
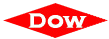




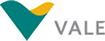

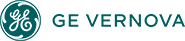




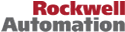

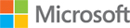
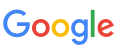

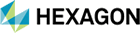


BASF, a large global chemical producer with headquarters in Germany, has operations in more than 80 countries. The company’s manufacturing fleet includes six highly-integrated “Verbund” production sites and 350 other sites around the world. Its goal is to “create chemistry for a sustainable future,” with economic success and environmental and social responsibility. Using digitization and data, the company is increasing the efficiency and effectiveness of its processes while creating additional value for is customers.
BASF’s Reliability Center employs manufacturing intelligence to provide expert support to sites to ensure reliable operation. The Center accesses industrial data from different sources at BASF sites around the globe and analyzes the data to support production sites with recommendations and troubleshooting. Dr. Michael Krauss, Senior Automation Manager at BASF SE, recently discussed parts of the company’s digital transformation with ARC Advisory Group and told us about early successes in achieving global access to industrial data from multiple applications to many data sources in a secure and scalable way.
BASF’s Reliability Center experts need 24/7 access to industrial data from different data sources and locations across the globe to support on-site personnel. This approach permits experts to remotely monitor equipment and catch issues before they cause damage that on-site personnel couldn’t or wouldn’t notice.
Dr. Kraus provided an example of how, in one instance, a remote expert noticed a deviation in compressor behavior. The anomaly triggered an additional inspection that revealed a sticking suction valve. The on-site personnel then replaced the valve and put the compressor back into service before it was damaged. This avoided the high maintenance costs and approximately six days of lost production that could have otherwise resulted.
Dr. Krauss described some of the common barriers that BASF encountered when implementing these types of manufacturing intelligence applications which, in fact, required a new unified industrial data platform to replace the many point-to-point integrations currently in place. The solution implemented functions in a similar manner to the middleware often used to connect business applications with operations management applications.
Many plants in the chemical industry find it challenging to get the needed data apart from pure process values from the field to the control system. For example, some plants have a hard-wired physical layer (such as intrinsically safe barriers) that makes it difficult to get the data from the plants.
Data must have context to be useful. A coded tag name may have meaning for on-site personnel, but probably not for a remote expert. Instead, a descriptive tag name that provides location, plant, equipment, and process function makes it quicker and more efficient for remote personnel to identify the various assets and apply analytics. In cases where different naming conventions are used, a data platform that can connect to multiple data sources and map the data to a uniform, enterprise-wide naming convention can be helpful. This is one of the functions of an information broker. Often, these conventions are structured in a hierarchical manner similar to the physical assets and called a data model.
Once the data repositories are connected and tag names standardized, the data must be made available globally. When a user searches for information, the source should be transparent. The data broker must identify and retrieve the data from the location or application where it resides. For assets geographically dispersed over large distances, regional replication of the data could speed up these name-and-retrieve searches.
Using native visualization from smart sensors, devices, and applications can lead to lots of different digital screens and dashboards. Ideally, the data platform should provide visualization using standardized dashboards and screens to reduce the learning curve and cognitive load.
Deploying the data platform on a global scale presents additional challenges. These include cybersecurity issues such as endpoint security, user authentication, and complying with the different country regulations that might apply. Large-scale global deployments are also likely to present challenges relative to: application performance, availability and reliability of data for demanding real-time applications, high initial costs, high lifecycle and maintenance costs, and the ability to design and implement global standards for different business units with different needs.
BASF now uses a data platform to connect information from different data sources, including legacy historians, spreadsheets, and new sensors. This platform enhances the company’s ability to analyze data and provide users with much-needed information.
Dr. Krauss shared the observation that when selecting the platform for BASF, he found that IT providers often lacked manufacturing domain knowledge. On the other hand, the manufacturing suppliers often appeared to lack adequate IT competency.
Ultimately, BASF selected the data platform from inmation, an industrial system integration middleware supplier based in Germany. The two companies have been working together for over two years to create new and innovative data management capabilities to support asset lifecycle management.
inmation provides real-time, bi-directional connections using single-port TCP/IP. This aligns well with the BASF IT organization and its system integration standards. The solution prioritizes the transport of compressed and encrypted data to run over BASF’s WAN VPN in close to real time. The inmation product provides a multi-layered information broker to decouple BASF’s multitude of data sources from the array of data-consuming applications.
The company’s infrastructure-solutions for infrastructure (“system:inmation”) and enterprise-wide deployments including data-driven dashboards (“enterprise:inmation") are based on the NoSQL MongoDB database. This can handle a wide array of data types (time series, text information, alarms or events, etc.) and set up and replicated very quickly in different world regions to speed access for local users.
In addition to this core capability, the solution embeds technologies such as data-driven digital dashboards, HTML5, and streaming analytics in combination with inmation’s KPI visualization partner, Transpara.
The BASF use cases to date include:
Predictive maintenance enabling access to global asset data. A rollout is currently in progress.
Connectivity from basic automation to MES applications is working up to almost 100 percent data availability across BASF’s global fleet (up from 85 percent for some remote sites)
The enterprise:inmation solution is currently installed and working at BASF sites on four continents, distributed over 50 computers, services dozens of facilities worldwide, and connects with hundreds of different distributed BASF data sources. Going forward, BASF will use inmation as a key component for the company’s global predictive maintenance platform. BASF also plans to expand the solution into many other manufacturing intelligence use cases.
According to Dr. Krauss, BASF has resolved many of its challenges relative to accessing and interpreting some operations and manufacturing data, but in terms of data availability, contextualization, and scalability, the new data layer provides a solution for integrating the data efficiently and effectively.
An effective data platform can help streamline digital transformation for manufacturing companies. For smart manufacturing, smart factory, Industrie 4.0 and similar initiatives; people, machinery, plants, logistics, and products need to communicate and cooperate easily. To connect these diverse data sources, a unified, flexible, high-performance system is needed to provide company-wide, real-time data and information flow. Based on BASF’s experience, it appears that globally networked solutions for manufacturing require both advanced manufacturing and deep IT know-how and that the quality of the outcomes of industrial analytics applications strongly depends on the availability of data and their context.
ARC recommends that industrial organizations considering using a data platform to make OT data available globally throughout the enterprise should look for a solution or solutions that:
Supports Industrie 4.0, Open Group Automation and Smart Manufacturing initiatives and similar standards that may affect the industrial data platform market
Supports standards such as OPC Unified Architecture, XML, and both structured and unstructured data and connects with a wide array of applications and equipment
Guarantees high availability and data interpretation of the data via a data broker and data model
Enables excellent process visualization and digital dashboards in real-time
Easily connects legacy systems and other data sources and is scalable across the enterprise
ARC Advisory Group clients can view the complete report at ARC Client Portal on New Client Portal or Office 365 or Box.com on this website.
If you would like to buy this report or obtain information about how to become a client, please Contact Us