
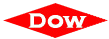




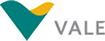

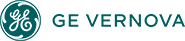




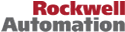

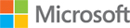
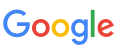

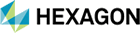


Introduction
Rohit Kedia, Chief Business Officer, Manufacturing and ERP Services for the Americas at L&T Infotech, is responsible for the company’s business across all manufacturing sectors. These include industrial manufacturing, automotive, aerospace, chemicals, resources, energy and construction. Mr. Kedia is also accountable for the go-to-market strategy for ERP and IIoT services. With 20 years of experience, he has become a thought leader for IT, consulting, and outsourcing.
ARC Advisory Group had an opportunity to ask Mr. Kedia a number of questions on topics related to the Industrial Internet of Things (IIoT) that impact manufacturing.
How do you think the IIoT will affect production operations and the manufacturing value chain?
Rohit Kedia: IIoT is a source of innovation, disruption, and competitive advantage across the manufacturing value chain. The multi-fold transformations possible create a variety of benefits beyond just cost efficiencies. Whether it is providing real-time production data to uncover additional capacity in a plant, enabling real-time operations data with predictive analytics to reduce unplanned downtime and decrease inventory, or creating visibility and control over industrial control systems environment to prevent cyber-attacks; IIoT solutions can drive powerful business outcomes.
L&T Group’s electrical switchgear manufacturing business, for example, uses IIoT to reduce waste and improve customer satisfaction through process quality and error-proofing. In automotive assembly, the accurate location-sensing of the car body at every workstation on the assembly line has amplified mass customization possibilities. Several manufacturing industries, such as aerospace, face a risk of knowledge depletion because of the aging workforce. IIoT can help mitigate this through augmented reality on the shop floor.
Because IIoT creates new supply chain configurations, manufacturing can move closer to consumption. This can improve market responsiveness while still keeping costs low. In addition, IIoT solutions can shorten the feedback loop to design; hence compressing NPI lead times through closer integration throughout the manufacturing chain from PLM to customer. Of course, a whole new level of cost efficiencies is now possible. Predictive analytics can drive higher asset performance, improved worker productivity, and optimized utility consumption. Now, manufacturers can improve operational efficiency through predictive maintenance to achieve results such as savings on scheduled repairs, reduced maintenance costs, and fewer breakdowns.
A case example involves a leading manufacturer of construction and mining equipment, diesel and natural gas engines, industrial gas turbines and a wide offering of related services. L&T Infotech worked with the manufacturer to use industrial analytics to harness and analyze data from its machines, engines, and services. The resulting insights and data are then sent to the manufacturer’s dealers to help them anticipate problems, proactively schedule maintenance, and help customers manage their fleets more efficiently. The company says its dealers in total can capture anywhere from $9 billion to $18 billion in revenue each year should they move customers from “fix when fail,” to predictive maintenance along with other actions. The company benefits by lowering its warranty fulfillment costs, and boosting sales of new machines, parts and services.
Much has been written about the impact of IIoT for industrial firms. How much of this is hype vs. reality?
Rohit Kedia: Not only do I believe that the IIoT opportunity is real; I think we have just scratched the surface. We’re seeing an unprecedented convergence of the digital and physical worlds. The impact IIoT can create for industrial companies goes far beyond extracting the next level of efficiency and asset performance. The full impact is realized when companies can transform the underlying business model to disrupt and create new paradigms of competitiveness in any given industry.
There are many real-world instances. Take the example of a multinational steel-making company based in South Korea. The company applied IIoT and analytics to two hot coil factories to reduce unplanned corrective maintenance by 45.5 percent. This saves the company $1.4 million annually. Another is a coal mine in Slovenia that uses IIoT and predictive analytics to reduce production delays by 22 percent and lower maintenance costs by 16 percent. Yet another IIoT application is monitoring the valves that control the gas flows to flare stacks in refineries. Using wireless acoustic transmitters, one refinery improved regulatory compliance and reduced hydrocarbon losses by $3 million annually due to timely detection and repair of faulty valves. The project paid for itself in five months, with an estimated annualized return on investment (ROI) of 271 percent over 20 years.
Another example of IIoT in action is at a leading US-based oil & gas company that increased asset utilization based on predictive maintenance. The Smart Asset solution from L&T Infotech helped the client put a system in place that predicts problems and schedules maintenance of their compressors. The predictive maintenance system enabled the company to reduce maintenance expenditure and energy consumption and avoid unplanned shutdowns. Missed production in each shutdown can result in $20 million in lost revenue.
A semiconductor manufacturer improved production efficiency by 8 to 10 percent with our expertise in IIoT solutions. We have worked with many other customers, including an automotive organization, to deliver smart asset management solutions that have reduced time to market and improved process efficiency. L&T Infotech helped a downstream oil & gas company gain visibility into order fulfillment and tracking of sales returns and pricing reversals to help improve the accuracy of execution and order fulfillment.
We’re seeing realized, quantified benefits all across the industry and in all departments and functions of a manufacturing organization: operations, supply chain, production, maintenance, design, service, HSE, and quality.
How would you compare opportunities for IIoT in consumer industries vs. industrial?
Rohit Kedia: Traditionally, the technology spend in manufacturing industries has been lower than in consumer industries. This is changing with opportunities created with IIoT. Industrial IoT will dwarf consumer IoT in terms of economic impact. Market leaders like GE have bet their future on IIoT by creating platforms for developing IIoT solutions and services to support and leverage the data.
Manufacturing companies have now realized the value of leveraging their operational data – this enables them to be innovative and competitive without huge capital investments. IIoT projects have a very fast payback – less than a year in most cases. IIoT professionals are needed with skills in manufacturing, program management, instrumentation & sensors, communication, security, cloud technologies, analytics, artificial intelligence, mobile applications, and visualization.
This has created a climate for manufacturing to invest in IIoT and hence good career opportunities for the right talent. Another indication of the impact of IIoT is the large amount of research done by industry analysts, conferences like ARC Advisory Group’s Industry Forums for attracting top management speakers, and participation in industry bodies such as IIC and large government investment programs for manufacturing.
Why are some companies hesitant to invest big in IIoT despite the stated potential?
Rohit Kedia: There are several reasons, some structural, which contribute to the hesitation to make full-scale investments in IIoT. First, companies still want to establish a clearer line of sight into large incremental business value and whether the outcomes IIoT creates are compatible with their business model. For example, an equipment manufacturer can easily enable connectivity and intelligence in their product; but is not sure whether it can access the data because of limitations in data and network ownership in the final install environment. Another issue is the organizational barriers created, such as OT-IT divide. Full IIoT solutions require integration across many technical domains. Staff and resources with these skills are either not readily available or often distributed across functions in an organization with organizational boundaries preventing easy collaboration. Security and privacy concerns also have impacted investments.
What are the critical success factors to realize business value from such investments?
Rohit Kedia: To implement IIoT, organizations must consider several critical factors for success. Enterprises must start with “having the end in mind.” IIoT is not just about making technology work but gaining clarity on how to rethink the business model and establishing a clear pathway to monetization of value. These monetization levers can include improving profitability, differentiation and top-line impact, and entirely new products and services.
In addition to keeping the end in mind, cross-functional collaboration is key to successful IIoT implementations. IIoT solutions require the combination of expertise and integration across digital and physical domains. For instance, it is not sufficient to just assemble terabytes of data from your plant; you need to be able to interpret that data and know where to look for high-value insights. The industry is full of early attempts that were largely focused on digital side without a clear line of sight into the business model impacted, or the underlying physics. And that has led to many failures.
Because IIoT transforms the nature of work from traditional to knowledge-based roles with real-time access to data from industrial assets, organizations should keep this change in mind when assigning resources. For example, at a manufacturer’s operations center in Australia, skilled equipment operators now sit in a remote command center. They work side-by-side with data analysts and engineers to orchestrate the actions of huge drills, excavators, earth movers, and dump trucks across multiple mining sites.
How can industrial companies benefit from L&T Infotech investments in IIoT?
Rohit Kedia: L&T Infotech partners with its customers to help them define, implement and sustain high-value IIoT innovations. We are making significant investments in selected IIoT applications that offer the highest potential gains for a number of industries in the years to come. These include smart manufacturing, asset performance, smart services and industrial security for industries such as oil & gas, power, semiconductors and high-tech, automotive, CPG, and industrial machinery.
We are well positioned because we bring real-life expertise across digital and physical domains. L&T Group is an industrial conglomerate with seven decades of experience in multiple industries, so its industrial heritage manifests in several ways in delivering differentiated capabilities in Industrial IoT through L&T Infotech.
What unique capabilities does L&T Infotech offer?
Rohit Kedia: L&T Infotech has expertise in the physical world and underlying engineering disciplines. When it comes to a factory, for example, we understand all critical domains including electrical, instrumentation, automation, supply chain, logistics, and safety. L&T Infotech goes far beyond the pure digital capabilities that most companies focus on to truly understand the business needs of our manufacturing customers.
We have real-life proving grounds. At L&T Infotech, we don’t just build solutions in an IT lab. We take them out and prove them in real-life operating environments. Our solutions make money for our customers. Here’s an example. We created a smart manufacturing solution for using a variety of sensing technologies which was deployed in our own plants. Closely integrated with advanced planning and scheduling systems, L&T tool rooms reduced the time taken to manufacture complex equipment from 30 days to 15 days. That is a huge business impact. Currently we are working with L&T’s construction group for their IIoT roadmap and implementation for large construction equipment. This will ensure tracking of these assets for maintenance, availability, security and when integrated with enterprise systems help inventory management and in hire or buy decisions based on project backlogs. Similar projects are in the pipeline for other L&T manufacturing businesses. Now we can apply the experience in other similar situations – without having to experiment again.
Finally, as L&T Group is a large industrial & engineering conglomerate, we have access to a large ecosystem of customers, suppliers and partners. Our alliances allow us to offer turnkey solutions that integrate capabilities across multiple domains for most industrial sectors. Our customers don’t have to bother about assembling an ecosystem themselves; in most cases we can bring the entire ecosystem to them. The IIoT practice at L&T Infotech incorporates these capabilities in our offerings to our customers in a single-stop model.
What advice would you offer for where or how to begin exploiting IIoT?
Rohit Kedia: There are two important areas to consider. The first is setting up an agile system for rapid discovery of high-value IIoT use cases. The second is defining the business model and monetization path. L&T Infotech helps our customers in a structured manner involving activities ranging from rapid discovery and a design thinking workshop to rapid experimentation and detailed monetization and profitability analyses.
Once the high-priority, business-critical areas to address are defined, L&T Infotech and the enterprise develop a strategy around the connected ecosystem. This involves implementing a pilot program to confirm solution and benefits and then building the roadmap to full deployment while framing the engagement, business model, and milestones.
What advice would you give industrial companies as they transition from the old systems to the new IIoT?
Rohit Kedia: L&T Infotech’s approach recognizes that most manufacturing industries have made substantial investments in their manufacturing infrastructure that cannot be ripped out and replaced. We ensure that we leverage their legacy systems. L&T works backward from the desired outcome to add the needed sensors, communication infrastructure and applications while ensuring no loss of production.
We keep asking ourselves the question, “How do we create profitable growth for our customers?” Our competitiveness can increase through new equipment differentiation and service offerings, pull-through revenues, service delivery productivity and warranty cost reduction. L&T Infotech’s mantras are risk avoidance, high availability, proven and tested solutions. We help our customers define their journey to move up the various levels of IIoT maturity while creating value at each step.
ARC Advisory Group clients can view the complete report at ARC Client Portal on Office 365 or Box.com
If you would like to buy this report or obtain information about how to become a client, please Contact Us
Keywords: industrial manufacturing, ERP, IIoT, electrical switchgear, OT-IT, ARC Advisory Group.