
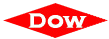




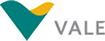

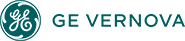




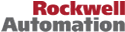

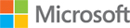
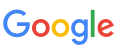

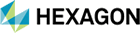


In asset intensive industries, such as oil and gas, routine maintenance and inspections are crucial for proper asset management. Regular maintenance and inspection works also help to ensure workplace safety. Various new technologies are playing a major role to help improve and simplify these routine tasks and thus, in turn improve the integrity and reliability of assets and infrastructure. Remote monitoring is one of the latest technologies used in the oil and gas and other process industries for better asset management.
Remote monitoring will not replace hands-on work performed on the plant floor or in the field. But it can reduce the time to respond, analyze, and remediate asset issues. Information is gathered from the field via mobile, handheld, wired, or wireless monitoring instrumentation on a continuous or near-continuous basis. Whether collected remotely, onsite, or via a combination of the two, data can be used to create predictive maintenance programs to help prevent asset failures by scheduling maintenance activities to minimize production interruptions.
With remote monitoring, end users can better leverage the expertise of their subject matter experts to help manage critical assets across the entire lifecycle. At the 2018 ARC Industry Forum, Braskem, a major global chemical company, shared with the audience their digital transformation strategy, that included specific focus on remote monitoring. The company implemented a new visualization platform and set up an asset monitoring center. The asset monitoring center continuously receives input on asset health through online monitoring. In addition, data can also be entered offline. The center is staffed with a variety of specialists, including a mechanical rotating equipment specialist, electrical engineer, instrumentation engineer, and static equipment specialist. These specialists look at various platforms and monitor the health of the equipment. They continuously analyze the incoming data and send their input to ERP systems, so that maintenance activity can be planned accordingly. In the future, Braskem plans to add analytics capability to better equip its specialists.
As end user organizations across all industries continue to face a shortfall of qualified personnel, advance Industrial IoT (IIoT) solutions can help fill this skills gap. Forward-looking suppliers are already investing to bring IIoT capabilities to their offerings, such as remote monitoring and remote services. These capabilities can help establish a more collaborative relationship between end users and suppliers.
At the 2016 ARC Advisory Group Forum, Emerson Automation Solutions shared how the company is leveraging the IIoT to help end users reduce valve-related unplanned downtime. Emerson initially began looking at adopting IIoT technologies as a way to collect more valve health data from the field and provide more realistic valve failure information than could be generated in a lab. It soon became apparent that IIoT technologies were a natural fit for developing a remote monitoring service to help optimize customers’ valve maintenance practices.
The company designed a valve maintenance service that leverages its valve expertise to fill existing gaps in valve maintenance practices and bring more actionable information to end users. To start, it collected valve performance data from customer plants and analyzed it extensively to better understand why valves fail and design a way to predict valve failures before they occur. Emerson partnered with software company, Seeq, to improve the data visualization tools used to predict future valve alarms. Seeq used its expertise in accelerating insight into time-series data to help Fisher Valve Division build a collaborative environment connecting customers with local Fisher services experts and global valve experts. This environment enables data from multiple sources to be visualized and aggregated and allows people located around the world to look and work on the same data in a collaborative manner.
Many suppliers now use high-definition cameras and augmented reality tools to better help their end users remotely maintain their assets. If something is wrong with an asset, such as a pump or a valve, suppliers can remotely look at the malfunctioning asset and can send appropriate service personnel with necessary replacement parts. In some situations, end users may be able to fix the issue themselves as well, with assistance from the supplier’s remote crew.
ARC recommends that end users identify critical assets and processes where they can benefit from remote monitoring. If end user is considering partnering with a supplier to provide expert remote monitoring services, they should note that to benefit fully from this type of service, operations/maintenance/engineering teams need to work together with IT department. For an effective asset management program, end users should start with a comprehensive plan and develop a clear strategy for the project. They should make it a priority to involve the right people and then properly train them about new work processes.
More information on Braskem’s remote monitoring initiative can be found at this link, and details on Emerson’s remote valve monitoring services can be found at this link.