management team presented a set of clearly delineated steps the company has developed to evaluate a part’s suitability for additive manufacturing. TCS deploys a range of services designed to assist manufacturers with additive manufacturing. These are divided into Initial Assessment, Design Solutions, and Additive Manufacturing as a Service. As a full-service engineering firm, TCS has well-proven expertise using digital design tools for traditional product design, simulation, and manufacturing process engineering. The company has applied this expertise to product development in medical, aerospace, high technology, automotive, and consumer packaged goods.
TCS can help its manufacturing customers evaluate additive manufacturing for a wide range of components using a broad spectrum of machinery. Initially, the company developed an internal process to evaluate production parts for suitability for additive manufacturing. Subsequently, it formalized the process with a knowledge-based decision support system that automated the business justification process. TCS now offers this business justification analysis as a service to allow customers to rapidly analyze and then classify a part for additive manufacturing. This tool is a proprietary analytical solution that gathers input from the customer regarding the part and produces a metric that ranks the part’s suitability for additive manufacturing.
Inputs to the tool include the complexity of the desired part, the surface finish, whether it will need post-process finishing on a subtractive machine, and just how closely the final part will need to match desired tolerances. Also assessed are part quantity and the end application scenario. The tool uses this information to generate a numerical assessment of the suitability of the part, coded either red (not suitable with current technology), amber (not the best candidate, but could be redesigned to be more suitable), or green (qualifies as a candidate). With the above data, this preliminary assessment takes only around 30-45 minutes to perform, but can generate significant time savings as unfit parts are identified at a much earlier stage. The tool considers all additive process types and possible build materials.
Manufacturers with thousands of production parts in their portfolios will recognize this as a very cost-effective way to segment and rank each production part’s suitability for additive manufacturing. However, the TCS framework is a closed loop; while a production part may not be suitable in the first pass evaluation, the company will employ its Design Solutions group to evaluate mechanical design alternatives. Armed with its expertise in digital design services for both product design and manufacturing process design, the company can identify design changes that would enable the manufacturer to develop a valid business case for moving the part to an additive manufacturing process.