
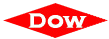




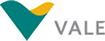

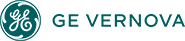




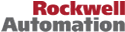

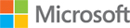
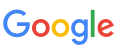

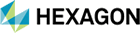


Last June, ARC Advisory Group attended the Internet of Things Convention held at the former Lamot Brewery in the historical city center of Mechelen, Belgium. More than 550 participants, 50 speakers, and 35 exhibitors gathered to discuss topics related to smart industry, smart mobility, or smart cities in five parallel sessions. 3IF.be, a Flemish government-sponsored project to stimulate implementation of state-of-the art technologies in small- and medium-sized manufacturing enterprises, supported the Smart Industry track of the convention.
3IF.be invited Carl Van Laer, global product line leader for OSIsoft technologies at Johnson & Johnson’s Jansen Pharmaceutica site in Beerse (Belgium), to speak about the development and scale-up of a successful cloud-based, machine learning solution to predict the health status of sterilization autoclaves at a biopharma site in Leiden, the Netherlands. The solution enables the company to identify and remediate autoclave health issues prior to failure.
Johnson & Johnson, a leading global healthcare company, has been in business for more than 130 years. The company is organized into three business segments: consumer health products, medical devices, and pharmaceutical products.
To help identify, test, and deploy promising new technologies, Johnson & Johnson created a “Manufacturing for the Future” unit composed of both technology and process specialists. A proof-of-concept installation for a new technology may be created in or after the discovery phase. If the result is promising, a quick small-scale implementation is done in 7- to-14-day sprints to prove the business value. At this point, the company decides whether to roll out the solution at the department level, over multiple sites, or at full scale in multiple sectors. The tests and implementations may be process-related (such as converting batch processes to continuous processes), utility-related, or maintenance-related.
Johnson & Johnson uses a reference architecture containing the components from which an Industrial IoT solution can be built. The architecture has both edge and OT components for real-time instrumentation and control, local visualization and storage, and connectors to enterprise platforms and the cloud. Data ingestion, data processing, data storage, analytics, egress components, service APIs and security are used to complement the enterprise platform tier. The cloud applications include both system and end user applications; some custom built. Security is a key component to help protect the manufacturing installations from malware or ransomware.
The Leiden site, on the Leiden Bio Science Park in The Netherlands, focuses on biotechnology to advance treatment of immune system-, oncology-, and cardiovascular-related diseases. Here, ten autoclaves are used on a routine basis to sterilize auxiliary equipment to avoid microbiological contamination of the products.
Autoclaves are often cylindrical vessels operated with steam at high temperature and pressure. They typically have pressure controls, pressure-relief safety valves, and steam and vacuum valves, as well as critical seals between the removable lid and autoclave body. Mechanical failure can lead to a failed sterilization procedure. As sterilization processes take time, such a failure leads to delays in production, reduces productivity, and increases cost. For Johnson & Johnson, the target was to reduce or eliminate these failures to increase uptime, optimize maintenance intervention, and protect equipment.
The team developed a digital twin of three autoclave systems to predict the need for maintenance, thereby optimizing the process and maximizing uptime. Raw historical data over six to seven years of the autoclave operations were available, a total of two billion records. Data aggregation and cleansing resulted in eleven million records. Two hundred different sensor values per record were used to analyze, tune, and test the autoclave models.
ARC Advisory Group clients can view the complete report at ARC Client Portal
If you would like to buy this report or obtain information about how to become a client, please Contact Us
Keywords: Cloud, Industrial IoT, Machine Learning, Reliability, Predictive Maintenance, Johnson & Johnson, Microsoft Azure, OSIsoft PI Integrator for Business Analytics, ARC Advisory Group.