
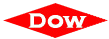




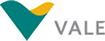

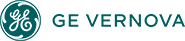




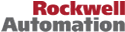

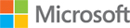
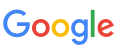

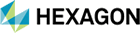


In Europe, the catastrophic accident in the Italian town of Seveso in1976 prompted the adoption of legislation on the prevention and control of such accidents. The so-called Seveso-Directive (Directive 82/501/EEC) was later amended in view of the lessons learned from later accidents, such as Bhopal, Toulouse, or Enschede, resulting into Seveso-II (Directive 96/82/EC).
The Directive applies to more than 12 000 industrial companies in Europe where dangerous substances are used or stored in large quantities, mainly in the chemical and petrochemical industry. Considering the very high rate of industrialization in Europe, the Seveso Directive has contributed to achieving a low frequency of major accidents. The Directive is widely considered as a benchmark for industrial accident policy and has been a role model for legislation in many countries world-wide.
Major accidents involving dangerous chemicals pose a significant threat to humans and the environment. Furthermore, such accidents cause huge economic losses and disrupt sustainable growth. However, the use of large amounts of dangerous chemicals is unavoidable in some industry sectors that are vital for a modern industrialized society. To minimize the associated risks, measures are necessary to prevent major accidents and to ensure appropriate preparedness and response should such accidents nevertheless happen.
We are looking at a best practice report for the use of Ultimo EAM software in a chemical plant to answer this question. Kisuma Chemicals, part of the Japanese Kyowa Group, produces high-quality additives for the polymer production and processing industry. They have four production lines in Europe that operate round the clock. These production sites fall under the Seveso Directive. The proof of conformity to the Directive causes considerable costs and additional work. This is because many additional administrative activities are necessary for the proof of conformity. From the start, Kisuma's approach was to protect the environment and make this process as cost-efficient as possible at the same time.
To achieve these objectives, Kisuma selected a cloud-based Enterprise Asset Management (EAM) system from Ultimo. The first approach was to plan production and maintenance processes in the EAM system. This generates work permits and shift handover information automatically, so that critical situations in these processes are avoided in the first place. It quickly became clear to Kisuma how important this effective exchange of information between the different teams is. With this mode of operation, Kisuma immediately reduced unplanned plant downtime by around 40 percent compared to the old mode of operation.
The company has determined the criticality of the production equipment, based on the ‘Failure mode effects and criticality analysis’ (FMECA) method, which involves quantitative failure analysis. It focuses on qualitative and quantitative risk identification for preventing failures. The FMECA involves creating a series of linkages between potential failures (Failure Modes), the impact on the mission (Effects) and the causes of the failure (Causes and Mechanisms). Kisuma’s objective for the FMECA assessment was to optimize plant safety. In addition to the FMECA assessment, the EAM software also allows each employee to enter short improvement suggestions for even more plant safety into the software.
To further support its maintenance operations, Kisuma has digitized approximately 30,000 documents and made them available to the workforce. This further increases the efficiency of the work process, as each employee always has direct online access to the documents they need to perform their tasks.
More information to the Kisuma use case can be found here.