As we've discussed in at least one
previous post on this blog, virtual reality is emerging as an increasingly practical option to train field operators. Many field operator training programs utilize gaming technology where field operators are modeled with avatars and manipulated with game controllers. These typically involve some form of 3D visualization on a computer screen or 3D headset. Multiple "players" can often participate, with dynamic interaction with a console operator manipulating a process and control system simulation. The cost of "realism" has dropped for the process and control systems simulation, but has dropped even faster for 3D visualization. Constructing a high-resolution 3D model that represents a real physical facility had previously been a costly endeavor. However, new photo-metric and LIDAR methods are making such 3D models much easier and cheaper to create. Newer facilities that have a 3D CAD design model often use this for training purposes. (In the past, plants were designed using drafting and paper with no effort to create a digital model.) While less expensive to create than ever, these 3D models still cost a lot and can suffer from a lack of fidelity. The static 3D model is only the starting point to create a virtual reality based-simulation, as equipment must be animated and linked to simulation actions. The new operators from the millennial generation are accustomed to virtual reality in modern computer video games. Pokémon Go has seen amazing popularity and has been touted as a gateway to augmented reality applications. Augmented reality may yet find a place in for operator training in industrial settings. A smart helmet (hardhat) like the
Daqri helmet with heads up display may provide a platform for such training, but many industrial facilities have hazardous environments requiring appropriate electrical certifications. But this doesn't appear to be an insurmountable problem. There are a few suppliers of rugged intrinsically safe cell phones with some unique features that make them especially useful in a hazardous industrial setting. The “ECOM” company, for example, is well known in this area. There are also devices with software applications to support “push-to-talk,” glove friendly interaction, displays for direct sunlight, and that can read messages from NFC (near field communication) tags.
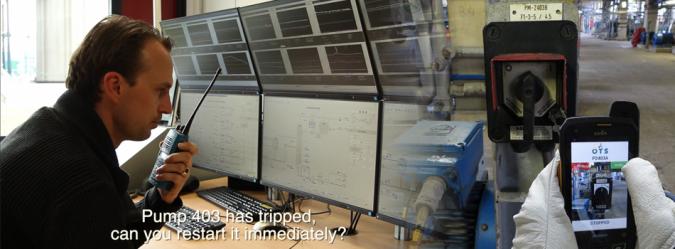
The OTS experts at
Operator Training Solutions have exploited just such a device to implement field operator training in a unique way that greatly increases the fidelity of the training experience. By using low-cost, passively powered NFC tags placed at various plant locations like transmitters, valves, pumps, or switches, the company has developed a novel simulation training program. This requires the field operator to physically go to these NFC tags (typically within two inches) and read them with an ATEX-certified smart device. Once the NFC tag for the plant equipment is read by the smartphone, the phone displays the simulated state of that device. In coordination with a console operator and a process simulation, the field operator would need to take simulated actions, but only on the ATEX smart device. For example, the field operator might approach a real pump and upon reading the NFC tag discover the pump is simulated on fire. The field operator must then physically walk to the pump shutoff switch and read that NFC tag before he/she is allowed to turn the simulated pump off on the ATEX smart device. In this simulation, the field operator must walk to specific locations in the real plant, but only interacts with the simulation on the ATEX smart device. The console operator running the simulation is separate from the console operator running the plant. This means the simulation takes place in a highly realistic setting, with full safety equipment and the smartphone displays the simulation of reality, which is essentially augmented or perhaps "substituted" reality. By training in the real plant, no 3D model is required. To avoid confusion, the actual shift operators would need to be aware of the simulation schedule/activities, the plant needs to be in a normal accessible condition, and the simulation group would absolutely need to be using separate channels for walkie-talkies or push-to-talk devices. The company experts mentioned that its client called this method, “real reality." We are all very experienced with simulation. We have acted out many hypothetical situations in our minds and that is how we learned so much of what we know. Just think back on all the toys, dolls, pictures, sculptures that you used as models. The act of pretending, imagining scenarios, using thought experiments to explore "what ifs," is simulation, and simulation is made much more realistic using these models as props. In the near future, both virtual reality and augmented reality will increase in importance for critical operator training tasks. Consider operators at nuclear plants, refineries, oil rigs, chemical plants, and even food and pharmaceutical plants and you can see that mistakes can cause huge consequences and avoiding mistakes depends on effective operators. Simulations of all kinds are how we learn. The digital world is opening up many new avenues where simulation can be used effectively to learn key skills. Like the flight simulators used by pilots, realistic simulations of important abnormal scenarios can give operators mental experiences they need to be effective when they face real problems that require situational awareness and decisive actions. Several sessions at the upcoming
ARC Industry Forum in Orlando, Feb. 6-9, 2017, will focus on operator training simulators. If you'd like to learn more about how 3D simulation and VR are being used to enhance operator training, please, by all means, join us.