
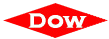




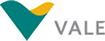

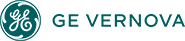




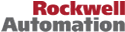

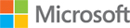
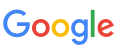

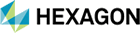


Effective asset performance management (APM) requires real-time maintenance execution so maintenance tasks can be planned and performed when needed based on actual operating and asset conditions. This helps avoid critical equipment failures and associated unplanned equipment downtime. This approach involves integrating technologies, people, and processes to provide the right information at the right time.
APM operates across multiple functional areas including maintenance, reliability, inspections, operations, and engineering. The technologies associated with these functions include enterprise asset management (EAM), field service management (FSM), condition monitoring (CM), and control systems. This extends into mobility and the Industrial Internet of Things (IIoT). Integrating these systems helps assure that data from one domain can be augmented with information in other applications to identify issues and inform users in a timely and in-context manner. Automated business processes enabled by this integration help ensure the resolution problems before critical asset failure. For example, when operating conditions indicate a developing problem in a critical asset, an alert allows decision makers to plan maintenance prior to failure.
Business Drivers for APM
The asset management function in industrial facilities continues to face pressure to improve uptime, asset longevity, and safety, while controlling costs. ARC has surveyed end users several times during the past decade, and each annual survey has "improve uptime" in the top position. The top four goals – uptime, asset longevity, cost control, and quality/yield – relate to C-suite metrics that are included in the typical company annual report.
The following business drivers provide the basis for the good business case and project justification needed to obtain management attention and allocation of the needed resources for successful implementation.
Revenue: Uptime improves equipment availability so production can meet its schedule – which directly effects customer satisfaction and revenue.
Balance Sheet: When assets last longer, the company retains cash and avoids using it to purchase replacement assets. Conserving cash improves the financial ratios used by Wall Street to measure the value of a company.
P&L: Maintenance effectiveness – particularly in the asset-intensive industries in which maintenance is a significant cost – impacts the P&L statement. Improved maintenance effectiveness can help reduce unnecessary maintenance or prevent unscheduled downtime and the related labor, material, and equipment losses.
Risk: Either intense competition or regulatory compliance drive executives to carefully manage risk. The goal of safety and risk management aligns with this concern.
Disconnects Impact Overall Performance
Most organizations have maintenance, reliability/inspections, and operations in separate departments with different managers and metrics. Usually, each organizational silo has been well optimized to meet its metrics – if not the manager would have a job continuity issue. However, between the organizations these different metrics lead to disconnects, delays, and sub-optimal overall performance. The key metrics for maintenance typically include equipment uptime, asset longevity, reliability and cost control. Production has a different set of metrics that includes on-time delivery, quality/yield, quantity, and control of production costs. While complementary, these goals are distinctly different, encouraging the two groups to operate independently and thus sub-optimally.
Each of the domain areas comprising APM has an ecosystem of users, applications, suppliers, and integrators. The associated management systems developed independently and, to a large part, remain separate silos. The applications and associated metrics often conflict with other silos. In this environment, activities and business processes that extend across multiple silos often exhibit dysfunctional behavior. Unfortunately for the business, there is little or no focus on the gaps between silos and associated inefficiencies. For example, a delay or disconnect between issue identification (by an operator, inspection or condition monitoring), and resolution (by maintenance) can cause unplanned downtime. This needs to change.
Data Quality and Master Data Management
Manual and paper-based systems tend to create delay and data entry errors that negatively impact system integrity. When people don't trust the system, they create workarounds and manage activities manually; resulting in declining productivity and increasing waste.
Since APM involves activities that involve high management visibility when things go wrong, the participants typically have a low tolerance for data quality issues within a silo. However, data inconsistency, incompleteness, ambiguities, and latency will occur between silos. This drives a need for some form of data standardization, which can range from simple translation look-up tables to cross-silo naming conventions. For initial pilot projects, it's best to keep this data management methodology simple. When the pilot projects succeed and are extended to a broader enterprise, organizations should consider including an appropriate level of master data management.
Business Process Automation
With a good APM strategy, operations and maintenance groups become more collaborative, exchanging information to manage critical issues and operational constraints while improving overall operating performance. Determining the business' unique critical issues provides a foundation for an APM initiative. Leveraging the rich information in the operations and maintenance solutions improves the effectiveness of both areas. Combining the information from the traditionally separate solutions offers new opportunities for managing risk and optimizing performance.
APM encapsulates an emerging, key business process. Using information from production management and control systems in asset management applications provides new opportunities to optimize asset availability. Also, information from the asset management applications provides new opportunities for organizations to balance operational constraints and improve return on assets (ROA). APM applies to the long, "operate and maintain" phase of an asset's lifecycle in which margins and profits are determined.
Maintenance Execution Maturity Curve
This exchange of information among systems provides opportunities for condition monitoring and predictive maintenance; an approach that allows maintenance staffs to anticipate failures and schedule work orders accordingly. A study by a major petroleum company showed that, compared to calendar-based preventive maintenance, a predictive approach reduces maintenance costs by 50 percent. Nearly all EAM systems have an interface for alerts to automatically generate a work order for a planner to review and schedule. This type of business process automation helps assure consistency between a specific problem and responsibility for rectification. This business process automation helps overcome the delay and waste that typically exists between silos. Collaboration and business process automation across operations, maintenance, and reliability groups are needed to increase overall business responsiveness.
Schneider Electric Avantis APM Solution
As ARC Advisory Group learned in a recent briefing, the Schneider Electric Asset Performance Management solution includes both Avantis EAM and Avantis Condition Manager. The combined solution is designed to help industrial customers improve the availability and performance of their critical assets, and provides real-time maintenance execution.
The Avantis EAM offering has a range of functions for managing maintenance including asset information, work order planning and scheduling, purchasing, inventory management, human resources, and financials.
Avantis Condition Manager collects operational information and performs diagnostics in real time. It is platform independent to work with a variety of EAM and control systems. This product has matured with over 10 years of use, customer feedback, and development. A wizard approach makes it easy to configure diagnostic algorithms and alerts that drive the appropriate actions by maintenance, operations, and engineering.
Conclusion
APM provides a strategy for improving visibility and systematically improving key metrics like uptime, mean time to repair (MTTR), asset longevity, cost, quality/yield, and safety. Rather than accepting APM waste because it is difficult to find or quantify, ARC recommends that industrial organizations develop a disciplined approach for improvements. Based on research and analysis, ARC recommends the following actions for owner-operators:
All signed-in ARC Advisory Group clients can view this report in pdf format at this Link
If you would like to buy this report or obtain information about how to become a client, please Request ARC Info
Keywords: APM, EAM, PdM, RCM, IIoT, Mobility, ARC Advisory Group.