
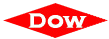




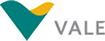

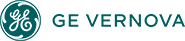




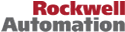

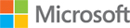
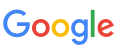

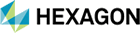


Looking ahead, upstream owner-operators and oilfield services companies will have to become even more cost- and energy-efficient and environmentally aware when drilling new wells. This will involve managing oilfield drilling operations to reduce overall costs, increase performance, reduce operating and financial risks, and minimize impact on the environment. The last few years have seen an upsurge of new drilling technologies being deployed, with methods from different disciplines being deployed to enhance oilfield drilling optimization. Communication and software technologies, and analytics are the most critical disciplines that can help optimize drilling. Large amount of data could be piped through different locations in reliable and timely ways. Advanced computer technologies are now being used to store large amounts of data and solve complex problems.
Success in implementing an optimized drilling program depends on several factors. These include the accuracy of data from the control wells upon which recommendations for the proposed well are based. Key rig selection criteria for optimization include hydraulic horsepower requirements, sufficient bit and drill collar weight, rotation speeds, adequate mud handling, bit type, and geology of the formation to be drilled. Data required for drilling optimization includes logs (preferably IES or sonic), bit records, mud records, recorded drilling data (torque, pump pressure, penetration rate, etc.), and the drilling specifications for the proposed well (casing points, hole size, expected problems, etc.), rig specifications, and correlation of formation tops to proposed well.
In general, the greatest data accuracy will be achieved by measuring instruments applied as close as possible to the vicinity of target load. Until recently, most drilling parameters were derived from load measurements taken on supporting structures or equipment related to the drill string—but not actually a part of the string. The remote position of these conventional sensors from the desired load often resulted in unacceptable error rates. Drilling optimization software such as Max3Di, developed by Halliburton, supports modeling, measuring and optimizing drilling performance. These types of software can also increase directional drilling efficiency and reliability by immediately detecting out-of-bound conditions. When combined with downhole sensors, they can also track cumulative vibration and torsional efficiency for end-of-life monitoring
Real-time, operations centers (RTOCs) for E&P emerged more than a decade ago. Using information-sharing technologies, software, the Internet, etc., to build collaborative hubs that could pool expertise and resources to improve a multitude of E&P operations spread out over any range of geographical locations. Shell’s RTOCs and Baker Hughes’s BEACON (Baker Expert Advisory Centers and Operations Network), for example, can help remote operators solve problems. Traditionally, if a downhole pump failed, the service company and operator would usually perform a tear-down of the pump together to find the cause of that failure. This would involve representatives of both companies traveling to one location to do the tear-down. However, real-time connectivity from the rig to the office is becoming the norm for many operations today. The real-time operation support center (OSC) is the hub of these activities; where domain experts, data interpretation experts, and drilling experts alike can be involved directly in data-centric collaboration and critical decision making. Having the ability to move the point of decision making from the point of data acquisition to the OSC intuitively provides the capability for more effective drilling optimization and the direct saving of non-productive time through risk mitigation.
Prior to implementation of the RTOC, one particularly challenging exploration well in a remote region of Peru had come in 100 percent overspent due to numerous wellbore stability and sidetrack issues. The company adopted collaborative software tools linking geological & geophysical and engineering databases. This improved collaboration between the geoscience and engineering domains to overcome increasingly complicated technical risks and uncertainties. Real-time well monitoring through RTOC, that accesses and visualizes real-time rig data from anywhere in the world, helps reduce the costly non-productive time (NPT) in complex wells.
Drilling optimization is designed to reduce drilling trouble time and optimize drilling practices using critical data interpretation based on a variety of downhole and surface sensors and specialized applications.
In general, a competitive drilling optimization system should include solutions for: drill string integrity (such as bit/pipe vibrations and bottom hole assembly vibrations), hydraulic management (such hole cleaning), and wellbore integrity (such as wellbore collapse modeling). Over the past few years, new technologies, automation, and advanced analytics have made significant progress in making drilling more efficient, particularly in improving real-time decision making. The process starts with real-time modeling, then proceeds to the integration of the real-time modeling and data, and passes finally to the real-time operation centers.
ARC is initiating research into the markets for drilling optimization systems, including technical areas such as managed pressure drilling, underbalanced drilling, software designed to better optimize mud pumps, reduce kicks and stuck pipe, etc. ARC welcomes the opportunity to speak with technology suppliers and users alike about your activities, thoughts, perspectives and questions on this exciting area.
For further discussion or to provide feedback on this blogpost, please contact the author, Jyoti Prakash, at jprakash@arcweb.com.