
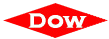




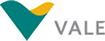

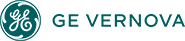




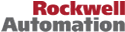

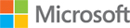
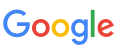

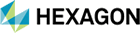


Companies can reap huge benefits in terms of productivity, business continuity, and clear ROI, from well implemented asset performance management technologies. As part of asset management services, some of the key offerings from L&T TS include engineering information management (EIM), material and inventory management (MIM), and enterprise asset management (EAM). L&T TS assisted a chemical manufacturer to streamline their maintenance management by providing ERP implementation support including creation of a standardized equipment master data; data management as part of EIM; MIM support; and executed other engineering documentation updates for asset information management.
Background and Challenge: Data capture, validation, and documentation is at the core of engineering information management. The client’s equipment master list was not updated, and critical prerequisites for creating the master database such as the asset register and spares inventory were incomplete. This created gaps in information and resulted in delays in spares procurement, maintenance of assets, and increased the possibility of high downtime. Added to this, local vendors were not available at remote plant locations resulting in further delays in operations and maintenance.
The client took the help of L&T TS to structure disjointed asset and spares data, including update of as-built plant engineering details and equipment specific engineering details. Moreover, a framework had to be put in place so that asset data would further be shared and utilized for asset reliability and maintenance.
The Solution: L&T TS provided SAP implementation support for asset information management. It was built across three phases:
Quantifiable Benefits: The client now had the complete equipment register along with required class and characteristics categories as per the global information management standards. L&T TS updated all the soft tags (control modules) and the missing instrument tags as per the site conditions.
The completed P&IDs serve as an important reference for process safety management, and it is critical to always keep them updated as per the site conditions. The L&T TS engineering team deputed at the client site identified the safety points and the same were communicated to the client. Lastly, as part of the document management services the client took the assistance of L&T TS to prepare technical dossier and technical construction files.
Keywords: Asset Information Management, Maintenance Management, Document Management, P&ID, Tagging, Process Safety Management, L&T Technology Services, ARC Advisory Group.