
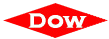




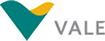

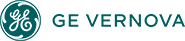




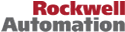

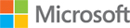
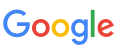

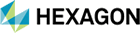


The latest endeavors in reducing operational cost have led to the emergence of real-time monitoring of corrosion in pipelines for integrity management. There has been a growing emphasis for continuous corrosion monitoring over conventional periodic corrosion inspection techniques. This inclination toward introducing real-time corrosion monitoring is purely cost-driven, and has led to significant reduction in periodic maintenance and inspection expenses. For instance, the subsea pipelines were subjected to periodic testing and inspection as mandated by the guidelines (standard codes – ASME B31.4, ASME B31.8, and API RP 1110) for risk and integrity management by associated federal council of the region. A few tests conducted during periodic maintenance included subsea pigging, leak test, and hydrostatic test, for identifying any anomalies in the internal orifice of the pipeline.
By implementing real-time corrosion monitoring system in subsea pipelines, the frequency of inspection procedures can be reduced and certain techniques such as the hydrostatic testing of pipelines can be eliminated, abating the periodic maintenance cost incurred to half or one-third of the original cost incurred during the conventional inspection process.
Non-intrusive monitoring technologies, such as acoustic emission and ultrasonic sensors, are gaining more traction in the corrosion monitoring space over intrusive monitoring technologies, such as coupons and resistance probes. As a result, the established intrusive monitoring equipment suppliers are rapidly losing out market share to the smaller and relatively new non-intrusive equipment suppliers in the global market. This has in turn led to several consolidations in the market, perhaps the most notable being the acquisition of Permasense by Emerson. Other significant market players operating in the non-intrusive monitoring space include ClampOn, Sensorlink AS, Sensor Networks Inc., and A3 Monitoring, among others.
With the increasing influence of Internet of Things on industrial processes, the challenges associated with large organizations in handling information from multiple sources have led to corrosion monitoring solution being deployed as a service. The assets are being connected online via wireless autonomous sensor for analysis over the Cloud. The necessary actionable insights are provided to the operator in the form of messages or alerts.
Furthermore, with the full-scale implementation of asset performance management (APM) tool in the plant, all the corrosion-related information can be managed via a centralized information management system. Scheduled maintenance and repair operations can be carried out with further integration of enterprise resource planning system with the APM.
Our new study reveals which corrosion monitoring technologies represent the largest share of the market, provides a detailed forecast on which regions will see the fastest growth, and explains how embracing real-time corrosion monitoring techniques can enhance the overall pipeline integrity management.
For more information on this and other available ARC market research, please visit our Market Research and Studies section.