
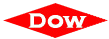




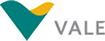

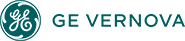




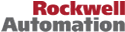

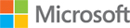
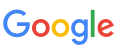

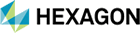


In the pursuit of sustainability goals, organizations face a complex landscape like never before. Rising safety incidents and increasing environmental regulations mean that companies are under pressure to operate plants that are both safe and sustainable. Complicating achievement of this objective is the growing lack of process safety expertise, uncertainty about the safety implications of renewable sources of power for the plant, and lack of awareness of useful new digital tools and technologies.
While there may not be an obvious link between boosting sustainability performance through improving process plant safety, that connection was proposed and made at ARC Asia’s October Digital Transformation Council (DTC) Best Practices event, Driving Safety and Sustainability, featuring guest speaker Steve Elliott, Senior Offer Director at Schneider Electric Process Automation. Delving deep into the core of process safety strategies and digital innovations, the webinar helped to uncover how these not only help to enhance industrial safety but also propel the organization toward its sustainability aspirations.
This blog post captures the main aspects points of the webinar; the entire one-hour event is available for on-demand viewing right here.
In its presentation, ARC Advisory Group highlighted key market trends in both the sustainability and process safety arenas. Industrial companies are responding to the urgent challenge of climate change, with more than 90 percent of manufacturers, according to a recent ARC research survey, having established some sort of sustainability program. And what’s good for the planet seems also to be good for the bottom line, say respondents, with the vast majority anticipating positive business outcomes from their sustainability activities.
Meanwhile in process safety, China, India, and Southeast Asia are expected to be the future growth centers for the estimated $3 billion global process safety systems market. ARC also delivered several recommendations for driving process safety success. These include embracing new technologies, such as software that captures and institutionalizes existing safety knowledge in the company and makes it retainable and repeatable in an environment of scarce skills and expertise; developing stronger relationships with knowledgeable technology suppliers; and internally, facilitating investment justification by championing safety in the context of sustainability.
For his part, Schneider Electric’s Steve Elliott began by articulating three safety and sustainability related challenges: the rising fatality rate in the oil & gas industry; Asia’s position as the world’s manufacturing hub needing to be enhanced through innovation and technology especially given the relative dearth of knowledge and experience; and increasing energy demands necessitating low carbon solutions in a net zero target world.
The increasing footprint of electrical assets, from both renewable energy deployments and more electro-intensive plant processes, means greater safety risks originating from electrical sources. Accordingly, HAZOP (Hazard and Operability study), traditionally applied to processes, and more recently to cybersecurity, should also be applied to electrical systems.
Mr Elliott gave the example of an electrical feedwater pump controlled by a variable speed drive and pumping water into a boiler. Sudden loss of power means the pump can no longer provide the feedwater to the boiler, so the boiler may run dry, it may overheat, rupture, it may even explode. So here, the HAZOP scenario should start with the electrical system as the initiating cause. And the overall objective is to fully understand the risks facing an industrial facility by making sure to include the trinity of process safety, electrical safety, and cybersecurity in the risk assessment.
So how can technology help companies improve sustainability performance as well as enable safety and commercial gains? Well, as Steve Elliott explained, a key requirement for any safety instrumented system (SIS) is that it needs to be tested, documented, installed, commissioned, maintained, and then throughout its life, periodically revalidated. All this requires banks of hardware test panels to simulate process conditions and teams of people often working long hours to test and document (usually on paper) all the various scenarios. It translates to high labor resource costs, especially when tests are inevitably extended, but also environmental consequences from the power, ventilation and air conditioning needed in the hardware test environment.
You can address these challenges by going digital, said Mr Elliott. And it is here that Schneider Electric offers Triconex Safety Validator, which can be used for those SIS development phases, including the periodic revalidations. Instead of writing a test plan into a Word document or an Excel file, it’s written into Safety Validator by filling in a template (no coding needed). The tests can run around the clock and are repeatable since using automated validation eradicates human factors, such as fatigue, human error, and lack of skills, which are often the cause of safety related incidents. Having all tests automatically recorded and documented also eliminates the onerous, unpopular but vital documentation task.
Software-based safety logic validation eliminates the environmental consequences associated with a hardware test environment. Source: Schneider Electric
Another area where Schneider Electric technology is being used to improve safety and sustainability is in bypass and alarm management. This time it is a digital solution, Triconex Safety View, which like Safety Validator is TUV certified to SIL 3, replacing the traditional hardwired, alarm enunciated panels in the control rooms, as well as the key switches used to maintain an instrument or put a bypass on a control loop. Again, removing hardware-based systems with software reduces energy consumption and also boosts safety through improved operator oversight and management of alarms and bypass functions.
“Without software, the energy transition is going nowhere,” was the stark summary from Steve Elliott, as he reminded the audience to consider going digital for their next project instead of falling back to the same old traditional methods. He also revealed quantitative C02 emissions savings from Triconex software deployments in the oil & gas and petrochemical industries.