
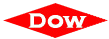




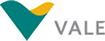

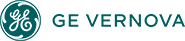




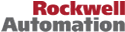

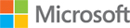
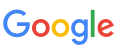

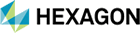


About the Client: The client, one of the world’s largest piping and casting solution providers, uses several Special Purpose Machines (SPM) for specific tasks during the manufacturing process. One such task is to create grooves for fitting pipes. The existing process relied on creating grooves manually. This resulted in inconsistent grooves, required a lot of time, and was risky as the work involved a rotating spindle. The client was on the lookout for a partner who could help them automate the process to improve grooving consistency and safety. LTTS’ (L&T Technology Services Limited) expertise in cross-pollinovation and engineering special purpose machines, such as the World’s 1st Gyro Screwdriver, made it the perfect partner of choice for this project.
Challenges: The client’s main challenges:
Solution: LTTS’ engineers did a thorough analysis of the current working setup and proposed a semi-automatic SPM to conduct the desired grooving.
Design: The new design consisted of a spindle that moves at half the RPM of the original machine and a cutter that moves in a linear axis to groove the product’s circumference. The entire machine is modular and can be easily configured to groove different product lines with minimal changes.
Machine vision: A laser-based machine vision system controlled by PLC ensures that the product is positioned correctly before moving the cutter.
Proofing: The Poka-Yoke based position detection sensor ensures the right part is loaded with right orientation. If there is any discrepancy, it will raise an alarm and the spindle will not rotate.
Quality: A separate machine vision system checks for the groove depth and width with a master image that ensures consistency of each groove.
Safety: The complete setup is placed inside a glass enclosure and the machine operates only when the light sensors are active. In this semi-automatic setup, the worker positions the product for grooving and moves out to a safe distance. The machine starts the operation only after this process is completed, thus protecting the worker from flying debris.
Quantifiable Benefits: The client benefited in multiple ways: